www.magazine-industry-usa.com
14
'17
Written on Modified on
Logistics is a competitive factor for us
Bürkert Fluid Control Systems automates the supply process for assembly
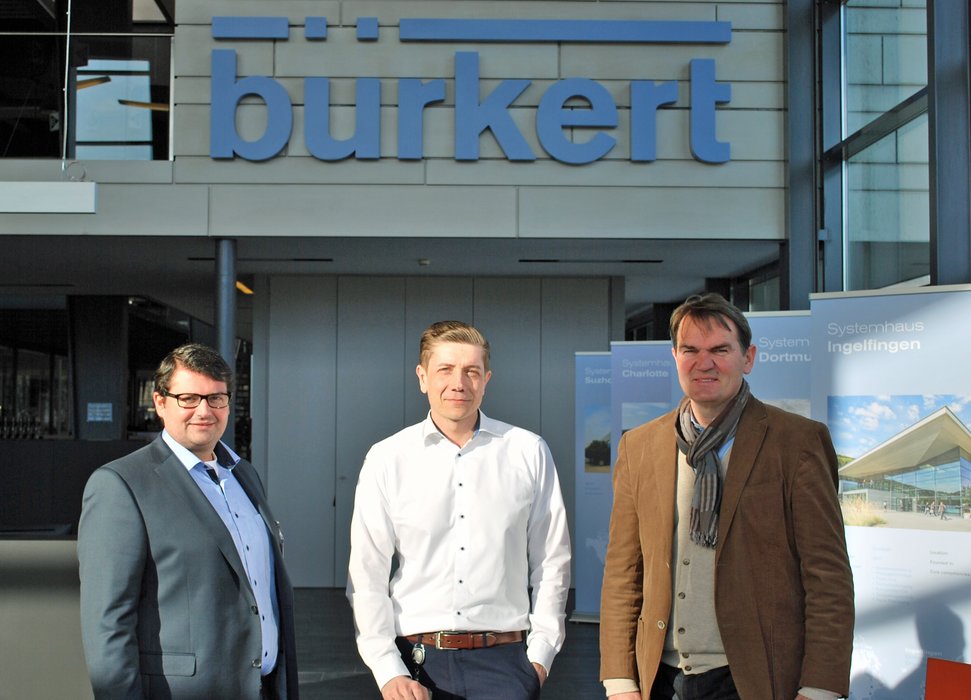
With the relocation of production and logistics to the new "Campus Criesbach" location, the Ingelfingen-based system manufacturer Bürkert Fluid Control Systems has significantly increased the degree of automation in the production processes. Also used in the intralogistics portion of the project, planned and implemented by general contractor SITLog, are various Leuze sensors.
It was a decision for the future – and a commitment to Germany as a business location: At the end of 2016, the Bürkert Fluid Control Systems company brought into operation its new plant at the Campus in Criesbach, not far from the company headquarters in Ingelfingen. The manufacturer of measurement and control systems for liquids and gases invested a total of 30 million euros in the new building. "Our primary goal was to reduce the lead times in assembly to strengthen our competitive position for the long term," says plant manager Marc Steffen Dahlheimer. "For this reason, we decided to significantly increase the degree of automation in intra-company logistics processes for supplying assembly operations and simultaneously maintain the flexibility in production." In this regard, managing the many different variants is one of the greatest challenges in daily operation. This is because Bürkert primarily supplies complete solutions for customers, some with highly customized configuration. It is therefore necessary to keep a range of different parts on hand and to efficiently bring them to the assembly line. For this order-related production, automated logistics is a great advantage. The intralogistics general contractor SITLog executed the control technology and visualization of the system under its own direction. "We realized the steel construction for the automated small-parts warehouse, the mechanics for the high-bay storage devices and materials handling, the fire-protection gates, the platform for the front zone of the automated small-parts warehouse, the manual pallet warehouse as well as the delivery of the workbenches to the individual workstations through additional purchases," explains Christian Hauser, project manager at SITLog. The main challenge here was the management of the different types of storage and transport containers already in use by Bürkert. "During the project, we concentrate on our core competencies of control and IT – all other components we procure from our partners, some of whom we have worked with for many years," says Hausner. "We thereby simply achieve the best result for our customers."
