The Future’s Bright
Mitsubishi Electric invests substantial amounts of time and resources in R&D activities to develop future technologies and products.
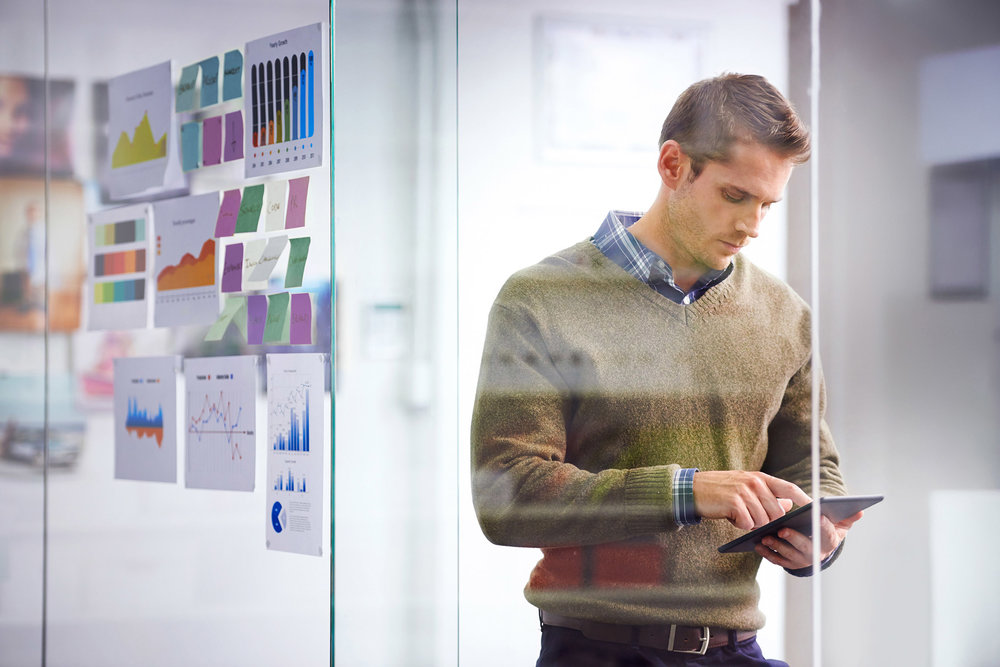
Mitsubishi Electric specialises in practical R&D, where everyone can appreciate the benefits
Some discoveries and innovations are incorporated subtly over many years, while others lead to radical new breakthroughs that disrupt existing markets. But what of today? What new technologies are available right now that can help advance the manufacturing operations of 2018? This article examines some recent developments of the R&D teams at Mitsubishi Electric, such as a high-performance database that can reduce data storage space by 98.5%, a huge benefit in a manufacturing age increasingly driven by process data collection and analysis. Another exciting development is a concept able to miniaturise the artificial intelligence (AI) algorithm to the point that individual devices can benefit from AI and local ‘deep learning’ processes. The future is bright indeed.
Data storage in the IoT
Among the overlooked challenges of the Internet of Things (IoT) is the large amount of captured data that has to be stored somewhere. Over the years industry has seen megabytes run into gigabytes, and gigabytes turn into terabytes. And it will not be long before engineers are routinely talking about petabytes, exabytes and zettabytes. One issue with this rapidly expanding data capacity is the cost for storage, back-up and keeping it available 24/7.
To imagine the scale of the challenge, consider how many sensors, data points and memory stores there are in a typical factory. A single production line can have thousands of sensors, each one generating a data reading every 100ms or less. Over a couple of years, this could add up to hundreds of terabytes of data. Multiply this figure by the number of production lines – and sites – and it is not long before a hefty monthly bill starts arriving from the cloud provider simply for storing data.
With the aim of addressing this issue, Mitsubishi Electric R&D has developed a high-performance database with the ability to reduce the required storage space by 98.5%. Significantly, because the volume is reduced, the load time for the database is also decreased by around 98%, which in turn means the search time reduces accordingly. All of these results can be achieved using a standard 2-CPU server with 4GB of main memory, an outcome that emphasises practical R&D at its best, where everyone can appreciate the benefit.
Artificial intelligence gets real
From blockbuster movies to the doom-laden predictions of sci-fi writers, AI is both scary and hugely exciting. Much of what has materialised to date has been impressive, but of little practical benefit, primarily because of two key issues. The first is the tethering of a super computer: if industry really needs that much computing power, it is hard to see how AI will be usable. The second is the realisation that AI, just like a human baby, needs to be taught or shown how to learn some basic rules around the task at hand.
To turn AI into a practical solution for today, Mitsubishi Electric R&D has been focused on both of these key issues. The result is Maisart (Mitsubishi Electric’s AI creates the State-of-the-ART in technology). Maisart has miniaturised the AI algorithm to the point where it can be deployed on a single chip embedded in other products. This capability means that individual devices can benefit from AI and local ‘deep learning’ processes, while AI located in cloud environments can be used to co-ordinate between those devices. Think of it as applying AI on a scalable base: machine to line; line to factory; factory to enterprise.
In the past, deep learning algorithms were expensive and IT-heavy. However, the new automated deep learning technology from Mitsubishi Electric is a world first and critical to future AI deployment without relying on expert knowledge. In fact, the training element of the AI is now 96.7% faster, which means this technology can be applied to faster and more demanding tasks.
