www.magazine-industry-usa.com
03
'18
Written on Modified on
Global Tool Deterioration Analysis Looks Beyond Machining
Cutting tools are fundamental elements of the metalcutting process. Depending on how the tools are chosen and applied, they offer the potential to maximise machining productivity or, on the other hand, create production bottlenecks. Much depends on how tool use is managed in relation to the overall manufacturing process.
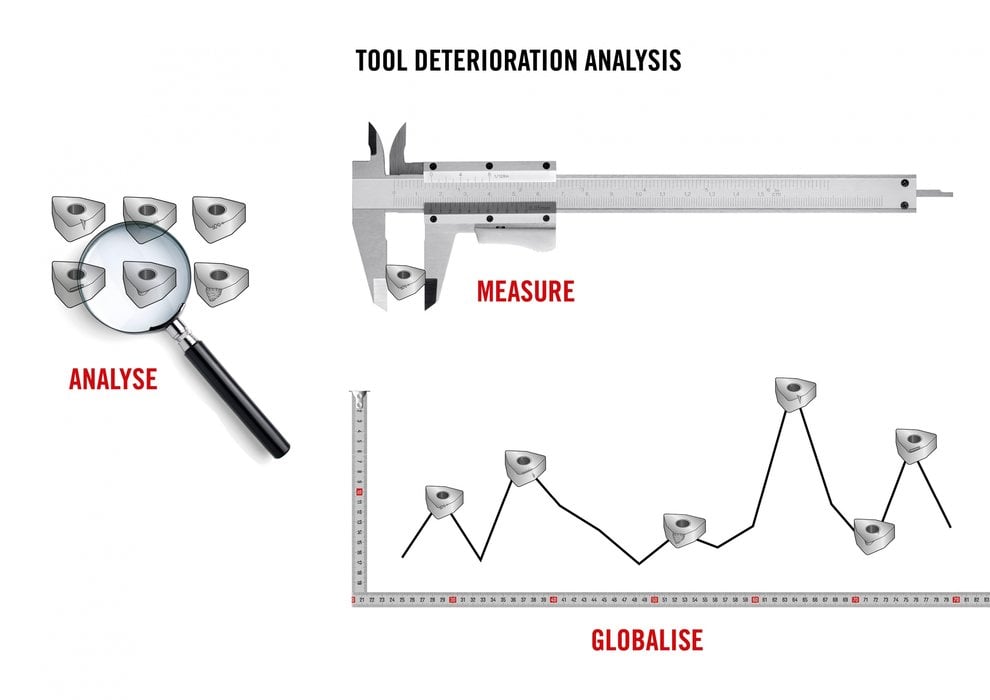
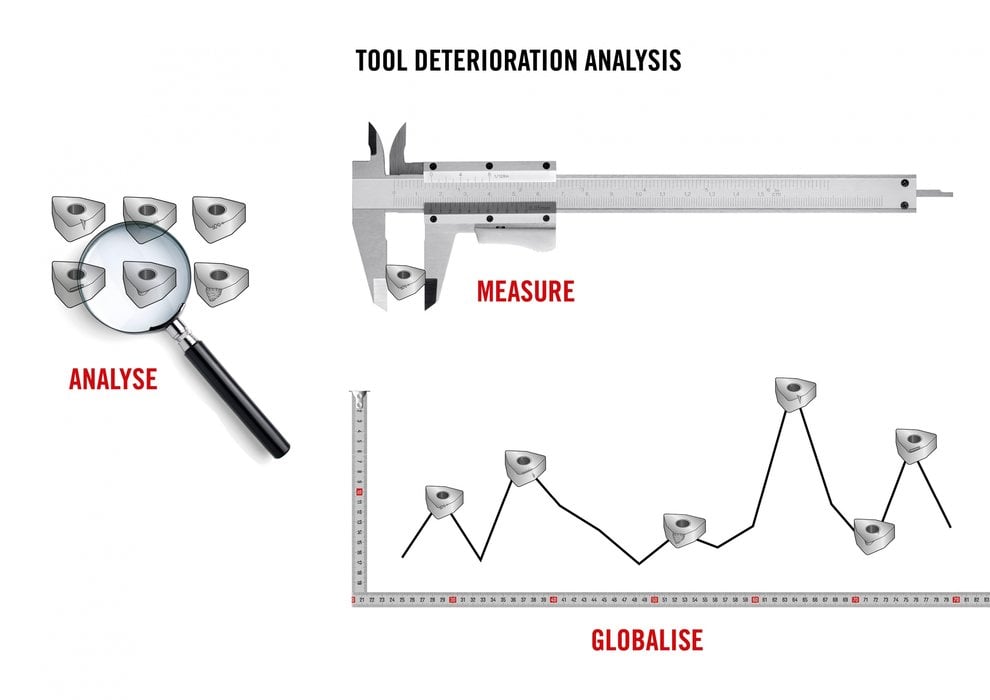
HQ_ILL_Tool_Deterioration_Analysis.jpg
Figure 1
Cutting tools are by their nature consumable; they wear until they are no longer effective. A traditional approach to metalcutting tool management employs wear analysis alone, focused on manipulating tool materials, geometries and application parameters to improve part output and tool life in a selected operation. Maximising the efficiency of a facility’s entire manufacturing process, however, involves consideration of a broad range factors in addition to tool wear. It is essential to examine cutting tool wear or, more broadly, tool deterioration, in light of the overall or “global” manufacturing process.
Global Tool Deterioration Analysis (GTDA) goes beyond basic measurement of tool wear to include tooling-related considerations such as time spent in tool manipulation, problems other than wear, production economics, shop organization, personnel attitudes and assumptions, value stream management, and total manufacturing costs. GTDA is based on regular evaluation of a large number of a shop’s used cutting tools randomly selected to construct a comprehensive picture of their contributions to the facility’s manufacturing efforts overall.