Automated small-parts warehouse is the heart of the system
This comprehensive approach convinced Bürkert as well. "We selected SITLog because we see the technical requirements in areas such as the number and design of the storage spaces or the connection via the materials handling system met here in the best possible way," says Dahlheimer. "And, by integrating external partners who have a high level of specialized know-how in their respective fields of business, we were able to realize a solution that was optimized for us in all regards." After all, no Bürkert customer is willing to pay for logistics services, but rather for the quality of the products and services. Fast, error-free delivery is something that is simply assumed today – and that with a guaranteed standard delivery time of five days worldwide for products from the main product line. "This is not something we could afford without a functional, efficient intra-company logistics system. Furthermore, the products would be unaffordable for our customers," says Dahlheimer. "For this reason, we view logistics as a true competitive advantage." Bürkert's new, fully automated container warehouse currently has a capacity of approximately 27,000 storage spaces in three aisles with double-deep storage. Used are two different container sizes with dimensions of 600 x 400 mm and 465 x 315 mm and a load capacity of up to 20 kg. Multi-order picks can be performed at the total of four order picking workplaces, i.e., picking of the same components for multiple, parallel orders – a decisive time advantage in the highly competitive market. Also available are two conveyor lines for the production connection, twelve primary packaging workplaces and three outgoing goods lanes. The handling capacities of the automated small-parts warehouse are impressive: 285 double cycles per hour, 400 containers per hour in both order picking and production as well as 600 containers per hour in both primary packaging and empty container return.
Solutions from mid-size companies for the mid-size market
Important tasks for smooth material flow are performed by optoelectronic products. Used in the high-bay warehouse with pre-storage zones and order picking area are the BCL 348i, AMS 348i and DDLS 500i product solutions from Leuze electronic. The BCL 348i stationary bar code reader with integrated Profinet interface, together with the AMS 348i optical distance measurement system, performs very complex tasks in this project. The bar code reader reliably performs the bar code identification of the containers and their content, and the AMS laser positioning system ensures the positioning of the high-bay storage devices. The DDLS 500i is the first optical data transmission photoelectric sensor with integrated web server for worldwide, location-independent remote diagnostics. It makes it possible to wirelessly transmit the data in industrial networks from moving system parts in conveyor systems, such as high-bay storage devices, gantry crane bridges or side-tracking skates, and to do so without interference over longer distances, too. The data transmission photoelectric sensor is used for the optical data