www.magazine-industry-usa.com
24
'11
Written on Modified on
Modernisation of the Loden-Frey fashion store in Munich
The refurbishment of the HVAC system of the Loden-Frey fashion store in Munich was particularly challenging as under no circumstances could the refurbishing work disrupt normal business operations or disturb the store’s customers. The project was made all the more difficult by the restricted clearance space above the suspended ceilings and the limited space available for a new plant room.
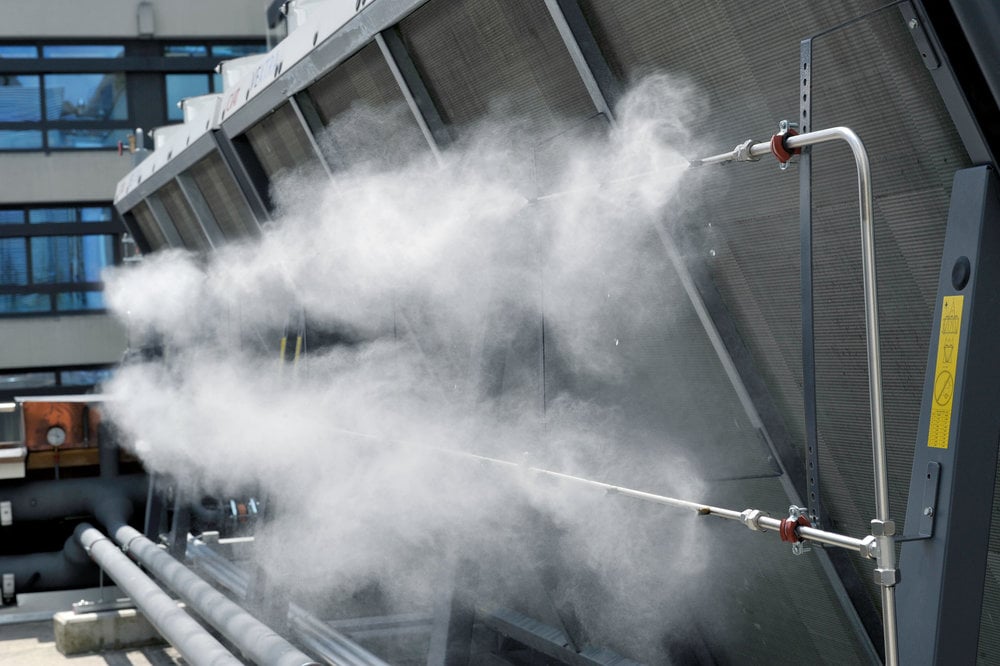
Technically speaking, a project involving a cooling system with 840 kW of new installed capacity, around 60 recirculating ceiling coolers, an air-water dry cooler and free cooling may not seem particularly spectacular. However, when the spatial constraints are considered, which implied unusually stringent demands, the project is indeed impressive.
The Loden-Frey fashion store in Munich consists of a complex of three buildings which are semi-independent in terms of building services but provide continuous usable floor space over several storeys. The sales areas, distributed over five floors, have a total floor space of 7,400 square metres. Originally, each building had its own designated use. One was designed for sales, another as an office building, and the third as a commercial and/or administration building. This naturally led to different storey heights, different ceiling heights and different building service system configurations.
Little space for an equipment room
The sales areas required a full-spectrum air conditioning system that could provide all four air handling options. Garment merchandising imposes severe constraints on air conditioning; the room must be constantly maintained at 22 °C with a relative humidity of 45 per cent all year round.
In addition, the new air conditioning units had to supply cooling to a portion of the existing ventilation systems. The plans called for the installation of a free cooling system to handle the transition periods and the winter season. This required a water-cooled water chiller and a suitable of dry cooler heat exchanger combination.
Furthermore, Loden-Frey could not free up any shop space for the new building services equipment room envisaged in the project plan. According to Franz Mihali, Technical Manager at Loden-Frey, this would have been far too costly. “Due to its exclusive location in the historic district, every square centimetre is valuable. Converting shop space into an equipment room would have represented an estimated cost of 100,000 euros extrapolated over a period of 20 years, based on the usual lease rates in this area.”
