www.magazine-industry-usa.com
12
'09
Written on Modified on
ANDANTEX equips the most innovating label manufacturing machines available on the market
ETI Converting Equipment is a company specialized in the design of machines for the manufacture of self-adhesive label equipment and printing presses. Recently, ETI Converting Equipment developed a revolutionary process for the application of a treatment on the parent material that increases the adhesive capacity of the ink, glue, or any other coating. Result: the printer can now purchase a much cheaper non-treated film and make considerable savings in label manufacture. In this leading edge process, ANDANTEX USA offers solutions marketed by MEROBEL (REDEX ANDANTEX group), a world leader in the web tension control field.
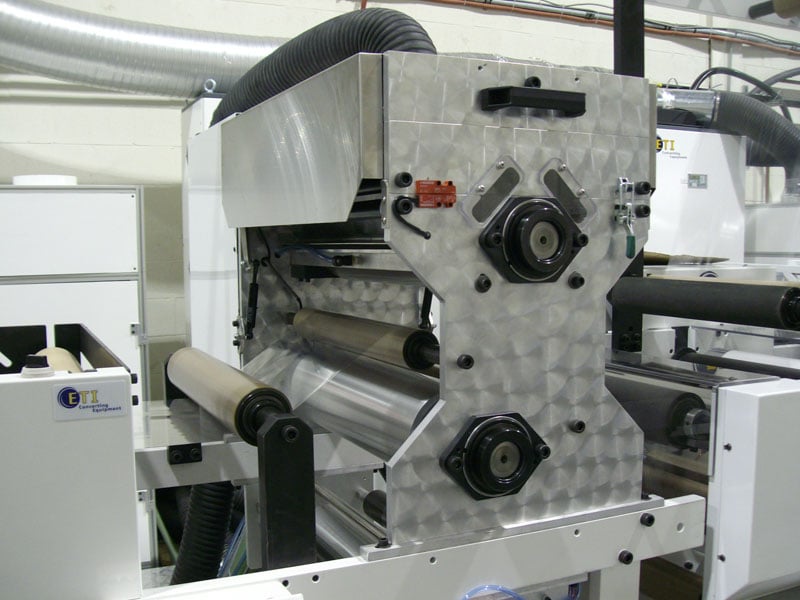
François Bayzelon, President and CEO at ETI, explains: «Our technology offers printers the possibility of entirely manufacturing their self-adhesive labels while making 30 to 70% cost savings on the raw material cost price». Savings are large scale, the investment payback is in less than one year and the outcome is a natural success. The first COHESIO system was presented at LabelExpo in 2000. Since then, more than 70 lines have been sold at a rate increasing each year with about 20 in 2008 alone.
The latest ETI substrate pretreatment system is called ETI Corona Plasma Optimum, or more commonly the ETI-CPO. This treatment is applied in an enclosure under a controlled inert gas environment. It sends a corona discharge to the surface of the film (PP, BOPP or PET), allowing the surface energy to be increased which provides for excellent wetability and superb adhesion of the glue, ink, or any other coating. The ETI-CPO system may be used with the COHESIO or upline on the rotary press printing the front before glue coating.
This frontline technology requires perfect web tension control. “Web tension control is necessary no matter what sector is involved in the Converting field. For us, it is even more critical as the films are very thin (15 to 20 µm). We use feed speeds of 120 m/minute. The web may then stretch 40 mm. Without excellent tension control, the register cannot be perfectly controlled and it is then impossible to implement our system. The chosen system becomes a strategic choice. We have analyzed all proposals available on the market and chose ANDANTEX, simply because they are the best. Technical assistance also played a deciding role. MEROBEL products are mounted on all our equipment, COHESIO or METRONOME. ANDANTEX USA also had the foresight to believe in the potential of the company since its founding.”
The MEROBEL web tension control system mainly consists of 2 complementary components: the EMP brakes and the digital controllers DGT300.
The EMP brakes apply a controlled torque to the web shaft to maintain a constant tension during winding or unwinding.
The EMP technology is both extremely reliable (very long maintenance free service life) and often simpler to integrate than friction systems as well as being more economical and much easier for users to control than motor & drives based systems. “The most remarkable difference is also its reliability”, explains François Bayzelon. This reliability results from numerous technological improvements: innovating surface treatment especially formulated to limit wear, the special steels chosen incorporating optimized magnetic properties, ball bearings optimized to resist to high temperatures. Furthermore, Andantex USA’s expertise in this technology allows the design teams to precisely simulate the machines working conditions and thus to select the cooling system that satisfies the complex application (cooling fins, axial ventilation, radial ventilation or water-cooling systems). The residual torques has been extremely reduced and magnetic circuits optimized to considerably increase the linear operating range. The EMP brakes and clutches are clean. Design ensures faultless sealing towards the outside, which naturally qualifies this technology for use in environments where dust emissions are prohibited (for example, food or pharmaceutical industries).
