www.magazine-industry-usa.com
27
'12
Written on Modified on
Maple helps engineers design propulsion systems for some of the world’s biggest ships
Ships keep the global economy moving. Whether they are ultra large crude carriers transporting oil from the Middle East, container vessels transferring manufactured goods from Asia or car carriers shifting vehicles from factories in Europe, the global maritime industry moves around 32 trillion tonne-miles of cargo every year, four times more than it did at the end of the 1960s. To deliver this dramatic increase in cargo, the industry has had to change drastically over the past few decades. Vessels have become larger and more efficient as shipping companies work strenuously to keep costs down in the face of rising and ever more volatile fuel costs. For marine engineers, that means constant pressure to refine the performance and reliability of vessels and their systems. Nowhere is that pressure felt more acutely than in the most fundamental component of any modern powered vessel: its propellers.
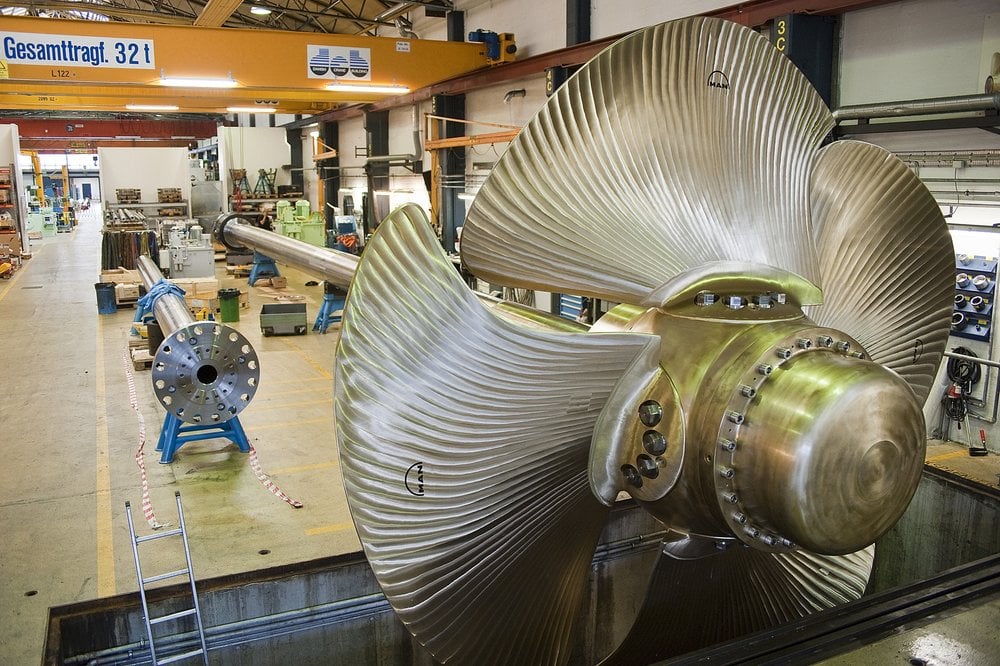
In cooperation with Rudolf Diesel, considered the father of the diesel engine, MAN produced the first diesel engine in 1897. The company has been manufacturing propellers for ships since 1902 and has designed, manufactured and supported more than 7,000 propeller plants.
Modern controllable pitch propellers, like the MAN Alpha CPP range, improve the efficiency and manoeuvrability of marine vessels. In propellers of this design, the angle of the blades is controllable, always providing the optimal match between the speed of the engine and the ship, thereby maximizing propulsive efficiency and permitting precise control of the vessel’s speed. This is important when manoeuvring into a port, for example. The blades can even be set to provide reverse thrust, which eliminates the need to install a separate reversing gear or use a reversible engine.
Mads Hvoldal is a mechanical engineer at the MAN Diesel & Turbo Propulsion Competence Centre division in Frederikshavn, Denmark. He works for the team that designs the mechanical and hydraulic control systems used to vary propeller pitch. “We produce a range of standard designs but it is the nature of the industry that many propulsion systems are engineered for specific vessels,” he explains. During peaks in demand for new vessels, development of hundreds of different designs per year is common. They need a software system that is robust and flexible.
“We start with the basic specifications, the available hydraulic oil pressure, the size of the propeller itself and the rate at which we need the blades to change pitch,” says Hvoldal. “We use those parameters to calculate the required sizes of components, both for standard parts like bolts and flanges and for the engineered components used in the system. We then pass those dimensions to our Pro/Engineer 3D modelling system for detailed design.”
The part sizing calculations are complex, taking into account the characteristics of the hydraulic control system and the properties of the materials used to make the final parts. They are also critical: transmissions need to perform well and operate reliably over long service lives in tough marine conditions. Shipping is also an intensively cost-competitive business, so over-sizing or over-engineering parts is not an option. After careful consideration, they chose Maple to help them in this complex design process. They chose Maple for its speed and accuracy.
“We started using Maple for our design calculations, replacing another mathematical software package,” explains Hvoldal. “The other system required us to transpose all the relevant equations from their original format into its own language before we ran the calculations. It was a time consuming process to write the translations by hand and then to check them.”