The only option available was a space with an area of 30 square metres, which was located under a ramp with a slope of approximately 20 degrees and was therefore originally too low. Part of the floor had to be lowered in order to provide sufficient height for the chillers. Owing to the presence of foundations beneath the floor, the area concerned was lowered in three steps, ranging from around 60 centimetres to 90 centimetres.
Based on their experience of previous projects and in consultation with Loden-Frey, the planners at IBF Ingenieurgesellschaft and the employees of Stingl, who were entrusted with carrying out all of the installation work, chose CIAT Kälte- und Klimatechnik for this joint project. They wanted to have just one contact person instead of many, and they needed a manufacturer that could supply a wide range of industrially standardised but nevertheless versatile components. The manufacturer also needed to have regional representation with knowledgeable contact persons. The French manufacturer CIAT has an extensive network of branches throughout Germany, one of which is located close to Munich.
A quick solution
The reduced clearance above the suspended ceilings imposed the use of units with low installed height, and in addition, ceiling cooling units with different capacities and adjustable air outlets were needed. Low-noise ceiling cassettes from the Melody range (type WA 63) with a LON connection were installed for this purpose. Thanks to their autonomous operating principle, these air conditioning units were able to operate for six months without being integrated into the building control system.
Organisational tour de force
It was imperative that all alterations in the shop areas be carried out inconspicuously; it was also important to ensure that Loden-Frey’s customers would not be inconvenienced even the slightest by noise or dust, or have the feeling they were on a construction site. The building areas to be refurbished were divided into small units using a grid system. In turn, each unit was partitioned off from the sales areas by quickly repositionable studded walls. All noisy activities had to be carried out at night, during shift work or at the weekend. Installation activities which generated little noise could be carried out during the day. When the work location shifted to a new grid cell, everything had to be restored to tip-top condition by 10 a.m., including the sales areas.
UTA Fan Coil Units designed for installation in the dead space between the rough and suspended ceilings were used wherever enough space was available. They can handle air volumes from 200 to 1,600 cubic metres per hour and have cooling capacities up to 11 kW. In locations where the space above the suspended ceiling was not deep enough for UTA units, Melody ceiling cassettes were used. Their air capacity ranges from 290 to 1,390 cubic metres per hour, with a cooling capacity of 1,530 to 10,800 watts.
Extremely compact equipment
The total installed cooling capacity of the fashion store is now just under two megawatts, including 840 kilowatts of new capacity. To provide this, three Dynaciat water-water water chillers were installed in the new building services equipment room. Two of them have a capacity of 330 kW, while the third has a capacity of 180 kW. Each of these chillers is equipped with a scroll compressor, and they can be cut in or out in stages allowing the system to respond to load variations.
A free cooling system was also installed. This was integrated into the cooling system for continuously variable operation to provide the capacity necessary for the air conditioning of rooms during transition periods when outdoor temperatures are below 15 °C. The temperature difference is significant enough to allow the temperatures in the sales areas to be maintained at 22 to 23 °C. The basic prerequisite for integrating free cooling was the presence of the water-cooled water chiller. An additional plate heat exchanger is driven via the cooling circuit of the chiller and the dry cooler. The plate heat exchanger has a capacity of 165 kW and is integrated into the circuit of the RLT system.
A dry cooler in the courtyard
The installation of the air-water dry cooler was also an exceptional assignment with an input power rating of 1,000 kW, of which 840 kW cooling capacity and 160 kW dissipated heat. However, a dry cooler with a capacity of approximately 1,500 kW would be required under extreme conditions, such as in the summer with temperatures around 35 °C and a relative humidity of 50 per cent. There was not enough space for a dry cooler of this size, so the extra capacity needed to handle the climatic conditions was provided by an adiabatic cooling unit.
