www.magazine-industry-usa.com
20
'20
Written on Modified on
UMS PRO: A new unflatness measurement system for SBL lines
Two measurements improve flatness by a factor of ten and reach almost no loss of material
With UMS PRO, Ungerer introduces a system for unflatness measurement of strip steel that combines the commonly used high tension and low-tension measurement methods. In conjunction with a high-speed controller, users obtain considerably improved coil flatness (by a factor of ten) after the stretch-bend-levelling unit (SBL). The measuring system can be easily retrofitted on almost all existing stretch-bend-levelling lines, even those from other manufacturers.
Low-tension or high-tension? Up till now, this has been the question that strip metal manufacturers have had to ask themselves when planning the purchase of a Stretch-Bend-Levelling (SBL) line (Figure 1). These machines produce a uniform flatness across the width of the coil. They equalize material and surface tensions and align the metal fibers with the levellers in such a way that key parameters such as yield strength and elongation can be optimally adjusted. The flat strips which are then wound into coils are must meet these quality requirements before they can be used in highly demanding applications.
Prerequisite: Precise measurement, fast control
The prerequisite for best levelling results is firstly the measurement of the real strip’s unflatness after levelling. Inventor of the actual levelling process, Ungerer is still an expert in SBL systems offering the market a worldwide presence.
In the machines from Ungerer the unflatness measurements are firstly made immediately at the leveller’s output with a rubberized roll made of high stiffness material with integrated piezo pressure sensors (high-tension method, see Figure. 2), The second flatness measurement of the strip is made at very low tension by a pull-down measurement roller as it comes out of the machine (low-tension measurement; Figure 3). In order to achieve a real time closed loop control, the sensors send their measurement results wirelessly via a PCM transmitter both to the PLC and to the UMS Pro controller specially developed for this application, which calculate and immediately send back the setpoint values to the leveller.
Low Tension: Good measurement results, long dead zone
The low-tension measurement takes place at the end of the process, after the coil has been unwound. Because the strip is then no longer under high tension, this measurement -called the pull-down measurement- delivers very precise results with a control accuracy of approx. 99%.
However, the measuring point here is 20 to 25 meters (on the strip path) behind the levelling zone, so a long dead zone must be considered. If we include the distance required for adjustment, there are always about 50 meters which lack the desired or required flatness, because the first feedback and the flatness measurement only take place after approx. 25 meters and the feedback from the second controller only reaches the pull-down roller after a further 25 meters. It can therefore be assumed that the strip of each coil is flat over a length of approx. 50 meters but does not lie within the tolerance range of 99% accuracy. This value is only reliably achieved when the leveller has accurately adjusted to the unflatness of the incoming material.
High-Tension: Fast action, inaccurate results
On the other hand, high tension measurement takes place almost immediately at the leveller’s output. Adjustment takes place quickly accordingly, and so, the loss of strip is really minimal. Since the strip is under high-tension, the results of the measurement and consequently of the levelling are not as accurate as with the low-tension measurement. It nevertheless achieves a control accuracy of approx. 95% immediately after the leveller unit.
Ungerer’s UMS PRO : an exclusive benefits from the advantages of both measurement systems
Thus, both measuring positions and methods offers advantages and disadvantages. The target of the Ungerer's developers has been then to enhance and keep the advantages of both methods: the minimal strip loss from the high-tension measurement, and the maximum accuracy from the low-tension measurement.
This goal was achieved by the combination of both methods and has been recently set to the market under the name UMS Pro. The measurement systems of both rolls (which are configured as master and slave) send their data to the central controller, which enables the parameters sending to the leveller in closed loop mode at high computing speed and which ensure that the strip is accurately stretched accordingly.
This brand new joint data evaluation allows the user to get the best of both methods without having to accept their respective disadvantages. In addition, if one of the two rollers is under maintenance, it is still possible to operate the machine.
This means that any lost production time for maintenance of the flatness measurement and control system is virtually eliminated. Ungerer's UMS Pro controller is the only one in the world that controls both systems, creating a flatness measurement system which is at the same time highly efficient and highly available.