The Global Manufacturing Process
Study of tool wear usually is limited to a single tool employed in a specific machining operation. However, to gain maximum benefits, it is essential to examine tool wear or deterioration in relation to all tooling in a facility’s manufacturing processes. The manufacturing process (Figure 2) begins with acquisition of raw materials and planning that involves utilisation of human intellect, technological resources and capital investment. The process advances through value-adding and value-enabling activities but may be restrained by waste-producing events that result in the loss of money, time and intellectual resources and consequently reduce part quality and yield. Output is measured in terms of part quality, the quantity required and desired production time and cost.
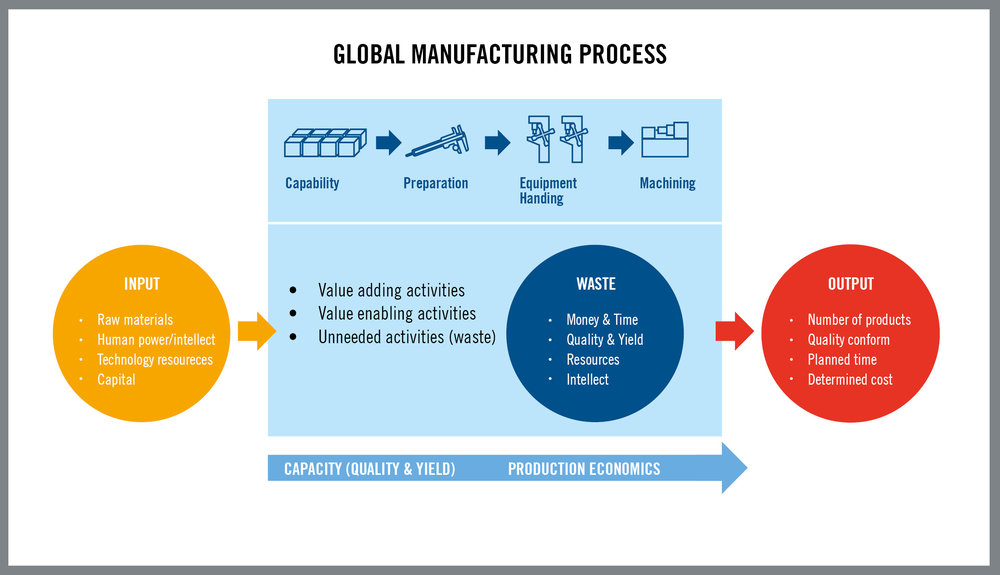
Figure 2
Manufacturing Process Evolution
The methods used to analyse and predict tool life depend on the way in which the tools are applied. Over the centuries, manufacturing practices evolved from craft-level output of individual items to mass production of standardized parts. Improving manufacturing methods then brought about a second generation of mass production capable of producing increasingly greater volumes of similar parts – a high volume, low product mix (HVLM) scenario. Most recently, digital technology as applied in programming, machine tool controls and workpiece handling systems is facilitating a third generation of mass production that permits cost-efficient, high-mix low-volume (HMLV) production.