The only location available in which to install this cooler was the courtyard. Once in place and reassembled, the V-shaped cooler comprised a total of fourteen fans in a horizontal arrangement. Operating in suction mode, they generate an air flow of 146,000 cubic metres per hour. To minimise noise emissions in the sensitive courtyard environment, the fans run at a maximum of 80 per cent of their rated capacity. At this reduced speed, the noise pressure level of the dry cooler can be limited to a maximum of 48 dB(A).
The main concern as regards the additional adiabatic cooling was the air quality in the courtyard. Part of the courtyard is used by the employees of the fashion store, and the adjoining buildings have windows facing out onto the courtyard. For this reason, a key concern in the design of the installation was to ensure that the water was sprayed in such a fine mist that every droplet evaporated completely. The system is fed by a pump that boosts the water pressure in the supply line for the adiabatic cooling unit to 80 bar. Extremely fine nozzles spray the water against small impact surfaces positioned in front of the nozzles. The nozzles face away from the suction side of the cooler. Water lands on the fins of the cooler only under unfavourable wind conditions, and even then, no deposits form on the heat exchangers. All water used at Loden-Frey is fully demineralised due to the quality of the local water. The water for the adiabatic cooling unit is additionally filtered, and any micro-organisms that may still be present are killed by UV light.
The adiabatic cooling unit has a nominal cooling capacity of approximately 400 kW. It is designed to cool the air impinging on the heat exchanger by approximately seven degrees Kelvin at an outdoor temperature of 35 °C. This results from the fact that the water extracts the heat needed for its evaporation from the air ahead of the dry cooler. Thanks to its clever design and construction, the unit used in the Loden-Frey project comes close to reaching the dew-point temperature and saturating the air to nearly 100 per cent relative humidity. The system is configured to prevent water condensation and avoid the formation of standing water. All components of the evaporative cooling unit were supplied by the dry cooler manufacturer as standard accessories.
Complex heat load determination
Franz Mihali, Building Services Manager of the fashion store: “Another aspect that is relevant to air conditioning and important for us is that we must offer our customers a high level of comfort in terms of temperature. This is because garments are always sold ahead of the season: fall fashions are sold in the summer, and the winter collection is sold in the fall. For this reason, we need a constant temperature of 22 °C in all sales areas, all year round.” Lighting is the predominant concern in the upscale presentation of the goods in the Loden-Frey shop. As a result, nearly a megawatt of electrical power is consumed by the lighting systems at Loden-Frey. This additional heat input requires constant cooling capacity during most of the year.
Close cooperation is essential
Johann Schranner, Sales Engineer, summarised the situation: “This complex refurbishment project with its many unknowns clearly shows that close cooperation, from a very early stage onward, must be given top priority. For us as a manufacturer, this project is a good example of how even demanding object-specific requirements can be fulfilled using industrially produced, standardised products.”
He also sees an obligation to provide sustained customer support. It would not be right to burden the customer with the responsibility for sophisticated technology. For this reason, customer service must be given high priority. “In the case of Loden-Frey, our service staff effectively take responsibility for the air conditioning system. They have unrestricted access to all internal company documents, and they know where to look for and find solutions to problems. Their expertise is also indispensable for remote troubleshooting by telephone. This helps our customers minimise unnecessary expenses, since most of the reported problems usually do not have anything to do with the cooling equipment.
Key data of the refurbishment project
Building area: 7,400 square metres
Construction period: October 2007 to mid-2011
Planning: IBF Ingenieurgesellschaft mbh, Munich
Installation: Stingl GmbH, Munich
Specific refurbishment requirements: Air conditioning: constant 22 °C room temperature with 45% relative humidity
A/C technology
-3 Dynaciat water chillers; total capacity 840 kW
-60 ceiling-mounted recirculating cooling units: Melody cassette fan coil units with capacities of 200 to 1,600 cubic metres per hour; UTA ductable fan coil units with capacities of 290 to 1,530 cubic metres per hour
-1 heat exchanger, CIAT PWA 1811, rated capacity 165 kW, for free cooling
-Vextra dry cooler, V-shape extraction unit with 14 fans arranged horizontally, air flow capacity 146,000 cubic metres per hour, cooling capacity 1,000 kW
About Loden-Frey
The Loden-Frey fashion store is situated at Maffeistraße 7 in Munich. The history of the company extends back to 1842, when cloth-maker Johann Georg Frey invented the water-repellent Loden fabric. Naturally, traditional clothing made from this material still forms part of the product line of the fashion store, but the descendents of the Loden cloth inventor have successively enlarged the product portfolio of the erstwhile specialist. With its focus on a sophisticated clientele, as a pre-eminent fashion store, Loden-Frey today offers only exclusive, selected garments from the word’s most renowned designers and manufacturers.