Result: Flatness improvement by a factor of ten and measurement that is twice as fast
The improvement that this double measurement brings can be expressed in numbers. By measuring after the leveller, a flatness of 95 to 96% is already achieved, after the pull-down, it is 99%. The result is coils that are exactly flat and can be machined precisely. For example, it meets the requirements of manufacturers of premium smartphones who manufacture from the coils mobile phone housings and their components, such as slots for SIM cards.
Cooperation between two experts
The innovation of UMS PRO lies, on the one hand, in the idea of combining both measuring methods and, on the other hand, in jointly evaluating the data from both sensor systems. In this demanding task, Ungerer (a specialist in pull-down systems) worked together with BFI, the research institute of the Steel Institute VDEH and expert for pull-up measurements. Among other things, BFI has developed the controller that evaluates the results of both measurements, correlates them and determines the corresponding control parameters on this basis.
Also new is that measurement results are displayed in Windows 10 with Labview. The measurement report is available among other options as a "waterfall diagram" which shows exactly the flatness over the width and length of the coil and displays the results of both measurements to the operator at the same time. The picture shows the measurement report at one of the world’s leading manufacturers of stainless-steel thin strip. After the SBL process with UMS PRO, the 1550 mm wide strip achieves far greater flatness than in a rolling mill, which for physical reasons cannot be obtained with pure cold rolling (Figure 3).
Simple retrofitting of existing equipment
The UMS PRO system can of course be used in all new SBL systems from Ungerer and other suppliers. However, it's noticeable that it is also highly suitable for retrofitting on existing systems. From the mechanical side, it's clear that to replace only one roller in the stretching block with a sensing roller is enough to achieve the requested result.
ROI dependent on material value
The new double measurement technology of coils flatness has already been integrated by Ungerer in several SBL lines, both in existing, and in new lines in China, Korea, and Italy, among others. It has been proven in practice that it has then shown to result in the production of higher quality coils with lower material loss. The higher the price per kilogram of the material, the quicker the measuring process pays for itself.
Ungerer has developed a calculator that allows to quickly and easily estimate the "Return on Investment" for UMS PRO. As a rule of thumb, you can say: with thin stainless steel, the investment in the measuring system pays for itself after around three years. For copper coils it is as low as one year, and for titanium the payback period is even shorter.
www.ungerer.com
Figures/captions
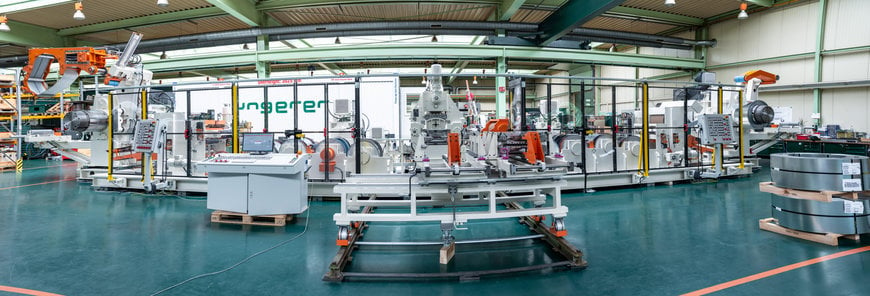
Figure 1: Ungerer's stretch-bend-levelling lines (SBLs) are in use all over the world.
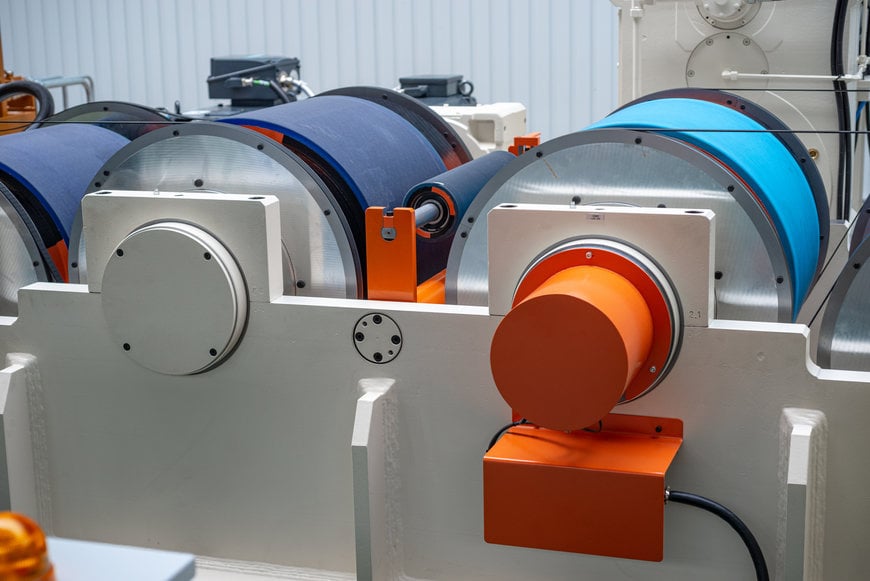
Figure 2: With UMS PRO, the unflatness of strip steel is measured twice and corrected within a very short time. The picture shows the first high-tension measuring station integrated in a roll made of solid material shortly after the leveller.