The DGT 300 digital controllers have been job-designed for the Converting and label trade. They regulate web tension no matter what the constraints: product elasticity, coil inertia, cyclic operation, great variations to the diameter, etc. Their extensive multipurpose capabilities ensure the control in open loop as well as closed loop regulation applications, which is the case for ETI for whom ANDANTEX USA also supplies load cells. The MEROBEL solutions are incorporated in all equipment manufactured by ETI, such as winding and unwinding stations and intermediate tension stations. Using a highly user friendly Windows PC interface or the front panel keyboard, the DGT300s allow the definition of all application parameters required to start a web tension control system: emergency stopping proportional to the set point, smooth start-up, freewheel and blocking modes, taper coefficient and non-stop web replacement on the fly. Numerous regulation mode optimization functions are also available such as variable PID coefficients, open loop + closed loop, inertia compensation, and also a special algorithm for use with motors, where applicable. This family of digital regulators, compatible with all usual sensor technologies, whether ultrasound sensors or all types of position and force sensors presents the advantage of incorporating a very simple calibration mode as it is fully digital. Remote maintenance and trouble shooting by MEROBEL teams is also available.
“We obtain an accuracy of 0.1 mm. The advantage of the Merobel solution in relation to a solid state electronic system is that we maintain better control of the process”, concludes Mr. Bayzelon.
ETI is a Canadian company. Its turnover is worldwide: 25% in North America, 25% in Europe and 50% in the remainder of the world. ETI operates in 25 countries and manages 2 production sites employing 50 people each, one at Boucherville in Québec, and the other at Shanghai in China.
The latest ETI substrate pretreatment system is called ETI Corona Plasma Optimum, or more commonly the ETI-CPO. This treatment is applied in an enclosure under a controlled inert gas environment. It sends a corona discharge to the surface of the film (PP, BOPP or PET), allowing the surface energy to be increased which provides for excellent wetability and superb adhesion of the glue, ink, or any other coating. The ETI-CPO system may be used with the COHESIO or upline on the rotary press printing the front before glue coating.
This frontline technology requires perfect web tension control. “Web tension control is necessary no matter what sector is involved in the Converting field. For us, it is even more critical as the films are very thin (15 to 20 µm). We use feed speeds of 120 m/minute. The web may then stretch 40 mm. Without excellent tension control, the register cannot be perfectly controlled and it is then impossible to implement our system. The chosen system becomes a strategic choice. We have analyzed all proposals available on the market and chose ANDANTEX, simply because they are the best. Technical assistance also played a deciding role. MEROBEL products are mounted on all our equipment, COHESIO or METRONOME. ANDANTEX USA also had the foresight to believe in the potential of the company since its founding.”
The MEROBEL web tension control system mainly consists of 2 complementary components: the EMP brakes and the digital controllers DGT300.
The EMP brakes apply a controlled torque to the web shaft to maintain a constant tension during winding or unwinding.
The EMP technology is both extremely reliable (very long maintenance free service life) and often simpler to integrate than friction systems as well as being more economical and much easier for users to control than motor & drives based systems. “The most remarkable difference is also its reliability”, explains François Bayzelon. This reliability results from numerous technological improvements: innovating surface treatment especially formulated to limit wear, the special steels chosen incorporating optimized magnetic properties, ball bearings optimized to resist to high temperatures. Furthermore, Andantex USA’s expertise in this technology allows the design teams to precisely simulate the machines working conditions and thus to select the cooling system that satisfies the complex application (cooling fins, axial ventilation, radial ventilation or water-cooling systems). The residual torques has been extremely reduced and magnetic circuits optimized to considerably increase the linear operating range. The EMP brakes and clutches are clean. Design ensures faultless sealing towards the outside, which naturally qualifies this technology for use in environments where dust emissions are prohibited (for example, food or pharmaceutical industries).
The DGT 300 digital controllers have been job-designed for the Converting and label trade. They regulate web tension no matter what the constraints: product elasticity, coil inertia, cyclic operation, great variations to the diameter, etc. Their extensive multipurpose capabilities ensure the control in open loop as well as closed loop regulation applications, which is the case for ETI for whom ANDANTEX USA also supplies load cells. The MEROBEL solutions are incorporated in all equipment manufactured by ETI, such as winding and unwinding stations and intermediate tension stations. Using a highly user friendly Windows PC interface or the front panel keyboard, the DGT300s allow the definition of all application parameters required to start a web tension control system: emergency stopping proportional to the set point, smooth start-up, freewheel and blocking modes, taper coefficient and non-stop web replacement on the fly. Numerous regulation mode optimization functions are also available such as variable PID coefficients, open loop + closed loop, inertia compensation, and also a special algorithm for use with motors, where applicable. This family of digital regulators, compatible with all usual sensor technologies, whether ultrasound sensors or all types of position and force sensors presents the advantage of incorporating a very simple calibration mode as it is fully digital. Remote maintenance and trouble shooting by MEROBEL teams is also available.
“We obtain an accuracy of 0.1 mm. The advantage of the Merobel solution in relation to a solid state electronic system is that we maintain better control of the process”, concludes Mr. Bayzelon.
ETI is a Canadian company. Its turnover is worldwide: 25% in North America, 25% in Europe and 50% in the remainder of the world. ETI operates in 25 countries and manages 2 production sites employing 50 people each, one at Boucherville in Québec, and the other at Shanghai in China.