www.magazine-industry-usa.com
22
'12
Written on Modified on
Modern techniques bring system-level modeling to the automation industry
Philipp Wallner, Global Technology Manager, Bernecker + Rainer Industrie and Johannes Friebe, MapleSim Europe Director, Maplesoft
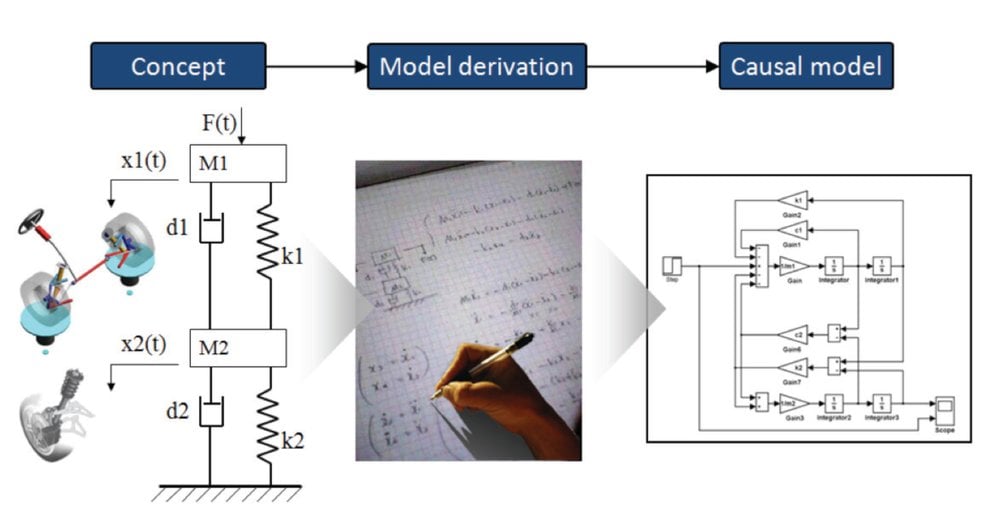
MapleSim and B&R Automation Studio
Designing an adequate machine or system model plays an important role in simulation-based development. MapleSim is an advanced physical modeling and simulation tool that applies modern techniques to dramatically reduce model development and analysis time while producing fast, high-fidelity simulations. However, the model is only the beginning of the story.
B&R Automation Studio is an integrated engineering development environment that allows the controller, drive, communication, and visualization phases of a development project to all be configured in a single environment. Through the use of an add-on product, the MapleSim Connector for B&R Automation Studio, physical models designed in MapleSim can be easily transferred to the B&R controller hardware. They can be used immediately for hardware-in-the-loop simulations that emulate the machine's behavior in real time, in a completely safe testing environment.
MapleSim has a graphical interface for model creation similar to well-understood system schematics. This means that knowledge of the model structure is often enough to create a physical model that runs in Automation Studio on B&R hardware. This process, illustrated in Figure 2, also results in system-level models that are easy to understand, allowing for faster and more efficient collaboration on projects.
MapleSim also provides system equations in full symbolic form. This helps to automate the cumbersome calculation of motion paths in solving inverse kinematics problems.
Example Application: B&R Reaction Wheel Pendulum
The inverse pendulum is a well-known example that demonstrates system-level modeling and closed loop control strategies. Here, B&R’s Reaction Wheel Pendulum rig is used as the basis to create a MapleSim model of the inverse pendulum, as seen in Figure 3. Creation of the MapleSim model is fast and simple, and it can then be seamlessly exported to B&R Automation Studio to validate the model and test control strategies.
The plant model uses MapleSim’s extensive 3-D multibody component library, including rigid beams, masses, and revolute joints. A moderately experienced MapleSim user can typically develop models of this complexity in minutes.
In this first test case, the model code is generated and exported along with the necessary solver, a process illustrated in Figure 4. Code generated using the MapleSim Connector for B&R Automation Studio is royalty free and is owned by the user. This tool converts the fundamental differential equations of motion generated by the model to Automation Studio-compatible C code. MapleSim also applies unique symbolic code optimization that accelerates the run-time speed without reducing model fidelity.
Using this efficient process, the actual modeling, coding, and implementation time can be on the order of minutes. The dramatic speedup in workflow is possible due to the intuitive nature of modeling in MapleSim along with its automatic code generation capabilities. With the MapleSim-generated C-Code ready for integration with Automation Studio, the final step is to validate the MapleSim plant model on the actual hardware platform via the existing Automation Studio workflow.