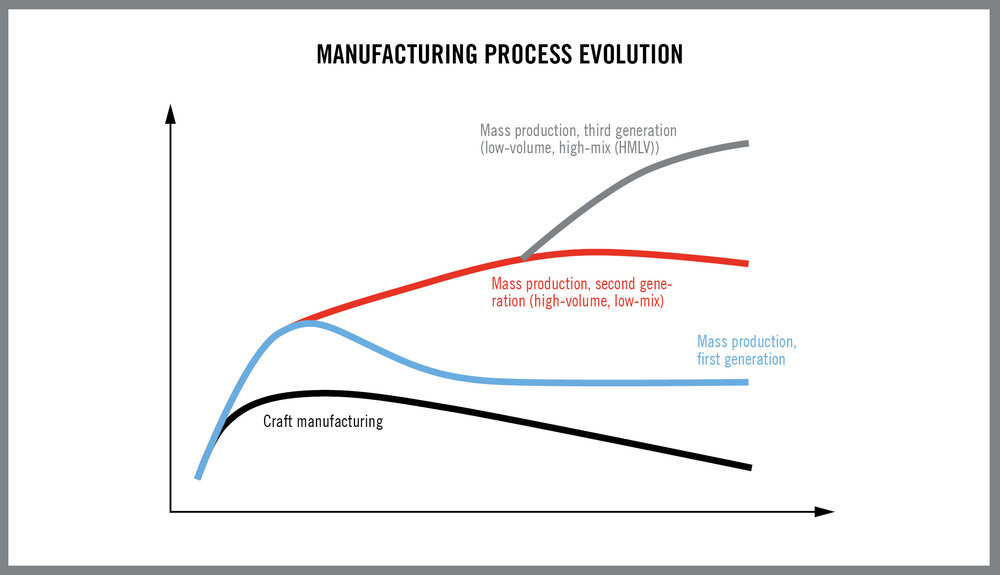
Figure 3
Although the key performance issues remain the same – namely achieving cost and time efficiencies, a certain minimum quality and a certain level of yield – second- and third-generation mass production techniques require different approaches to tool life analysis. In a second-generation HVLM scenario, identical parts are machined from the same workpiece material in production runs that may last days, months or years using the same equipment and the same kind of cutting tools. In that situation, tool life management is relatively simple. Shop personnel use prototyping and trial runs to determine the best average tool life, then divide the desired volume of parts by the expected life of individual tools.
Consistent tool life expectancy data enable a shop to plan tool changes that maximise tool utilisation and support continuous production. However, HVLM production methods are declining in prominence. To balance part inventory with demand and accommodate ongoing engineering changes, manufacturers are machining fewer and fewer parts in long, unchanging production runs.
At the same time, third-generation HMLV mass production strategies are growing in acceptance. Rapidly adjustable HMLV processes match well with contemporary inventory and engineering goals, but the planning process is much more complex. A run of ten parts may be followed by part lots of two, five or even a single component. Workpiece materials may change from steel to aluminum to titanium, and part geometries from simple to complex. There is not enough time available to determine tool life through trials.
In such cases, a workshop typically makes a conservative guess regarding a tool’s projected life and, to be safe, employs a new tool for each run then discards it well before the tool reaches its actual productive lifespan. A more global approach to tool wear analysis and predictions can help minimise waste of cutting tool capability.
