www.magazine-industry-usa.com
06
'19
Written on Modified on
Microfactory driving Local Motors
Additive manufactured tools and a revolutionary production model are helping bring electric vehicle automaker Local Motors nearer to its vision of a cleaner, more sustainable future.
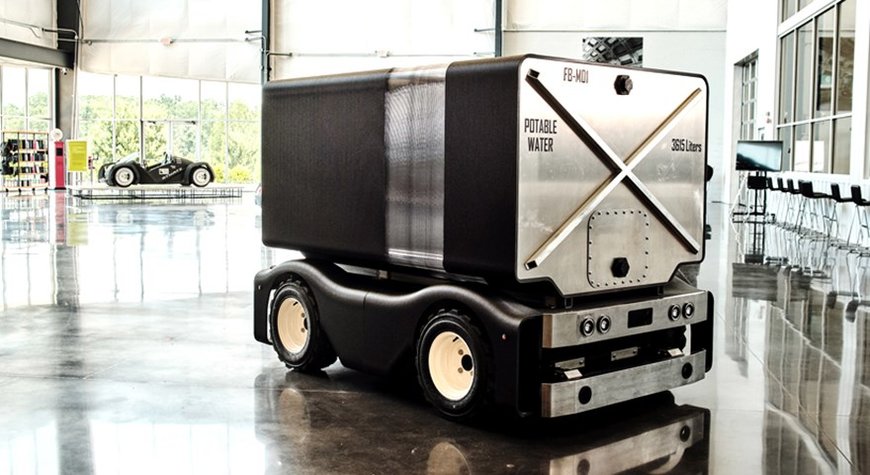
Electric vehicles (EV) are nothing new. What is new are autonomous electric vehicles that are produced on a massive 3D printer, then assembled by a small team of workers in a “microfactory”, a facility no larger than the nearest big box store. What’s more, these futuristic vehicles are often customized to the specific needs of the people or companies buying them.
Just like Olli, a shuttle bus that promises not only to change the face of transport as we know it, but also to revolutionize the way automakers everywhere design, produce and market their wares.
The driverless shuttle was introduced at the 2018 International Manufacturing Technology Show (IMTS) in Chicago, and the vehicle’s manufacturer, Arizona-based Local Motors, has a history of similarly audacious acts. At IMTS 2014, the automaker built the world’s first 3D-printed car – the Strati – on the floor of the convention centre. On the show’s final day, Local Motors founder Jay Rogers and Association for Manufacturing Technology president Douglas Woods took the car for a spin.
Breaking the mold
Since its inception in 2007, Local Motors has given us the Rally Fighter, the first co-created production car, as well as the XC2V (an “experimental crowd-sourced combat-support vehicle”), the Verrado electric-powered drift trike, and the “completely customizable” and co-created LM3D Swim roadster. Perhaps most exciting of all, it gave us the Domino’s DXP (stands for “delivery expert”), touted as the “ultimate delivery vehicle” for pizza. All were collaborative efforts, and all broke the mould of traditional manufacturing.
"We have a lot of creative brainstorming sessions with the team and make decisions based on science and available data"
Yet this story isn’t so much about machining as it is about vision – a vision for a cleaner, more sustainable future, investment in our communities and an entirely new paradigm for making things, all of which begins with the microfactory concept.the CoroMill 390 milling cutter helped Local Motors reduce the weight of the cutter to improve performance at long overhangs.
“I grew up in East Tennessee,” says Billy Hughes, Local Motors’ research and development programme director. “We have a culture of community here, and our microfactory in Knoxville partakes in that culture. We use locally sourced components, such as batteries and aluminium substructures whenever possible, and many of our employees are like me: they’re from around here and understand the area. That’s what the local in Local Motors means – to be part of the local community and help the people who live there.”
A new, sustainable production standard
Microfactories don’t eat up huge tracts of land the way traditional factories do, Hughes explains, but rather they help to revitalize communities by repurposing empty buildings, often turning what was a failed business venture into a vibrant, forward-looking commerce partner and provider of high-paying technical jobs. Microfactories are also far more flexible than their large counterparts; where a typical car or truck takes years to develop and a month or more to build, Local Motors can turn around a customized vehicle in weeks.
"We want to connect with and scale to the community, not build massive quantities of products to be shipped off elsewhere"
Hughes attributes much of this agility to direct digital manufacturing, or DDM, a technology that includes 3D printing but goes much farther. For instance, the Local Motors design and engineering teams leverage the latest in CAD simulation and other software tools and, according to Hughes, are always on the hunt for better mousetraps. They spent several years developing proprietary, carbon-fibre-reinforced materials so that Olli is both safe and structurally sound. They also collect and analyse data – not only from the manufacturing floor but from the delivered vehicles as well – and use it to continually improve their processes and products.
“We have a lot of creative brainstorming sessions with the team and make decisions based on science and available data,” Hughes says. “For example, we’ll use small-scale printers to create a concept car, then discuss ways to improve it. We’re constantly striving for simplicity of design, which is a big reason our vehicles contain only 40 to 50 parts, instead of several thousand.”
www.sandvik.com