www.magazine-industry-usa.com
01
'12
Written on Modified on
“Innovations in all segments”
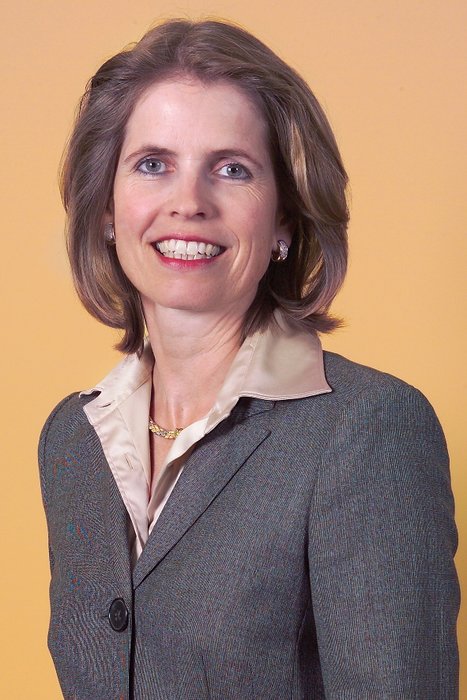
Jutta Humbert, Managing Director, NORD DRIVESYSTEMS, and
XXX name of local manager, function, company name, country XXX
With a wider than ever range of frequency inverters, additional energy-saving motors, more new industrial gear units, and hygienically optimized systems as a development priority, NORD DRIVESYSTEMS has entered 2012. It is the stated goal of the company to consolidate its status as the number two full-scale drive technology supplier. Jutta Humbert and XXX name of local manager XXX from the management team of the North German drive manufacturer speak about current innovations and outline the group’s strategy.
Ms Humbert, XXX Mr/ Ms (name of local manager) XXX, how do you aim to score points in the drive market this year?
Jutta Humbert: For one thing, through strategic company planning and branding. We are continuously strengthening and expanding our global presence. And it is important to us to establish “NORD DRIVESYSTEMS Group” as the consistent name for our global group. But obviously it will also be our technological innovations which will attract attention this year. You will find new products and improvements in all segments of the NORD portfolio.
XXX name of local manager XXX: One of our priorities in 2012 is the ongoing expansion of our electronics range. Both in the control cabinet inverter range and with distributed systems we are adding new, higher-performance models. In addition to that, the increasing energy savings regulations for motors in all markets require adequate new solutions. For instance, we now supply IE4 systems with power ratings up to 7.5 kW. In the gearbox division we have recently announced smaller models from our successful line of industrial gear units: in addition to the 60,000 to 220,000 Nm models, there are now also units with output torques from 25,000 to 50,000 Nm.
Ms Humbert, you mentioned a new name – “NORD DRIVESYSTEMS”. Please tell us, what is that about?
Jutta Humbert: With NORD DRIVESYSTEMS we establish an international umbrella brand for our group of companies. This communicates our key competence as a global full-range supplier consistently and more recognizably than was previously possible with the diverse names of our many German and international subsidiaries. In parallel, the existing names of the local companies remain, for example “Getriebebau NORD GmbH & Co. KG” at our German headquarters. But the parent company as well as every one of our companies worldwide is a “Member of the NORD DRIVESYSTEMS Group”, and they all use that label with their names. The name signifies how far we have come since the founding days as a gearbox manufacturer. Today, we supply full-scale drive solutions. In this sector, we hold a secure second rank. We are very satisfied with the continuous growth of the NORD group.
The period since the introduction of the euro must have been a success story for the entire German economy. Has NORD’s development been special?
Jutta Humbert: We are among the leaders in terms of dynamism, owing in part to our anti-cyclical investment strategy. Last year, our gross sales approximated 412 million euros, starting from 151 million in 2000. I would say that such figures are remarkable even in an environment as successful as that characterized by medium-sized German enterprises. Our wide vertical range of manufacture remains extraordinary, even in comparison to the competition – from pinions to windings and circuit boards we manufacture everything in our own factories. And of course, looking at just the last decade, we have kept on setting technological milestones with innovations such as the latest generation of our aluminum NORDBLOC gears. And the momentum stays high. We expect to grow at the same rate in the present decade.
Let us turn to product innovations! XXX Mr/ Ms (name of local manager) XXX, since you have highlighted the electronics division, what novelties can NORD show?
