www.magazine-industry-usa.com
28
'11
Written on Modified on
Cleancon: Innovative cleanliness concept for fasteners compliant with VDA 19
The VDA 19 guideline and the ISO 16232 standard define new requirements for the automobile industry for verifying technical cleanliness. To fulfil these requirements, manufacturers must identify and quantify any particle contamination that is present. The Cleancon® cleanliness concept from Arnold Umformtechnik goes a step further and provides a process that encompasses cleanliness requirements all the way from production to the customer application.
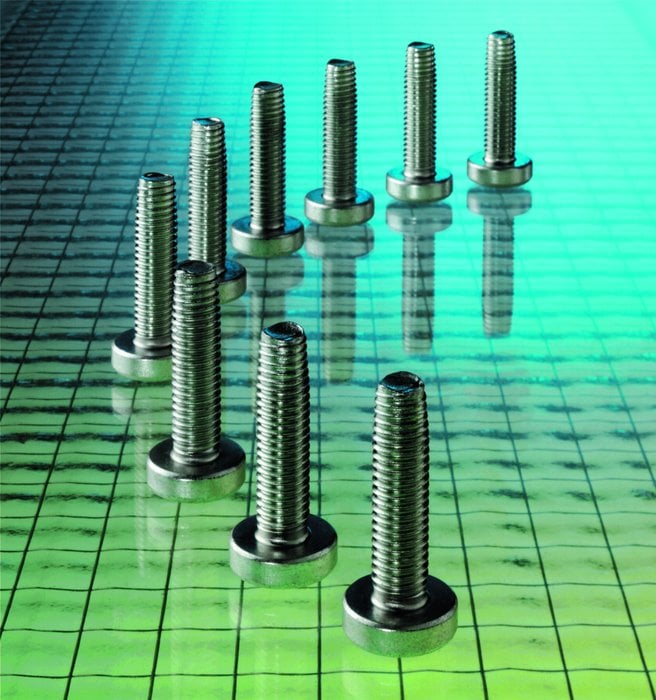
All OEMs currently rank electronics failures as the top cause of car problems. Consequently, the technical cleanliness of not only electronic components, but also pneumatic and hydraulic components (used in brakes, engines and chassis) is increasingly a matter of concern for the automobile industry. With the ongoing trend of increased performance and reduced size of units and modules, microscopic particles on component surfaces can easily cause malfunctions.
Arnold Umformtechnik offers a suitable solution in the form of its Cleancon® cleanliness concept.
The entire process consists of five steps:
-In the customer requirements profile, the limits are defined, the environment is analysed, surface and inspection specifications are recorded, and the packaging is specified.
-During production, the entire process is accompanied by cleaning processes.
-In the cleanroom, the parts are microcleaned, anti-friction coatings are applied as necessary, and the components are packaged.
-In the VDA 19 compliant cleanliness analyses, an adapted extraction method is used and the particle size distribution and gravimetrics are investigated.
-Finally, the components are placed in Cleanpack multi-layer packaging to preserve cleanliness, with an internal layer that secures the components and an outer layer that can be printed or marked according to individual requirements.
No external service provider necessary
Arnold Umformtechnik’s system eliminates the need for an external specialist firm that microcleans the fasteners before they are used in assembly.
A comparison of the Cleancon® process to the conventional process leads to a clear conclusion: the number of metallic particles is reduced dramatically. This is accompanied by improved assembly security and the opportunity for further component miniaturisation, which translates into higher power density and smaller structures.
Success factor of the new cleaning process
A new cleanroom design provides conditions similar to those of a high-class cleanroom. This is where the fastener components come at the end of the production process for microcleaning using advanced equipment, for the application of anti-friction coatings immediately after cleaning, and for cleanliness-preserving packaging in Cleanpack containers. The latter two operations safeguard component cleanliness against the effects of external downstream process steps. The special internal layer of the Cleanpack packaging provides antistatic protection and mechanically secures the components so they cannot move relative to each other during transport (unlike bulk transport), putting an end to post-production particle contamination.
Arnold Umformtechnik offers a suitable solution in the form of its Cleancon® cleanliness concept.
The entire process consists of five steps:
-In the customer requirements profile, the limits are defined, the environment is analysed, surface and inspection specifications are recorded, and the packaging is specified.
-During production, the entire process is accompanied by cleaning processes.
-In the cleanroom, the parts are microcleaned, anti-friction coatings are applied as necessary, and the components are packaged.
-In the VDA 19 compliant cleanliness analyses, an adapted extraction method is used and the particle size distribution and gravimetrics are investigated.
-Finally, the components are placed in Cleanpack multi-layer packaging to preserve cleanliness, with an internal layer that secures the components and an outer layer that can be printed or marked according to individual requirements.
No external service provider necessary
Arnold Umformtechnik’s system eliminates the need for an external specialist firm that microcleans the fasteners before they are used in assembly.
A comparison of the Cleancon® process to the conventional process leads to a clear conclusion: the number of metallic particles is reduced dramatically. This is accompanied by improved assembly security and the opportunity for further component miniaturisation, which translates into higher power density and smaller structures.
Success factor of the new cleaning process
A new cleanroom design provides conditions similar to those of a high-class cleanroom. This is where the fastener components come at the end of the production process for microcleaning using advanced equipment, for the application of anti-friction coatings immediately after cleaning, and for cleanliness-preserving packaging in Cleanpack containers. The latter two operations safeguard component cleanliness against the effects of external downstream process steps. The special internal layer of the Cleanpack packaging provides antistatic protection and mechanically secures the components so they cannot move relative to each other during transport (unlike bulk transport), putting an end to post-production particle contamination.