Binary Yield Possibilities
Rapidly changing HMLV manufacturing methods increase the difficulty of achieving high percentage yields for machining operations. In the case of long-run HVLM production, trials and adjustments can produce yield percentages in the high nineties. On the other hand, yield in the HMLV situation may be binary. A successful single part run represents 100 percent yield, but when the part is unacceptable or a workpiece is ruined, the yield is zero.
Demands for quality and cost and time efficiency remain the same, but first-time yield becomes an overriding requirement. In that case, avoiding tool breakage is perhaps the most important consideration. One advantage is that tool wear is a minimal concern in short run situations and a shop can apply, within reason, more aggressive and productive cutting parameters.
Craftsmanship and the Human Contribution
Lengthy and unchanging HVLM production runs tend to minimize the importance of human contributions to the manufacturing process. After a long run is initiated, operations can essentially be automated. Even in cases where an operator participates in every changeover between parts, the repetitive nature of these situations marginalizes the influence of operators and programmers. Flexibility is not required, and perhaps even discouraged.
On the contrary, rapidly changing HMLV scenarios reemphasize the role of humans in the process, to the point that the operations require a form of traditional craftsmanship involving creativity and flexibility to efficiently adapt to the continually changing parts and cutting conditions characteristic of HMLV machining.
Focus On Process Before Results
Many manufacturing process analysis efforts focus on reviewing end results in relation to tool life and part output without thoroughly examining the process itself. Problems related to cutting tools, but not directly to tool life, may be missed and create production bottlenecks. For example, burrs typically are not related to tool life, but their occurrence interrupts the manufacturing process because another operation must be developed and implemented to remove the burrs.
Burr formation is, however, related to tool geometry and application parameters and therefore must be considered in tool deterioration analysis. Tool breakage, another problem not usually related to tool wear, does involve tool material, geometry, application parameters as well as machine tool factors.
Elements of Operational Excellence
The basic components of manufacturing efficiency are elimination of waste, inflexibility and variability. Comprehensive tool deterioration analysis takes into account five elements of operational excellence.
First, it is essential to thoroughly understand the overall machining process and the relationship of the machining operation to the workpiece material. Second, attention must be given to waste reduction, through lean manufacturing strategies and other initiatives. Third, the concepts of production economics need to be employed to assure profitability. Fourth, percentage yield goals should be viewed in light of manufacturing volume and part variety; maximising flexibility must be viewed as a way to minimise bottlenecks, but variability has to be controlled to assure consistent part tolerances. Finally, it is necessary to emphasize the value of manufacturing personnel to gain maximum benefit from the unique and irreplaceable resource it represents.
Considerations Beyond Tool Wear
Global tool analysis supplements initial measurement of insert edge wear with analysis of the tools’ role in Cost of Goods Sold (COGS) totals, Single-Minute Exchange of Die (SMED) analysis, Value Stream Management (VSM) results and Overall Equipment Effectiveness (OEE) percentages.
The most basic tooling-related economic consideration is clear: tools cost money. Figure 4 presents the cost of various elements of the machining process and totals them as COGS. These data enable a shop to compare and contrast the various elements of production costs, with an eye on finding candidates for cost reductions that will boost operational profitability.