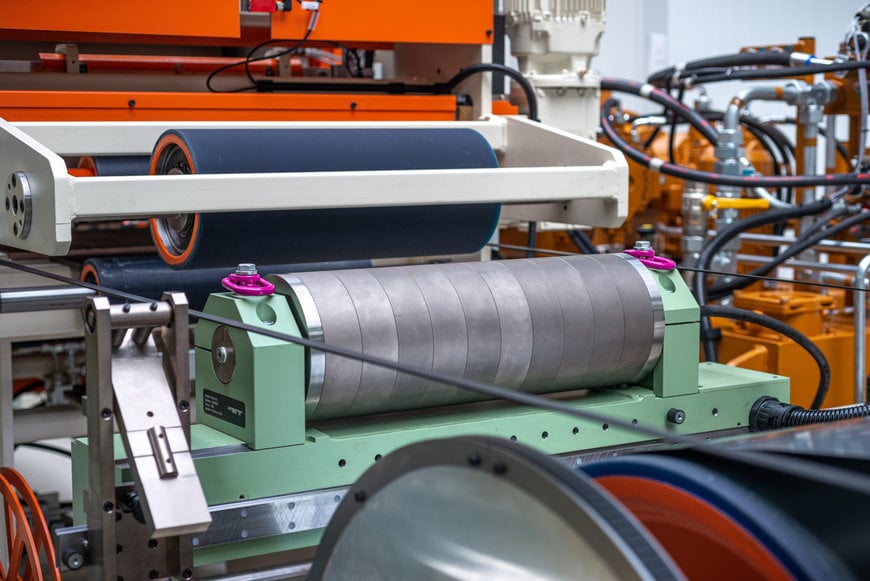
Figure 3: The second (low-tension) measuring station is located in the low-tension output area.
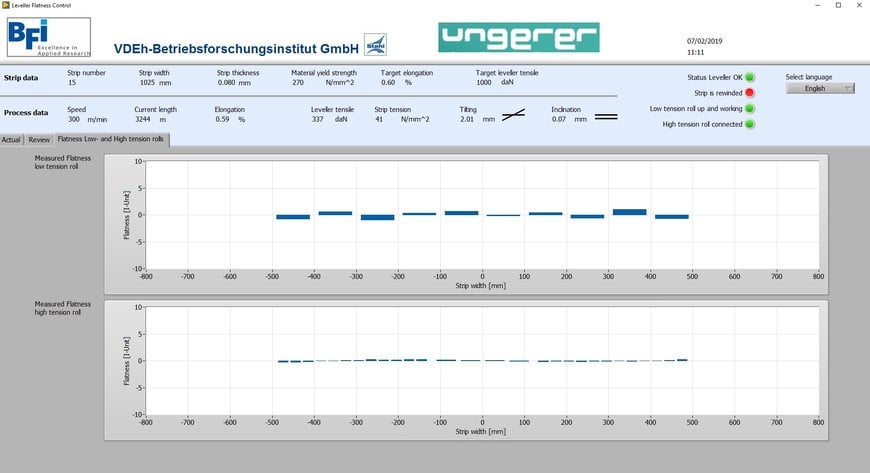
Figure 4: The combination of high- and low-tension measurement in combination with sophisticated control technology improves flatness by a factor of ten and minimizes strip loss.
Author: Klaus Lenz, CEO, Ungerer Technology GmbH, Pforzheim