www.magazine-industry-usa.com
14
'19
Written on Modified on
Product customization: Dürr enables fully automated painting of cars in two colors for the first time
A quantum leap in two-tone painting.
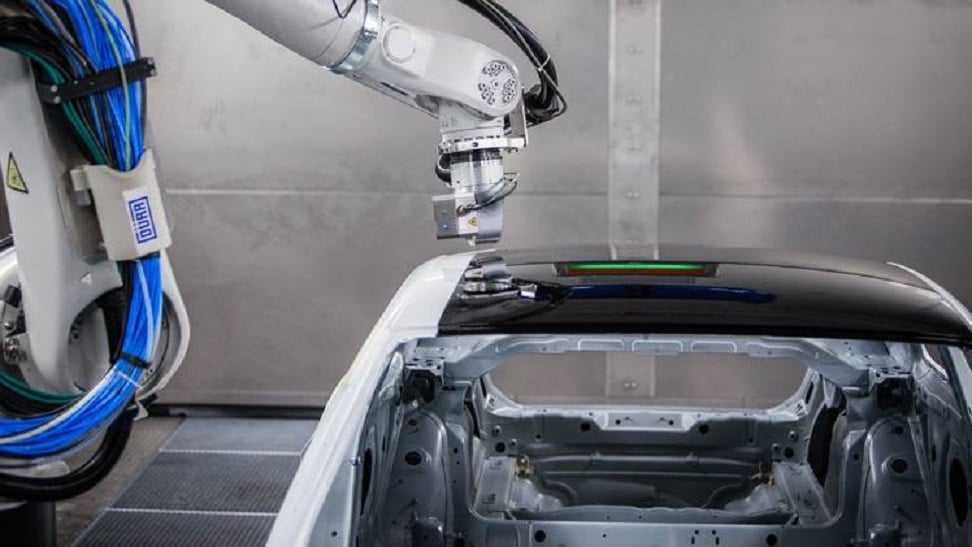
- Also suitable for electric car production
The more customized, the better – this motto governs more and more purchasing decisions. When it comes to the color of cars, the trend toward customization is also on the rise. Buyers of small cars, in particular, are increasingly ordering contrasting and accent colors, for example for the roof, to stand out from the crowd.
For the automotive industry, two-tone painting means considerably more cost and effort. Not only does it require more time and energy, it also creates a lot of wastage. Thanks to a pioneering innovation offered by Dürr, this is now changing. With its EcoPaintJet system, the world market leader in automotive painting technology presents an automated application solution that ensures an unprecedented level of precision in applying sharp paint lines.
The EcoPaintJet also offers important benefits in the painting of electric cars. Dürr introduces the solution at the 11th Open House, which will take place from May 13 to 17, 2019 at the company's headquarters in Bietigheim-Bissingen.
Dr. Jochen Weyrauch, CEO of Dürr Systems AG, says: “The EcoPaintJet is a quantum leap in the journey toward the efficient, two-tone painting of cars. It is the first system to efficiently combine customized product design with automated production.”
When only one type of paint is applied, the efficiency of modern automotive paint shops is unrivaled. Thanks to their highly automated processes, large plants paint 300,000 car bodies per year while maintaining a consistently high level of quality.
However, adding a contrasting or accent color, for example on the roof or as a design strip, means a considerable amount of extra work: Once the entire car body has been painted in the basic color, which has then dried and cooled, masking tape must be applied by hand – except for the areas due to be painted in a different color. Then the car body goes back to the painting line, where the second color is applied.
After more cooling and drying, the tape must be removed, once again by hand. This is not only associated with high labor costs, but the energy consumption for the curing of paint increases by at least 25 % compared to single-color painting. In addition, 6 to 15 square meters of masking tape must be disposed of per car body. Moreover, the painting line is blocked by the second paint application, which wastes valuable time.
No masking tape required
Dürr’s new process, known as EcoPaintJet, is much more efficient, as it dispenses altogether with the need for masking the car body. This is thanks to a totally new applicator. Fixed to a robot arm, it moves over the target area and applies paint with razor sharp lines. The paint lands exactly on the intended areas and nowhere else – not even the tiniest amounts.
As a result, the rest of the car body no longer has to be masked. It only takes a cycle time of 120 seconds to apply a contrasting color to a car body roof. By comparison: when using masking tape, the time required to put on and remove the masking tape alone is about 50 minutes.
Electric cars seem flatter
EcoPaintJet helps electric car manufacturers to fulfill an important customer requirement. Some e-cars are built slightly higher than conventional models, since the battery is installed in the floor assembly, under the passenger compartment. Many buyers, however, would like their cars to look low-slung and sporty.
To get this effect, a dark contrasting color is used to paint a strip between the roof and side wall as well as on the rocker panel, which makes the car look flatter. The EcoPaintJet is perfectly suited to this purpose, as it applies the strip precisely without compromising the existing finish.
No more overspray
The EcoPaintJet achieves its high level of precision because the applicator does not generate any overspray at all. Overspray refers to fine droplets of paint, which are produced by other atomizers, and land outside the target area. The EcoPaintJet has an intricately machined nozzle plate, measuring only a few square centimeters, which prevents the formation of overspray.
The nozzle plate, which forms the underside of the rectangular applicator, has around 50 hardly visible holes with a diameter of approx. one tenth of a millimeter. They are used to apply paint to the car body surface in parallel jets from a distance of 30 millimeters.
The applicator is the centerpiece of the perfectly designed EcoPaintJet system. This also includes the EcoRPL 133i painting robot, which moves the applicator without any vibration. A measuring system, equipped with sensors, provides maximum precision. It takes a 3D measurement of the area to be painted and sends the data to the control software.
This continuously calculates along which path the applicator must be moved over the surface to achieve an optimum paint finish – this is called automatic path generation. It also determines how the applicator must turn plus the speed required to apply exactly the right amount of paint.
According to Dr. Lars Friedrich, responsible for Application Technology on the Dürr Systems AG Board of Management: “This high-tech process enables the automotive industry to fulfill customers’ specific requirements faster while ensuring top quality. There is great interest in the market, as we are offering real added value with this new technology.”
The EcoPaintJet is currently being tested at several carmakers’ sites. In the meantime, Dürr is already working on a further development of the technology, which can also paint more complex geometries. This enhanced version, known as EcoPaintJet Pro, enables each hole in the nozzle plate to be opened and closed individually.
This offers even more possibilities for product customization. In the future, the automatic application of lettering and logos should also be possible – similar to a digital printer.
www.durr.com