XXX name of local manager XXX: One of the most recent additions to our frequency inverter program took place with the SK 200E family of distributed inverters which now boasts models with up to 22 kW output. Furthermore, we now provide SK 500E cabinet inverter models up to size 10 for up to 132 kW. Another new model in this series is the top-of-the-line SK 540E inverter that supports the free programming of drive-related functions according to IEC 61131. There are a few pilot applications which we will publicize throughout the year. All our inverters – from the basic models in each line to those with the most extensive functionality range – use the established, very fast ISD current control technology which ensures constant speed under changing loads and provides for very high torques during start-up. Even with the low-price units, you can realize highly precise applications. If, however, your application requires servo-like performance, conventional three-phase technology also provides a solution: just select one of the advanced functions models from our inverter range and implement speed or position control with the respective encoder systems.
Energy-saving motors seem to be an important cue, since you already mentioned them before. Could you go into detail?
XXX name of local manager XXX: Currently, our most efficient new units are size 80 to 100 IE4 motors with a 0.55 to 7.5 kW output. In addition to that, we supply IE3 motors up to size 180, and for the same range – size 80 to 180 – we provide ATEX versions of our globally available IE2 motors.
Ms Humbert, am I mistaken or has the original NORD mainstay, the gearbox segment, lost importance in the face of all these innovations in the electronics and motor divisions?
Jutta Humbert: Oh no, you are very much mistaken! Of course, innovative gearboxes with the reliably high quality we have been known for for almost five decades remain our core competence. XXX Mr/ Ms (name of local manager) XXX has mentioned our line of industrial gear units – after all, we did not expand that line at random, but because it was so successful that we almost had no other choice. There was an immense demand for additional models smaller than the performance range we initially launched. This year, we are well positioned to meet that demand with our expanded range of models.
Why, do you think, are these industrial gearboxes in so much demand?
Jutta Humbert: Certainly because they provide a special combination of useful advantages. The standard unit can be upgraded with various options. For use in conveyor applications, for example, one can directly mount an auxiliary drive. In general, users can choose from a very adaptable modular system in order to quickly and comfortably configure their customized gearbox. For many users it is also very important that one standard enclosure per size covers the entire range of transmission ratios, and of course, short delivery times for customized versions anywhere in the world.
XXX name of local manager XXX: Moreover, we are continuously improving that line. We have increased the transmittable torque by about 15 percent and further improved the thermal power limit.
XXX Mr/ Ms (name of local manager) XXX, finally, let us now talk about the “hygienic systems” for the food industry. What have you developed for this sector?
XXX name of local manager XXX: We looked for the “cleanest solution”, so to speak, and we found it with our washdown gear units, the new two-stage helical bevel gear units which complement our successful NORDBLOC.1 gearbox series. Cleaning liquids can be easily washed off in all installation positions since all external surfaces have been designed with wide radii and the overall construction has no indentations or dead spaces. We supply these extremely robust gear units in five frame sizes with torques ranging from 90 to 660 Nm.
So much said about hygienic helical bevel gearboxes. Are there any other gearbox innovations this year?
XXX name of local manager XXX: Yes, in fact we have also just revised our series of worm gear units, for example. The latest versions are now designated as SMI. Incidentally, this is still very close to the subject of “clean solutions”. Once again we have improved the design of the casings and given the gearboxes very smooth surfaces which enable optimal and particularly easy cleaning. By the way, when we deal with hygienically sensitive devices, the gear cases are not coated. Instead, we give the aluminum gear casings a special treatment that endows them with characteristics comparable to stainless steel. We call this technology NSD tupH. A catalytic process makes the surfaces of an aluminum gear case about seven times harder than before.
Why should I choose such a treated gearbox in preference to a stainless steel one or a model with special varnish?
Jutta Humbert: Because generally the stainless steel version is usually only available in the few types offered by your supplier. In contrast, we offer the NSD tupH treatment for a very broad range of products. You have a practically free choice of gear units, as long as they are aluminum models. Also, this solution is much lighter because the basic material weighs significantly less than steel, which is a further advantage. And if you consider a varnished gear unit or one with a protective coating as an alternative, you must be prepared that the surface, whether it be varnish, nickel, or a nickel-Teflon composite, could of course peel off. When the coating has been damaged, at any rate, that danger can never be completely avoided. With NSD tupH gear units this is impossible. The treated surfaces are scratch-proof, very resistant, and do not corrode.
Illustration 1: Jutta Humbert, Managing Director at NORD DRIVESYSTEMS
Illustration 2: XXX name, function, company name XXX
Illustration 3: The new top-of-the-line model in NORD’s cabinet inverter program
Illustration 4: NORD manufactures enhanced-efficiency motors complying with current energy-saving regulations
Illustration 5: A host of benefits for hygienically demanding applications: washdown gear units with special surface treatment