Photo captions:
DSC0468a: Loden-Frey is one of the leading Munich addresses for upscale clothing.
DSC0477a: Space is tight in the new building services equipment room. All of the piping had to be fitted before the water chiller could be installed.
DSC1249a: Sorting out a few project details (from left to right): Martin Fesl, IBF Ingenieurgesellschaft; Franz Mihali, Loden-Frey Building Services Manager; Helmut Kühner, CIAT Service Technician; Johann Schranner, CIAT Sales Engineer; Tobias Erl, Stingl Project Manager.
DSC0530a: The adiabatic cooling unit, installed ahead of the Vextra dry cooler, in action.
DSC1382a: The enormous heat input for the solarium is obvious at a glance.
DSC1404a: The unobtrusively integrated Melody ceiling cassettes have adjustable air outlets.
All photos: CIAT Kälte- und Klimatechnik GmbH
The Loden-Frey fashion store in Munich consists of a complex of three buildings which are semi-independent in terms of building services but provide continuous usable floor space over several storeys. The sales areas, distributed over five floors, have a total floor space of 7,400 square metres. Originally, each building had its own designated use. One was designed for sales, another as an office building, and the third as a commercial and/or administration building. This naturally led to different storey heights, different ceiling heights and different building service system configurations.
Little space for an equipment room
The sales areas required a full-spectrum air conditioning system that could provide all four air handling options. Garment merchandising imposes severe constraints on air conditioning; the room must be constantly maintained at 22 °C with a relative humidity of 45 per cent all year round.
In addition, the new air conditioning units had to supply cooling to a portion of the existing ventilation systems. The plans called for the installation of a free cooling system to handle the transition periods and the winter season. This required a water-cooled water chiller and a suitable of dry cooler heat exchanger combination.
Furthermore, Loden-Frey could not free up any shop space for the new building services equipment room envisaged in the project plan. According to Franz Mihali, Technical Manager at Loden-Frey, this would have been far too costly. “Due to its exclusive location in the historic district, every square centimetre is valuable. Converting shop space into an equipment room would have represented an estimated cost of 100,000 euros extrapolated over a period of 20 years, based on the usual lease rates in this area.”
The only option available was a space with an area of 30 square metres, which was located under a ramp with a slope of approximately 20 degrees and was therefore originally too low. Part of the floor had to be lowered in order to provide sufficient height for the chillers. Owing to the presence of foundations beneath the floor, the area concerned was lowered in three steps, ranging from around 60 centimetres to 90 centimetres.
Based on their experience of previous projects and in consultation with Loden-Frey, the planners at IBF Ingenieurgesellschaft and the employees of Stingl, who were entrusted with carrying out all of the installation work, chose CIAT Kälte- und Klimatechnik for this joint project. They wanted to have just one contact person instead of many, and they needed a manufacturer that could supply a wide range of industrially standardised but nevertheless versatile components. The manufacturer also needed to have regional representation with knowledgeable contact persons. The French manufacturer CIAT has an extensive network of branches throughout Germany, one of which is located close to Munich.
A quick solution
The reduced clearance above the suspended ceilings imposed the use of units with low installed height, and in addition, ceiling cooling units with different capacities and adjustable air outlets were needed. Low-noise ceiling cassettes from the Melody range (type WA 63) with a LON connection were installed for this purpose. Thanks to their autonomous operating principle, these air conditioning units were able to operate for six months without being integrated into the building control system.