“I had quite a lot of experience using Maple in hydraulic systems design in a previous role,” he explains. “So I could see its potential benefits in our current work.” The critical advantage of Maple, he notes, is that the engineers can put the design equations in their original form right into the system. “That makes Maple faster to use, with reduced need to check and debug the code.”
MAN Diesel & Turbo, Propulsion Competence Center, Frederikshavn, has been using Maple for around six months and the power, speed and efficiency of the system has convinced its engineers that there is potential to expand their use considerably in the future. “So far, Maple has replaced our previous system for design calculations,” concludes Hvoldal, “But we are now exploring the feasibility of building standard models to simplify and automate the process further, and of automating the links between our initial calculations and the detailed part models in the 3D CAD system.”
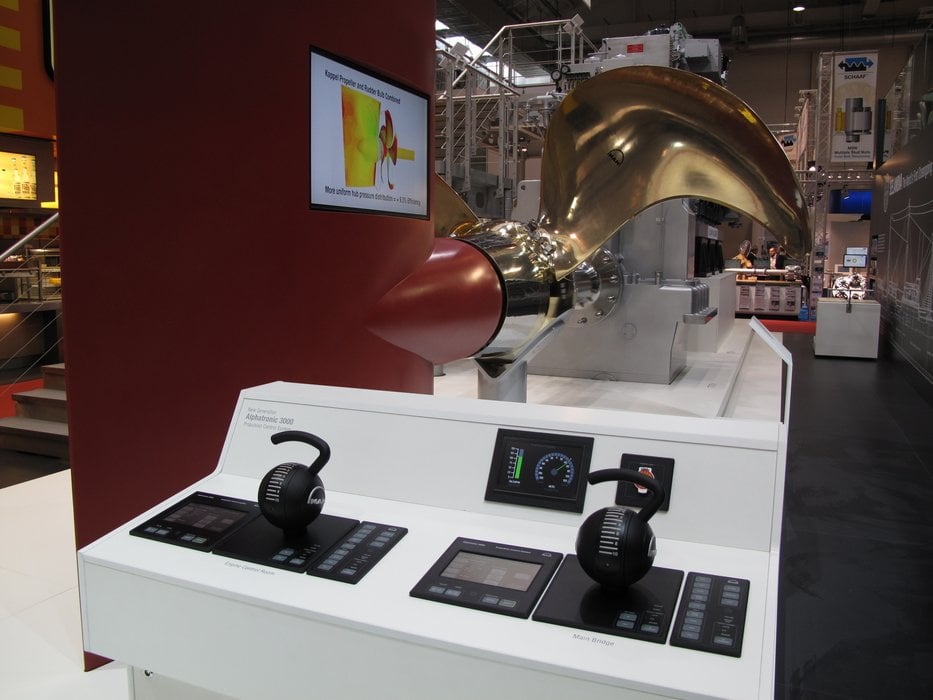
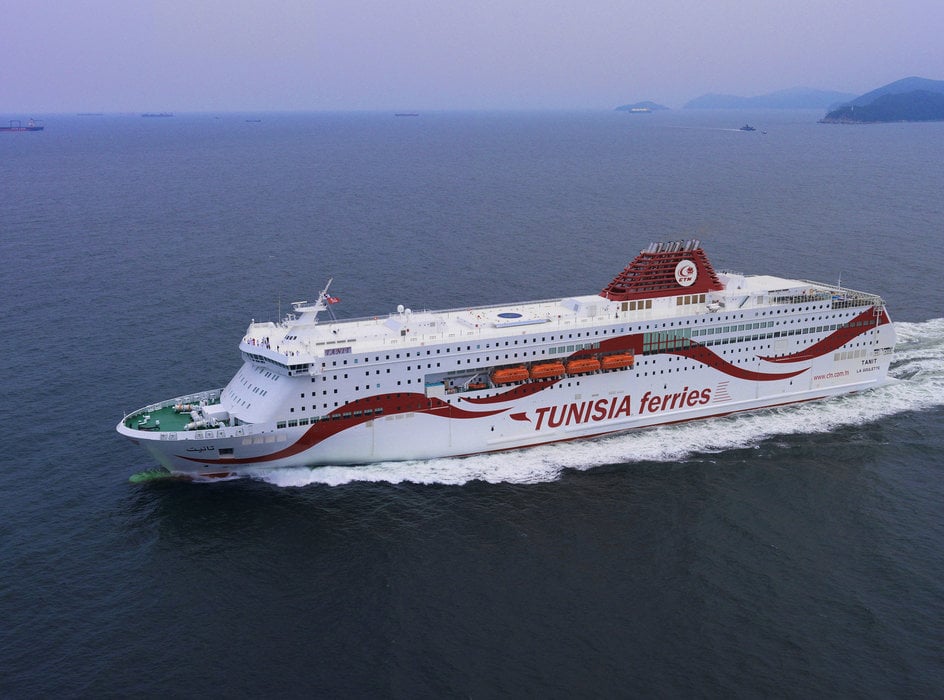