In a manufacturing environment, for example, robots could be learning new tasks in minutes rather than being taught manually over many hours, simply because the number of trial operations and calculations can be reduced by 98% or more. Maisart-based FA solutions will soon become increasingly common, as will AI deployment in everyday products such as air conditioners and other increasingly intelligent appliances.
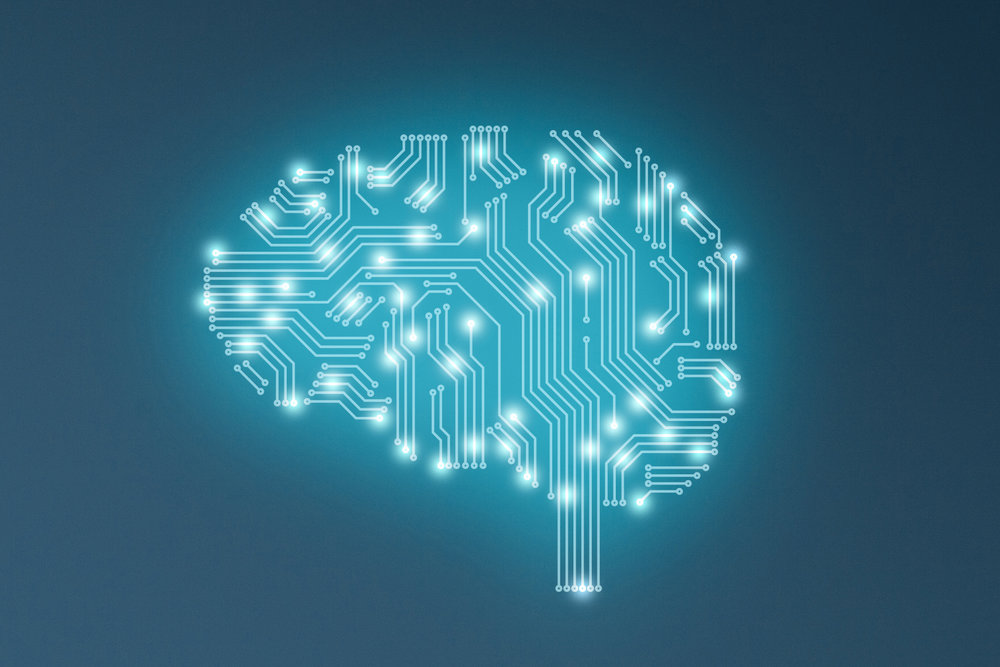
Mitsubishi Electric’s ‘Maisart’ means that individual devices can benefit from AI and local deep learning processes
Proven track record
Of course, Mitsubishi Electric has registered many notable technological breakthroughs over the years. Take interactive vision-guided robots in the postal industry, for example. The surge in global parcel traffic has been spurred in recent times by the success of online retail giants such as Amazon. Here, the desire for total automation has been a long-held goal. However, the main challenge has been devising a robot capable of picking a seemingly infinite number of different package sizes and shapes.
With this issue in mind, the Amazon Picking Challenge was born, whereby robots are tasked with picking a wide variety of small, large, soft, hard, fragile, robust, light and heavy products – and placing them in a packing carton without mis-picking or damaging the goods. Mitsubishi Electric’s MELFA 3D vision for robots proved to be an essential enabler of this process, allowing the robot to ‘see’ what it wants to pick. The system can even enable robots to quickly and reliably pick products that are dispersed randomly in a pick bin. In 2014, this particular Mitsubishi technology won a coveted R&D100 award.
This example, like many others of yesterday, today and tomorrow, means that Mitsubishi Electric R&D successes not only lead the world in terms of technology, but deliver real benefits and create new automation solutions for a brighter future. Moving forward, industry expects an enhanced human, machine and AI environment that will deliver many positive benefits for all concerned. Imagination, it would appear, is the only limitation.
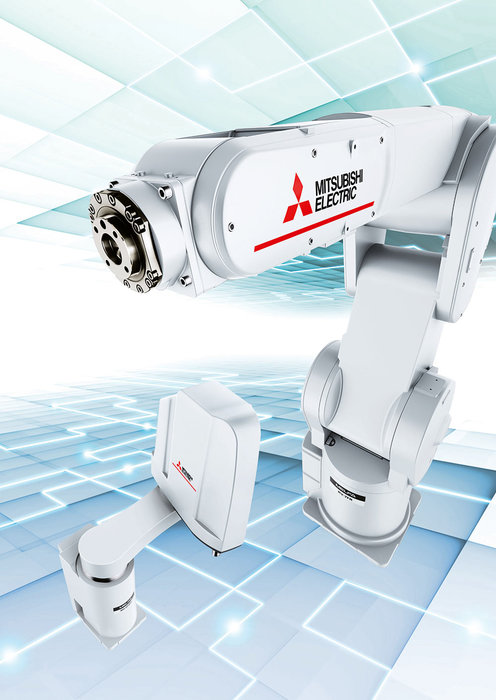
Vision-guided robots are a recent example of where Mitsubishi Electric R&D has made a significant contribution to advancing real-life industrial operations