System-Level Modeling in MapleSim
MapleSim combines advanced technologies such as physical modeling techniques, symbolic computation, and Modelica® to provide multiple advantages for system-level modeling:
• Rapid, easy development of complex physical models, including multidomain and multibody applications
• Automatically-generated, accessible model equations, leading to models that are fully parametric and easy to analyze
• Advanced analysis through an extensive programming language and design documentation environment
• Highly optimized code generation facilities for plant models
• Support of the Modelica modeling standard as well as select, specialized modeling frameworks for advanced application areas
From an architectural perspective, MapleSim is a modeling environment connected to the well-known technical computing software, Maple (Figure 5). Maple provides a powerful symbolic mathematics engine that efficiently manipulates the expression and algebraic structure of equations. This means that engineers can work with the mathematics without any approximations or simplifications, and in an automated, error-free environment.
Mathematically, MapleSim models are generally governed by ordinary differential equations (ODEs) or differential algebraic equations (DAEs). MapleSim includes the option of quick, direct input of mathematical equations to define custom components.
MapleSim also provides additional levels of equation and code preprocessing to minimize the required computational load during the simulation. Consequently, MapleSim has the capability of producing very fast code but also very robust code, as the mathematical simplification inherently reduces complexity.
Conclusion
Combining MapleSim and B&R Automation Studio allows for the efficient implementation of system-level modeling into the B&R toolchain. The real power and potential, however, is in the larger concept that is embodied in this initiative. By adding an easy-to-use and cost-effective system-level modeling phase to the automation workflow, engineers will soon be able to increase the level and sophistication of virtual simulation and testing prior to hardware commitments.
Maplesoft, MapleSim, and Maple are trademarks of Waterloo Maple Inc. Modelica is a registered trademark of the Modelica Association.
Figure 1: The traditional workflow for system-level modeling
Figure 2: MapleSim’s modern approach to system-level modeling is more efficient and intuitive
Figure 3: The Reaction Wheel Pendulum rig and the MapleSim system model
Figure 4: Generating C-Code from a MapleSim model and deploying it on a B&R PLC or industrial PC.
Figure 5: Using Maple, you can solve technical computational problems faster in a more intuitive way
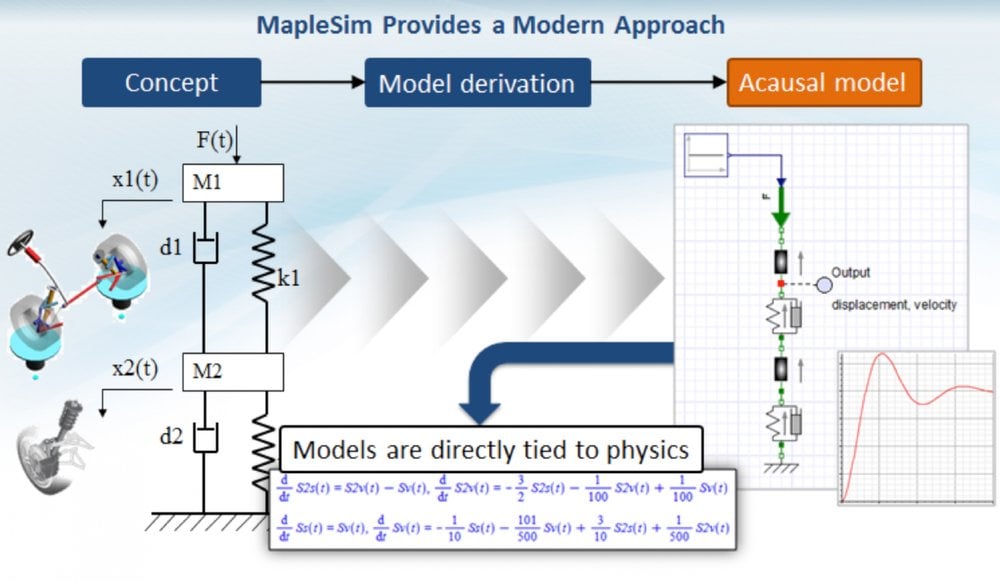
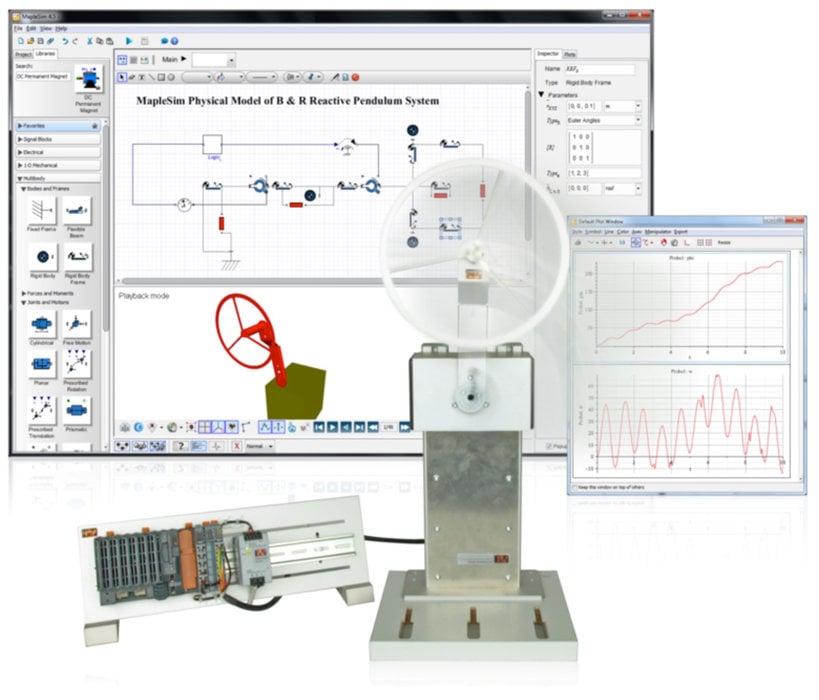
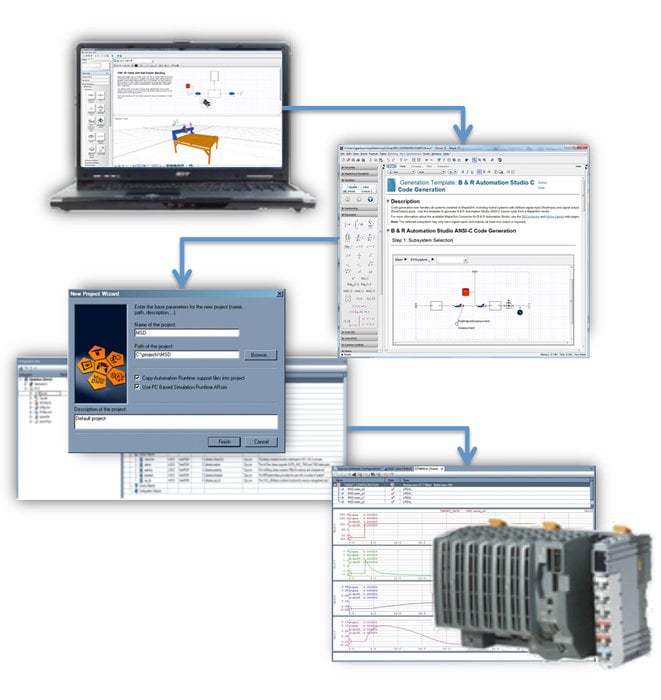
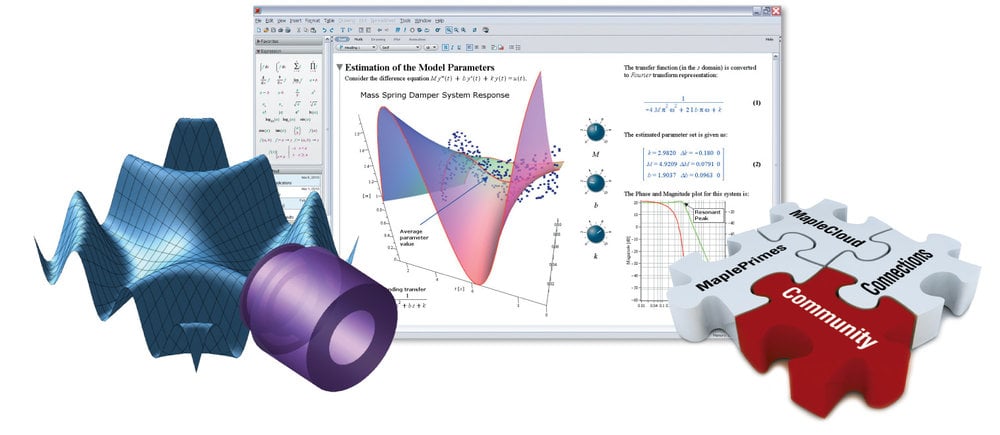