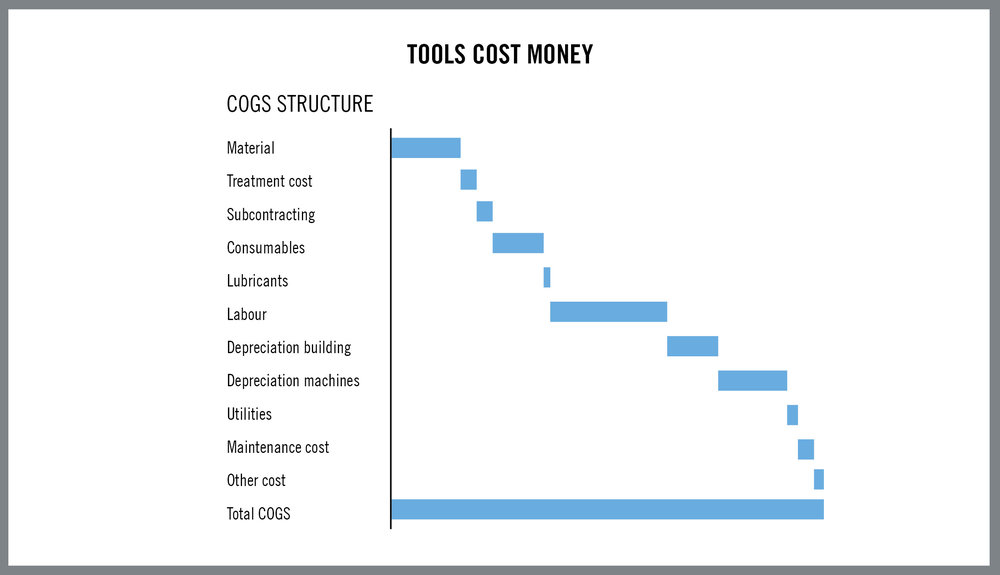
HQ_ILL_Tools_Cost_Money.jpg
Figure 4
Another tool-related economic factor is that tools cost time – the time involved in manipulating tooling outside of actual machining operations. Time spent in tool changeover and setup is analysed via SMED analytical techniques that also provide a view of costs beyond those generated by tool wear and replacement. Part of that expense is incurred in acquiring and organizing tooling and mounting it and loading programs into the machine tool.
OEE determines how much of the available manufacturing time is used effectively. OEE analysis points out losses, benchmarks progress and improves productivity by eliminating waste. The total time available for production is identified, then the analysis subtracts planned downtime, unscheduled breakdowns, changeovers, minor stops and lost speed, and scrap and rework to arrive at effective machining time expressed as a percentage of the total time available. A 100 percent OEE – a noble but practically unattainable goal –means a part is produced in the specified quality, as fast as possible, with no wasted time.
VSM analysis illustrates the need to balance performance improvements among all the elements of the manufacturing process. Figure 5 is a graphic representation of the effects of improving the performance of one element of a system without improving others. Think of individuals rowing a boat. Higher performance by one rower would actually hurt the boat’s overall performance.
Improvements in parts of the process must be made in view of their relation to production volume and variety, workpiece material characteristics, part geometries, machine tool and fixturing requirements and other considerations to achieve and maintain a manufacturing operation that is in balance overall.
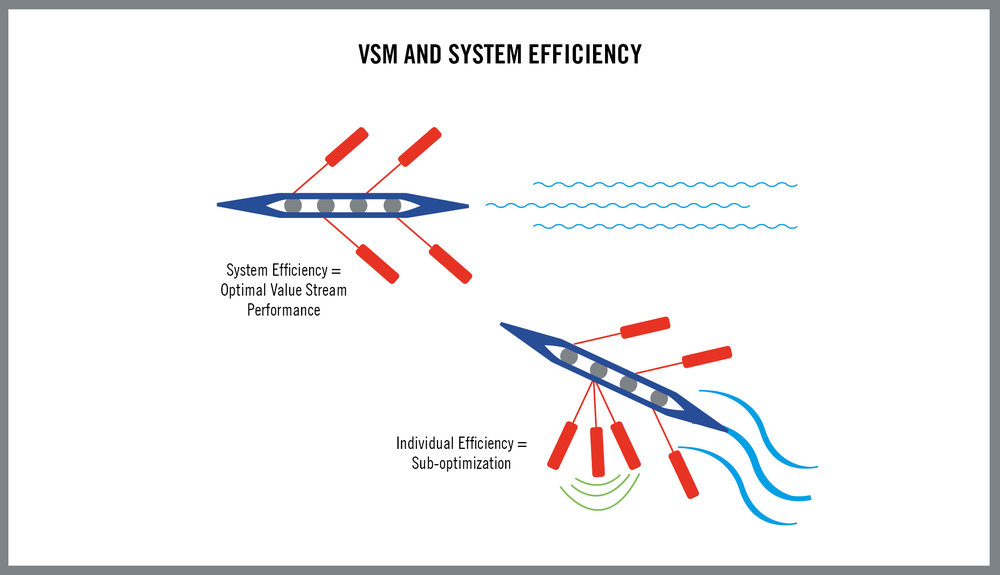
Figure 5
Global Tool Deterioration Analysis
GTDA is basically a simple process. The cutting edges of a large number of randomly chosen tools from throughout a shop are examined one edge at a time to determine which edges are worn. The wear is classified according to its type and amount. Traditional tool wear analysis concentrates on one tool in one operation; GTDA gathers information about tool wear and other tool-related issues from the entire shop, then applies COGS, SMED, VSM, OEE and other analytical tools to compile additional data that will guide planning and implementation of improvement programs.
