www.magazine-industry-usa.com
25
'10
Written on Modified on
Single Chip CANopen Interface
Embedded CANopen interface reduces development efforts up to 70%.
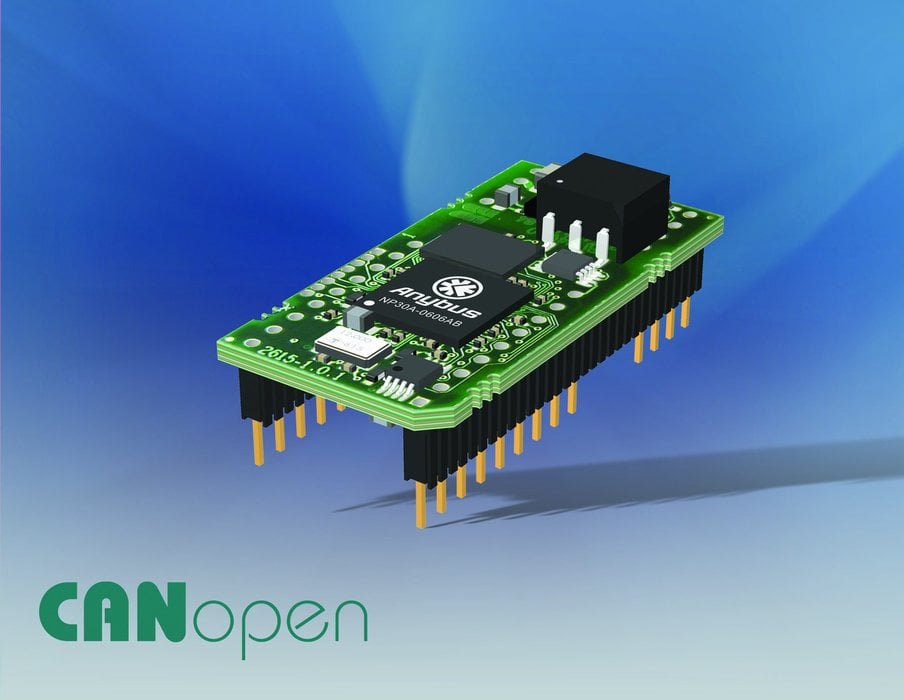
HMS Industrial Networks has extended its Anybus-IC family with the addition of the Anybus-IC for CANopen. The module is a tiny but powerful embedded single-chip CANopen interface, which is certified by the CAN user organization for conformance to the CANopen standard. The new component extends HMS´ Anybus-IC family which already includes interchangeable solutions for Profibus, Profinet, DeviceNet, EtherNet/IP and Modbus-TCP.
In a single housing of only 8cm2 in size, the Anybus-IC contains the HMS NP30 microprocessor with its integrated CAN controller and a full featured CANopen slave software stack. The IC reduces the development efforts needed to design a CANopen interface by up to 70%. Additionally, space and power supply requirements are minimized so that even small automation devices such as barcode readers or motor starters can be economically equipped with a CANopen interface.
The Anybus-IC has a 32-pin dual in line housing and requires only a single 5 Volt / 150 mA power supply. It functions as a standard CANopen slave and supports Version 4 of the DS 301 profile. Up to 144 bytes of input data and 144 bytes of output data are permitted. The Anybus-IC contains all hardware and software necessary for any automation device to communicate over a CANopen network, only the connector has to be added.
When used in intelligent devices that have their own micro-controller, the Anybus-IC is connected via a fast serial TTL interface. The IC handles the entire CANopen protocol and offloads the microprocessor from all time-critical communication tasks. For use in simple automation devices such as valve terminals, that -have no mircoprocessor, the Anybus-IC has a shift register interface and can control up to 128 direct inputs and outputs.
All members of the Anybus-IC family are interchangeable and offer device manufacturers a simple and efficient way to connect small and medium automation devices to all major fieldbus and industrial Ethernet networks with just one development.
In a single housing of only 8cm2 in size, the Anybus-IC contains the HMS NP30 microprocessor with its integrated CAN controller and a full featured CANopen slave software stack. The IC reduces the development efforts needed to design a CANopen interface by up to 70%. Additionally, space and power supply requirements are minimized so that even small automation devices such as barcode readers or motor starters can be economically equipped with a CANopen interface.
The Anybus-IC has a 32-pin dual in line housing and requires only a single 5 Volt / 150 mA power supply. It functions as a standard CANopen slave and supports Version 4 of the DS 301 profile. Up to 144 bytes of input data and 144 bytes of output data are permitted. The Anybus-IC contains all hardware and software necessary for any automation device to communicate over a CANopen network, only the connector has to be added.
When used in intelligent devices that have their own micro-controller, the Anybus-IC is connected via a fast serial TTL interface. The IC handles the entire CANopen protocol and offloads the microprocessor from all time-critical communication tasks. For use in simple automation devices such as valve terminals, that -have no mircoprocessor, the Anybus-IC has a shift register interface and can control up to 128 direct inputs and outputs.
All members of the Anybus-IC family are interchangeable and offer device manufacturers a simple and efficient way to connect small and medium automation devices to all major fieldbus and industrial Ethernet networks with just one development.