Organisational tour de force
It was imperative that all alterations in the shop areas be carried out inconspicuously; it was also important to ensure that Loden-Frey’s customers would not be inconvenienced even the slightest by noise or dust, or have the feeling they were on a construction site. The building areas to be refurbished were divided into small units using a grid system. In turn, each unit was partitioned off from the sales areas by quickly repositionable studded walls. All noisy activities had to be carried out at night, during shift work or at the weekend. Installation activities which generated little noise could be carried out during the day. When the work location shifted to a new grid cell, everything had to be restored to tip-top condition by 10 a.m., including the sales areas.
UTA Fan Coil Units designed for installation in the dead space between the rough and suspended ceilings were used wherever enough space was available. They can handle air volumes from 200 to 1,600 cubic metres per hour and have cooling capacities up to 11 kW. In locations where the space above the suspended ceiling was not deep enough for UTA units, Melody ceiling cassettes were used. Their air capacity ranges from 290 to 1,390 cubic metres per hour, with a cooling capacity of 1,530 to 10,800 watts.
Extremely compact equipment
The total installed cooling capacity of the fashion store is now just under two megawatts, including 840 kilowatts of new capacity. To provide this, three Dynaciat water-water water chillers were installed in the new building services equipment room. Two of them have a capacity of 330 kW, while the third has a capacity of 180 kW. Each of these chillers is equipped with a scroll compressor, and they can be cut in or out in stages allowing the system to respond to load variations.
A free cooling system was also installed. This was integrated into the cooling system for continuously variable operation to provide the capacity necessary for the air conditioning of rooms during transition periods when outdoor temperatures are below 15 °C. The temperature difference is significant enough to allow the temperatures in the sales areas to be maintained at 22 to 23 °C. The basic prerequisite for integrating free cooling was the presence of the water-cooled water chiller. An additional plate heat exchanger is driven via the cooling circuit of the chiller and the dry cooler. The plate heat exchanger has a capacity of 165 kW and is integrated into the circuit of the RLT system.
A dry cooler in the courtyard
The installation of the air-water dry cooler was also an exceptional assignment with an input power rating of 1,000 kW, of which 840 kW cooling capacity and 160 kW dissipated heat. However, a dry cooler with a capacity of approximately 1,500 kW would be required under extreme conditions, such as in the summer with temperatures around 35 °C and a relative humidity of 50 per cent. There was not enough space for a dry cooler of this size, so the extra capacity needed to handle the climatic conditions was provided by an adiabatic cooling unit.
The only location available in which to install this cooler was the courtyard. Once in place and reassembled, the V-shaped cooler comprised a total of fourteen fans in a horizontal arrangement. Operating in suction mode, they generate an air flow of 146,000 cubic metres per hour. To minimise noise emissions in the sensitive courtyard environment, the fans run at a maximum of 80 per cent of their rated capacity. At this reduced speed, the noise pressure level of the dry cooler can be limited to a maximum of 48 dB(A).
The main concern as regards the additional adiabatic cooling was the air quality in the courtyard. Part of the courtyard is used by the employees of the fashion store, and the adjoining buildings have windows facing out onto the courtyard. For this reason, a key concern in the design of the installation was to ensure that the water was sprayed in such a fine mist that every droplet evaporated completely. The system is fed by a pump that boosts the water pressure in the supply line for the adiabatic cooling unit to 80 bar. Extremely fine nozzles spray the water against small impact surfaces positioned in front of the nozzles. The nozzles face away from the suction side of the cooler. Water lands on the fins of the cooler only under unfavourable wind conditions, and even then, no deposits form on the heat exchangers. All water used at Loden-Frey is fully demineralised due to the quality of the local water. The water for the adiabatic cooling unit is additionally filtered, and any micro-organisms that may still be present are killed by UV light.
The adiabatic cooling unit has a nominal cooling capacity of approximately 400 kW. It is designed to cool the air impinging on the heat exchanger by approximately seven degrees Kelvin at an outdoor temperature of 35 °C. This results from the fact that the water extracts the heat needed for its evaporation from the air ahead of the dry cooler. Thanks to its clever design and construction, the unit used in the Loden-Frey project comes close to reaching the dew-point temperature and saturating the air to nearly 100 per cent relative humidity. The system is configured to prevent water condensation and avoid the formation of standing water. All components of the evaporative cooling unit were supplied by the dry cooler manufacturer as standard accessories.