To be successful a shop must have the discipline to begin a GTDA program and, equally important, continue tool examination and data analysis on a regular basis. Another form of discipline – honesty – is required as well. A shop must honestly and objectively accept the results of the analysis and be willing to act on the findings without regard to shop traditions and politics or unsupported opinions regarding tool application parameters.
Conclusion
Tool wear is inevitable and managing it is essential to achieve successful machining operations. However, tool wear is just one example of the many influences of cutting tools on the efficiency of a facility’s overall manufacturing process. GTDA goes beyond wear analysis of single tools to include all the tools in a shop as well as a wide range of significant tool-related influences outside the cutting process.
Sidebar:
GTDA: Why and How
At the peak of the era of high-volume mass production of individual parts, tool wear was simply measured, manipulated and balanced to maximise tool life and part output. As manufacturing strategies have progressed into a more just-in-time production of near-custom components, tool wear by itself has become a less central element of the manufacturing process overall.
Seco Consulting Services continually analyse ongoing manufacturing evolution and has developed its “NEXT STEP” production model to deal with the continual changes in the manufacturing industry (Figure 6). The NEXT STEP model is based on the four key standards of machining, namely cost efficiency, time efficiency, quality and yield. Next Step enables manufacturers to set and meet machining standards for themselves through analysis of waste production, machining process technology, tooling and workpiece material science, production economy and yield, and the critical role of people and leadership in their operations.
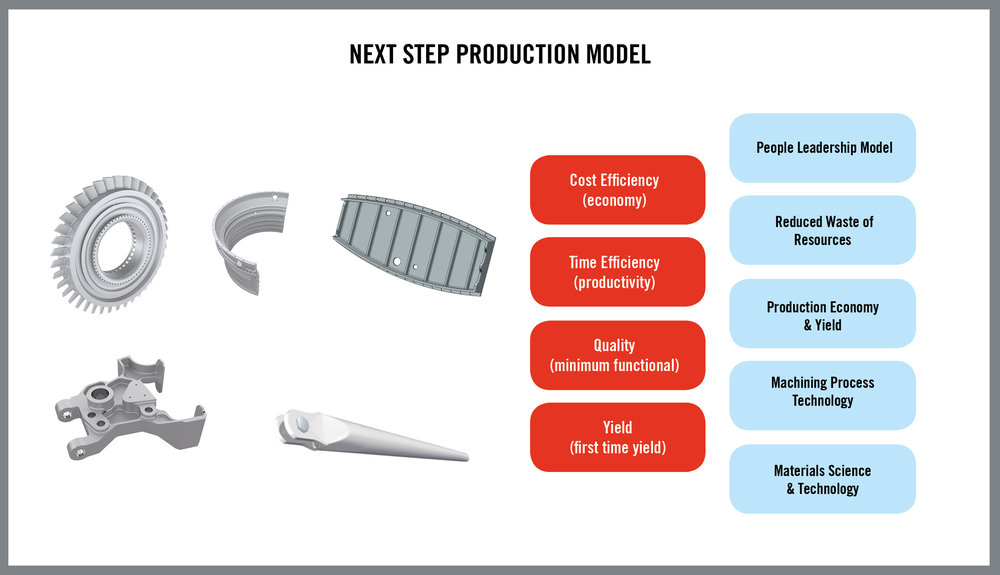
HQ_ILL_Next_Step_Production_Model.jpg
Figure 6
Global Tool Deterioration Analysis (Figure 7) is a key component of overall manufacturing process evaluation and improvement. By examining a random selection of tools covering all machining areas of a facility, then applying a variety of production measurements, a manufacturer gains a broad understanding of the role that tooling plays in the entire machining process. GTDA helps shops discover where tool performance can be improved to boost productivity, and where tooling-related issues may be creating time- and money-wasting bottlenecks in the manufacturing flow.
