www.magazine-industry-usa.com
06
'20
Written on Modified on
It's the mix: GEA liquid jet mixers in use in the petrochemical and many other industries
More and more companies in the petrochemical and chemical industries rely on liquid jet mixers from GEA for their storage tanks, as recently a well-known major company in the petrochemical Industry did for its fuel and motor oil tank farm.
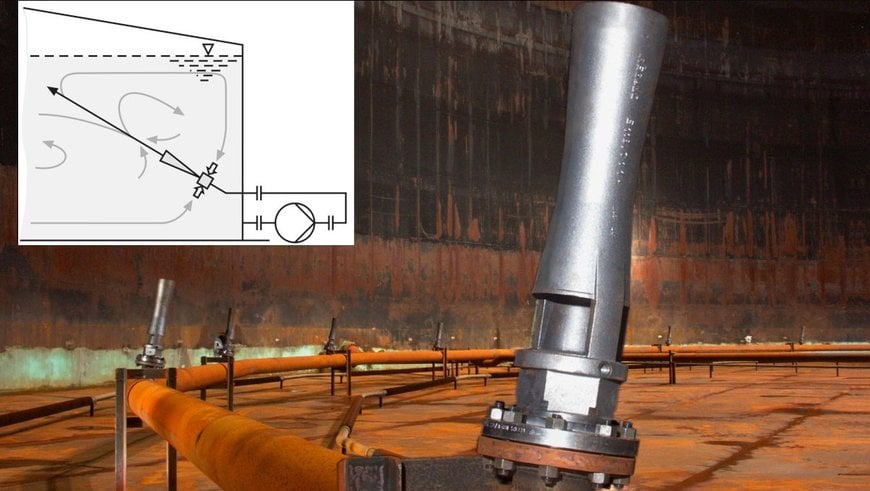
The customer uses GEA ejector systems to equip new tanks, to retrofit existing tanks and also for tanks that are specially used for testing new liquid products. An important aspect is the optimal design and arrangement of the jet mixers in the tank. All tank farms and storage facilities with GEA technology have two major advantages for customers: The mixing time has been reduced and the mixing quality optimized compared to previous mixing systems.
Jet pumps - a genuine high-performance technology - also a high priority in the Ariane project
Jet pumps, also known as ejectors, are devices for conveying, compressing and mixing gases, vapors, liquids and solids and for generating vacuum. The principle: A jet pump generates pumping action by a fluid jet (motive medium), which sucks in, accelerates and compresses/conveys another medium (suction medium) by impulse exchange. An ejector is usually a pump which generates a negative pressure, i.e. has a predominantly compressing effect.
Speaking of vacuum: GEA jet pumps have already been successfully used in vacuum generation in the European space project "Ariane" and the corresponding tests.
Jet pumps from GEA have a whole range of advantages. Basically, their simple design makes them particularly robust and low-maintenance and low-wear, as they have no moving parts and no internal drive and consist only of a motive nozzle, diffuser and head. Due to their relatively low mechanical stress, jet pumps can also be manufactured from thermally and chemically resistant special materials such as graphite. Furthermore, it is possible to achieve very high compression ratios with a high motive pressure. This is particularly decisive for vacuum technology. A very important, further advantage of jet pumps: because there are no rotating parts, they do not run hot and can therefore also be used in potentially explosive atmospheres. GEA jet pumps also have an advantage when it comes to installation: their design makes them very flexible in terms of installation and mounting.
Rigorous testing in the GEA test laboratory in Karlsruhe
All GEA ejectors operated with motive steam are thoroughly tested here. The research results of all GEA ejectors examined were entered into a huge database. With the help of this database, GEA can obtain important information for improving the mechanical design. These "heart and kidney" tests also help to underline GEA's reputation as a reliable partner and experienced technology expert in jet pumps.
The GEA approach: close to the customer and working together to find the best, specific solution
An ejector or an "off-the-shelf" liquid jet mixer is rarely available. GEA works intensively with its customers, because every tank and every plant is different. Many customers already have their tanks or plants in place or dimensioned. In most cases, the nozzles for the connections are already installed. In the case of liquid jet mixers, the customer is also advised and supported on request in the optimum positioning and alignment of the liquid jet mixers in order to optimize the mixing process. The mixing quality and mixing time must be right.
Customers need help with the choice of power as well as the choice of motive current and motive pressure. GEA experts look at the parameters of the customer's equipment to assess the extent to which the liquid jet mixers can best be modified and operated. The focus is always on how the customer's system or GEA ejectors can be adapted to achieve the best results with GEA ejectors. The GEA experts benefit from the experience gained from tests in the GEA test laboratory and from the records of earlier tests that have been documented over decades.
Modern techniques for flow simulations in use
GEA uses CFD (Computational Fluid Dynamics) simulations to analyze the flow conditions and mixing effects in tanks to optimize the design and arrangement of the jet mixers. The aim is to achieve the best mixing result for the customer and to avoid potential problems in mixing processes before they arise in reality.
New info video arouses great interest
GEA developed an information video to visualize the functionality and possible applications of jet pumps. It shows briefly and very clearly what an ejector is and how diverse the fields of application are:
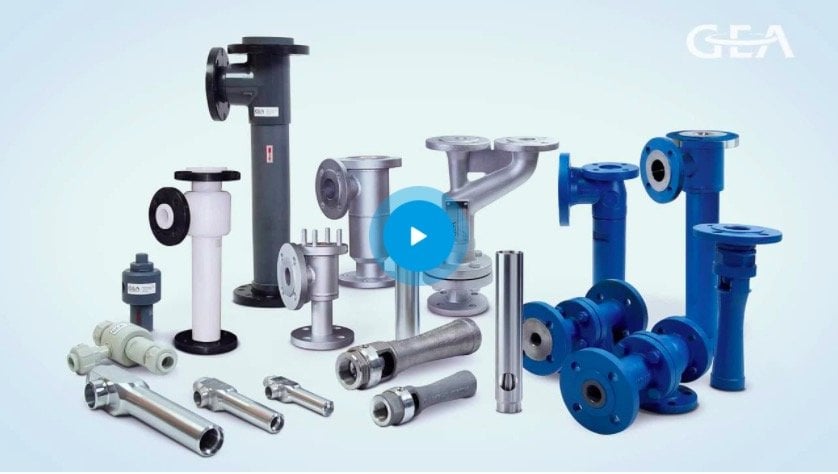
video.gea.com
www.gea.com