Complex heat load determination
Franz Mihali, Building Services Manager of the fashion store: “Another aspect that is relevant to air conditioning and important for us is that we must offer our customers a high level of comfort in terms of temperature. This is because garments are always sold ahead of the season: fall fashions are sold in the summer, and the winter collection is sold in the fall. For this reason, we need a constant temperature of 22 °C in all sales areas, all year round.” Lighting is the predominant concern in the upscale presentation of the goods in the Loden-Frey shop. As a result, nearly a megawatt of electrical power is consumed by the lighting systems at Loden-Frey. This additional heat input requires constant cooling capacity during most of the year.
Close cooperation is essential
Johann Schranner, Sales Engineer, summarised the situation: “This complex refurbishment project with its many unknowns clearly shows that close cooperation, from a very early stage onward, must be given top priority. For us as a manufacturer, this project is a good example of how even demanding object-specific requirements can be fulfilled using industrially produced, standardised products.”
He also sees an obligation to provide sustained customer support. It would not be right to burden the customer with the responsibility for sophisticated technology. For this reason, customer service must be given high priority. “In the case of Loden-Frey, our service staff effectively take responsibility for the air conditioning system. They have unrestricted access to all internal company documents, and they know where to look for and find solutions to problems. Their expertise is also indispensable for remote troubleshooting by telephone. This helps our customers minimise unnecessary expenses, since most of the reported problems usually do not have anything to do with the cooling equipment.
Key data of the refurbishment project
Building area: 7,400 square metres
Construction period: October 2007 to mid-2011
Planning: IBF Ingenieurgesellschaft mbh, Munich
Installation: Stingl GmbH, Munich
Specific refurbishment requirements: Air conditioning: constant 22 °C room temperature with 45% relative humidity
A/C technology
-3 Dynaciat water chillers; total capacity 840 kW
-60 ceiling-mounted recirculating cooling units: Melody cassette fan coil units with capacities of 200 to 1,600 cubic metres per hour; UTA ductable fan coil units with capacities of 290 to 1,530 cubic metres per hour
-1 heat exchanger, CIAT PWA 1811, rated capacity 165 kW, for free cooling
-Vextra dry cooler, V-shape extraction unit with 14 fans arranged horizontally, air flow capacity 146,000 cubic metres per hour, cooling capacity 1,000 kW
About Loden-Frey
The Loden-Frey fashion store is situated at Maffeistraße 7 in Munich. The history of the company extends back to 1842, when cloth-maker Johann Georg Frey invented the water-repellent Loden fabric. Naturally, traditional clothing made from this material still forms part of the product line of the fashion store, but the descendents of the Loden cloth inventor have successively enlarged the product portfolio of the erstwhile specialist. With its focus on a sophisticated clientele, as a pre-eminent fashion store, Loden-Frey today offers only exclusive, selected garments from the word’s most renowned designers and manufacturers.
Photo captions:
DSC0468a: Loden-Frey is one of the leading Munich addresses for upscale clothing.
DSC0477a: Space is tight in the new building services equipment room. All of the piping had to be fitted before the water chiller could be installed.
DSC1249a: Sorting out a few project details (from left to right): Martin Fesl, IBF Ingenieurgesellschaft; Franz Mihali, Loden-Frey Building Services Manager; Helmut Kühner, CIAT Service Technician; Johann Schranner, CIAT Sales Engineer; Tobias Erl, Stingl Project Manager.
DSC0530a: The adiabatic cooling unit, installed ahead of the Vextra dry cooler, in action.
DSC1382a: The enormous heat input for the solarium is obvious at a glance.
DSC1404a: The unobtrusively integrated Melody ceiling cassettes have adjustable air outlets.
All photos: CIAT Kälte- und Klimatechnik GmbH