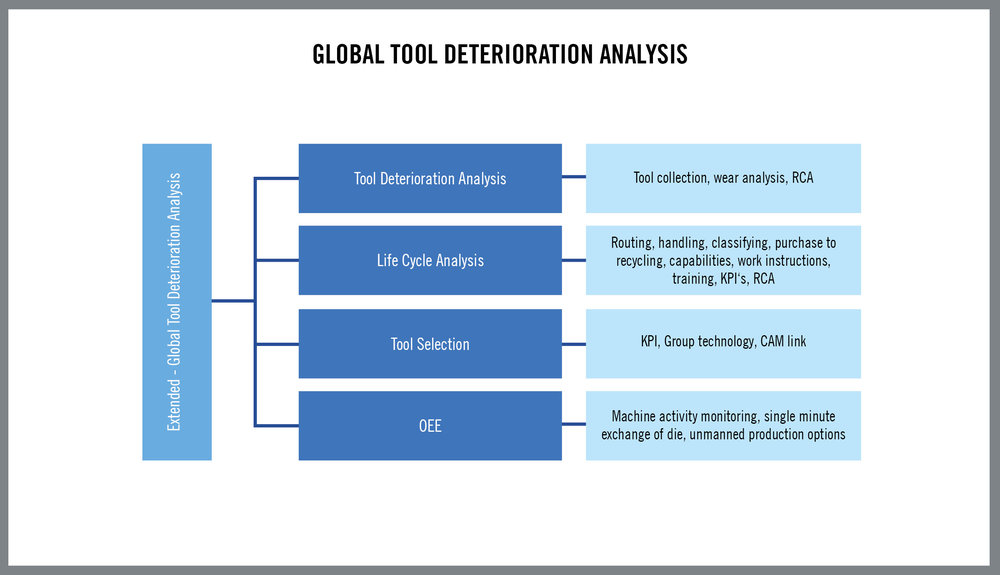
HQ_ILL_Global_Tool_Deterioration_Analysis.jpg
Figure 7
On the specific subject of GTDA, Seco Consulting Services have produced a text book entitled “Tool Deterioration: Best Practices” (Figure 8). The book presents tool deterioration as a balancing point for machinability models, noting that most problems in machining processes can be classified as tool deterioration-related events. The guide discusses different applications in metalcutting and is intended a to provide an insight in the phenomena that cause tool deterioration, while also offering a “best practices” overview on how to identify, handle, and control tool deterioration processes.
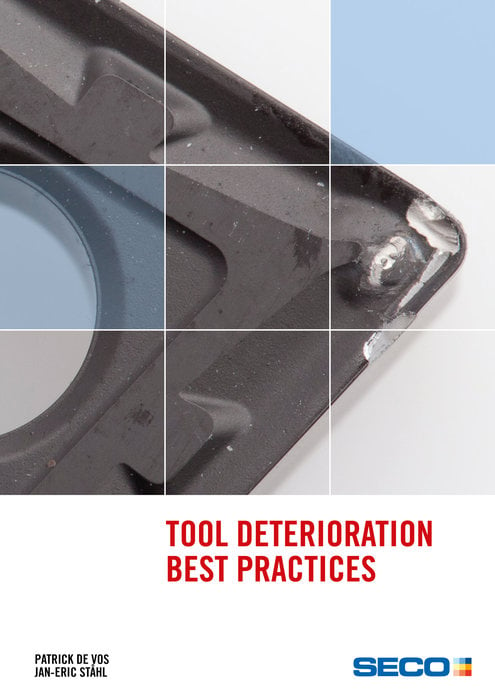
HQ_IMG_Tool_Deterioration_Best_Practices_2014.jpg
Figure 8
By:
Patrick de Vos, Corporate Technical Education Manager, Seco Tools