www.magazine-industry-usa.com
02
'11
Written on Modified on
Bebco EPS 6000 and 5000 Q series
Preventing Dust Explosions Using the Purge+Pressurization System
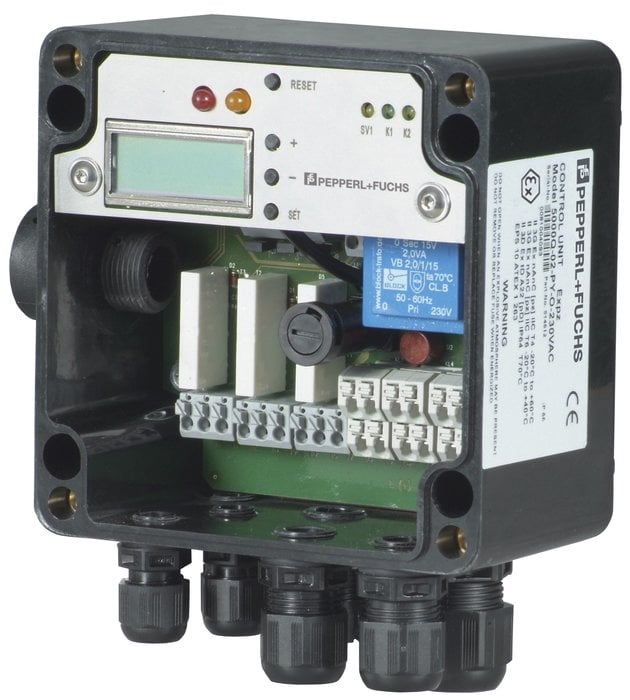
On February 7, 2008 an explosion occurred at the Imperial Sugar Company refinery in Portwentworth, Georgia, USA. The explosion left 13 people dead and 42 people injured with most of the plant destroyed. The investigation showed that there was a small explosion within the plant, which was not serious, but the result of the shock and the small fire that preceded it, caused the sugar dust to be suspended in the air, which caught on fire and followed the cloud of dust throughout the plant. Five years earlier in North Carolina, USA, a plant that produced rubber stoppers for intravenous bags and syringes and plastic pill casings for the pharmaceutical industry was destroyed because the plastic dust from the process exploded. It should be noted that the plastic that ignited was not listed in the MSDS sheets as an explosive material because it was evaluated in its normal form, as a pill casing. Take that pill casing and grind it up into a powder, and it becomes explosive.
The Imperial Sugar Company disaster and others like it caught the attention of several politicians and the Chemical Safety Board’s investigation on worker safety. The result was several congressional hearings that sited OSHA for not enforcing regulations for workers protection. As a result, OSHA has now identified at least 30,000 plants in the USA that are at risk for a combustible dust explosion. Furthermore, it is estimated that around 2,200 dust explosions happen throughout Europe every year.
As the processing industry becomes aware of this potentially devastating problem, Pepperl+Fuchs’ purge and pressurization system can easily and properly protect workers, plants, and the surrounding environments.
When it comes to purging/pressurization systems, it’s important to know that the requirements for dust atmospheres are different than those for gas atmospheres
1. Purging is not used for dust areas. If dust has accumulated inside the enclosure, it cannot exit the enclosure via the vent because the vent requires a spark-arresting screen. The enclosure must be cleaned out by hand, sealed, then pressurized to keep more dust from entering the enclosure.
2.The purge system being used must be certified for dust. This requirement is recognized in Europe and Asia where a distinction is made between zones 0, 1 and 2 for gases and zones 20, 21, 22 for dusts. However, it is sometimes overlooked in North America because it is perceived that a Type X or Type Z enclosure is certified for both gas and dust atmospheres. It is always important to check the certification of the application and equipment going into an area.
Two purge systems from Pepperl+Fuchs’ Bebco EPS line of purge and pressurization systems are certified for dust installation: the full-featured 6000 series and the compact, economical 5000 Q series:
The 6000 series is rated for both gas and dust atmospheres and has the certifications for Class I/II / Division 1, ATEX and IECEx for Zone 1/21. The new certified dust proof enclosure for the 6000 series provides a separate stainless steel enclosure to house the user interface, I.S. termination board, and optional temperature modules. The IP66 enclosure is an accessory for use with the 6000 series component kit and can be mounted and used in the dust area. The component kit allows the 6000 series purge to be custom installed inside an equipment enclosure so that it is not mounted externally. This addition to the component kit provides a simple way to separate the purged enclosure and the user interface. The remote user interface can be mounted in a user accessible location while still located in the hazardous environment.
The 5000Q series is a uniquely compact, low cost, and efficient purge and pressurization system rated for both gas and dust atmospheres that allows users to save money and space with a solution specifically engineered for ATEX Zone 2/22 installations. It is one of the simplest, most flexible, and easiest to use purge and pressurization systems to date. User-selectable programming makes it easy to select the specific program to satisfy a variety of application needs, and an integral pressure sensor facilitates automatic purging and pressurization through the digital solenoid valve.
The Imperial Sugar Company disaster and others like it caught the attention of several politicians and the Chemical Safety Board’s investigation on worker safety. The result was several congressional hearings that sited OSHA for not enforcing regulations for workers protection. As a result, OSHA has now identified at least 30,000 plants in the USA that are at risk for a combustible dust explosion. Furthermore, it is estimated that around 2,200 dust explosions happen throughout Europe every year.
As the processing industry becomes aware of this potentially devastating problem, Pepperl+Fuchs’ purge and pressurization system can easily and properly protect workers, plants, and the surrounding environments.
When it comes to purging/pressurization systems, it’s important to know that the requirements for dust atmospheres are different than those for gas atmospheres
1. Purging is not used for dust areas. If dust has accumulated inside the enclosure, it cannot exit the enclosure via the vent because the vent requires a spark-arresting screen. The enclosure must be cleaned out by hand, sealed, then pressurized to keep more dust from entering the enclosure.
2.The purge system being used must be certified for dust. This requirement is recognized in Europe and Asia where a distinction is made between zones 0, 1 and 2 for gases and zones 20, 21, 22 for dusts. However, it is sometimes overlooked in North America because it is perceived that a Type X or Type Z enclosure is certified for both gas and dust atmospheres. It is always important to check the certification of the application and equipment going into an area.
Two purge systems from Pepperl+Fuchs’ Bebco EPS line of purge and pressurization systems are certified for dust installation: the full-featured 6000 series and the compact, economical 5000 Q series:
The 6000 series is rated for both gas and dust atmospheres and has the certifications for Class I/II / Division 1, ATEX and IECEx for Zone 1/21. The new certified dust proof enclosure for the 6000 series provides a separate stainless steel enclosure to house the user interface, I.S. termination board, and optional temperature modules. The IP66 enclosure is an accessory for use with the 6000 series component kit and can be mounted and used in the dust area. The component kit allows the 6000 series purge to be custom installed inside an equipment enclosure so that it is not mounted externally. This addition to the component kit provides a simple way to separate the purged enclosure and the user interface. The remote user interface can be mounted in a user accessible location while still located in the hazardous environment.
The 5000Q series is a uniquely compact, low cost, and efficient purge and pressurization system rated for both gas and dust atmospheres that allows users to save money and space with a solution specifically engineered for ATEX Zone 2/22 installations. It is one of the simplest, most flexible, and easiest to use purge and pressurization systems to date. User-selectable programming makes it easy to select the specific program to satisfy a variety of application needs, and an integral pressure sensor facilitates automatic purging and pressurization through the digital solenoid valve.