transmission of all Ethernet-based data protocols – such as the Profinet system used at Bürkert – with a real-time transmission speed of up to 100 Mbit per second. "From this project, it is clear that warehouse automation absolutely makes sense, even for mid-size companies," says Josef Apfelbeck, key account manager at Leuze electronic. "It doesn't always have to be large applications with tens of thousands of items in the product range." And of course, it is certainly no disadvantage that the participating partners – Bürkert, SITLog and Leuze – are all mid-size companies as well as owner-managed. "This considerably simplifies the mutual understanding in certain matters and definitely played a role in the success of the project," says Apfelbeck.
Bürkert gives positive interim assessment
Bürkert is fully satisfied with what has been accomplished thus far. "Our customers order products with increasing frequency but in smaller quantities," says Dahlheimer. "With the solution now implemented, we have significantly reduced our lead times and shortened the delivery times to the customer." We are particularly proud of the fact that the move to the new location was successfully completed during running operation and without significantly affecting delivery quality – that, too, is an achievement of the participating logistics partners.
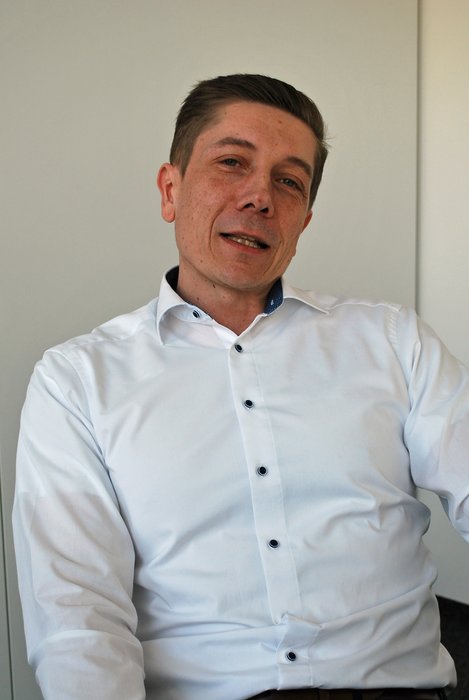
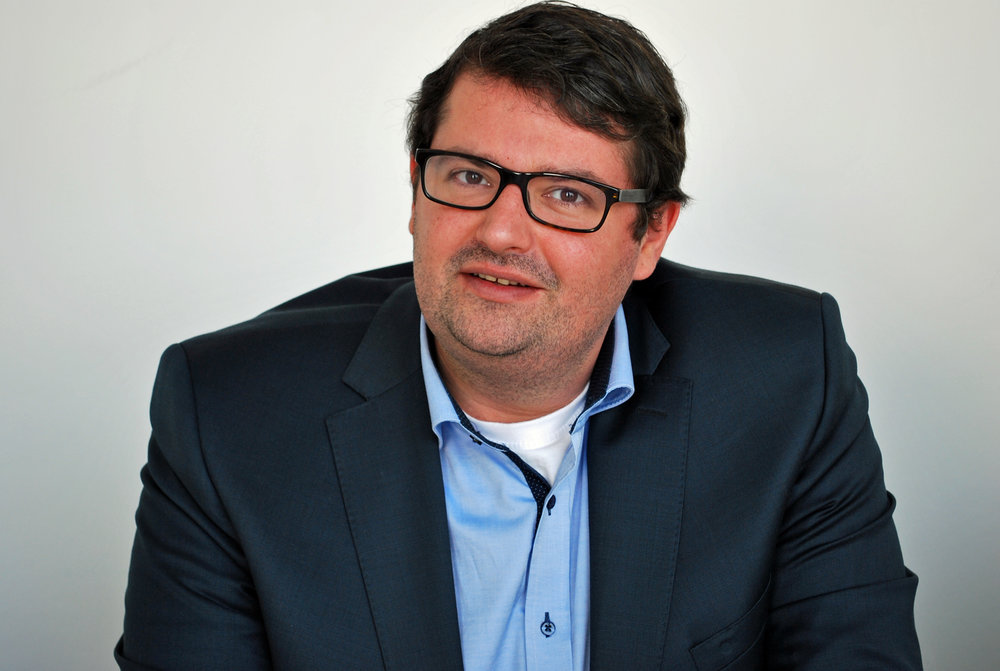
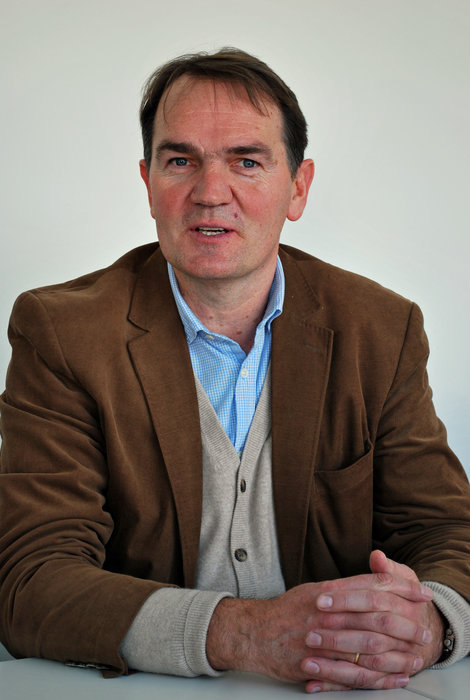
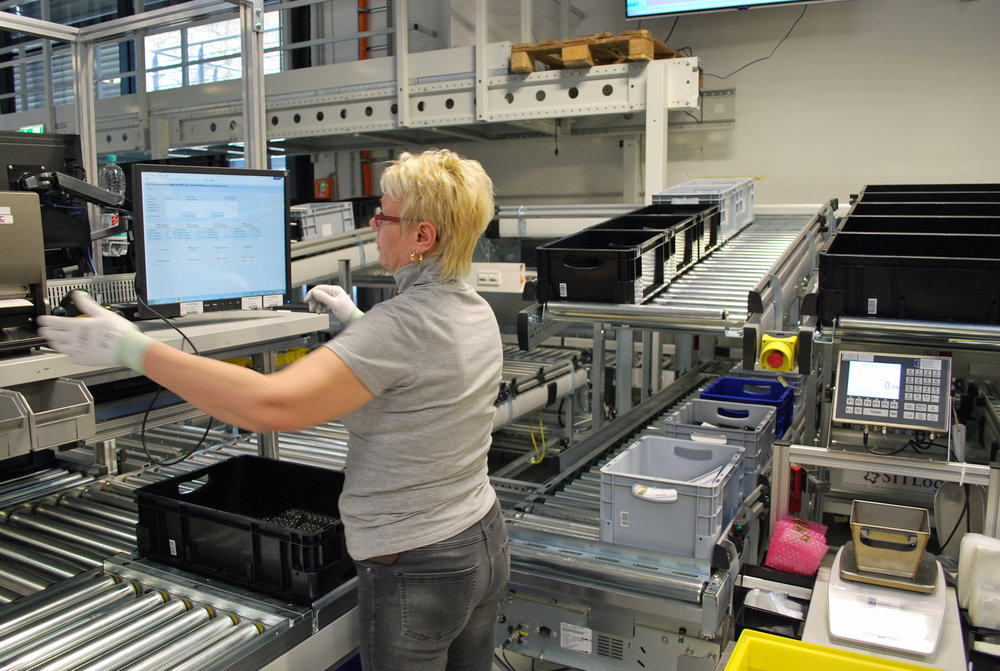
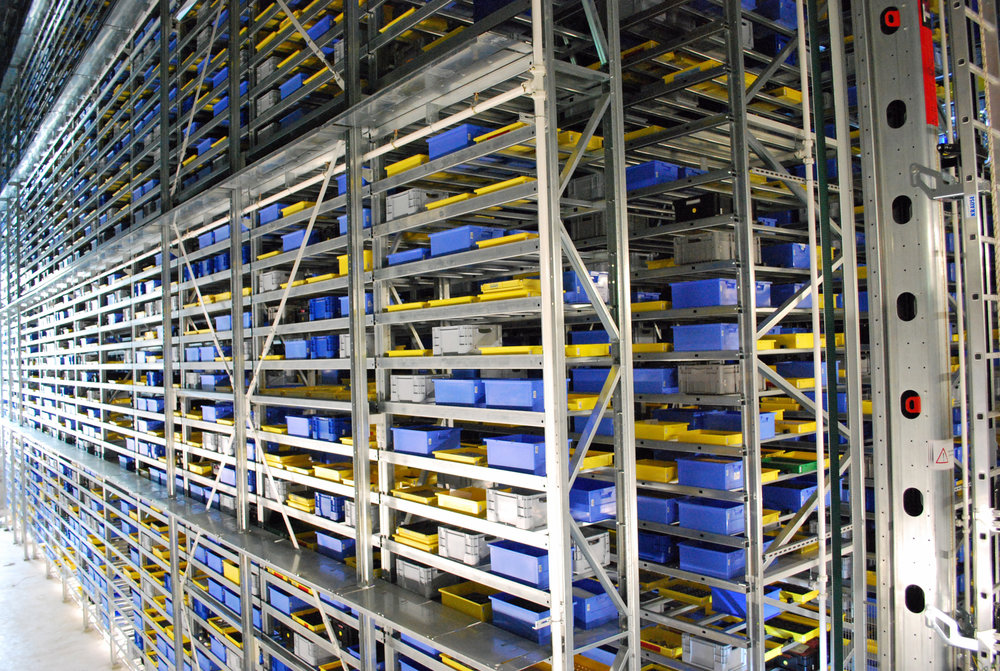
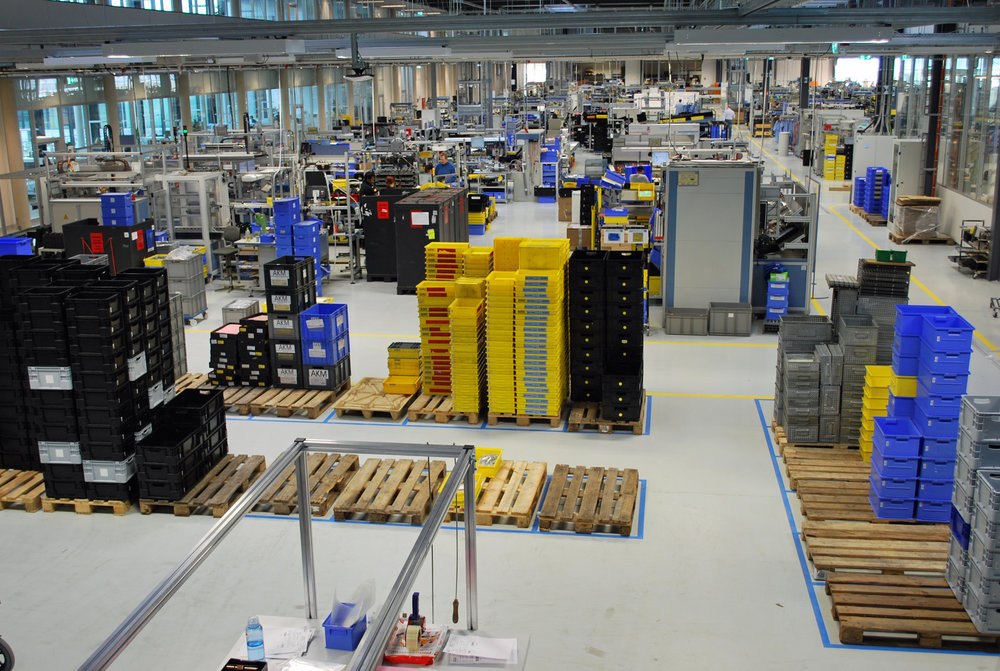
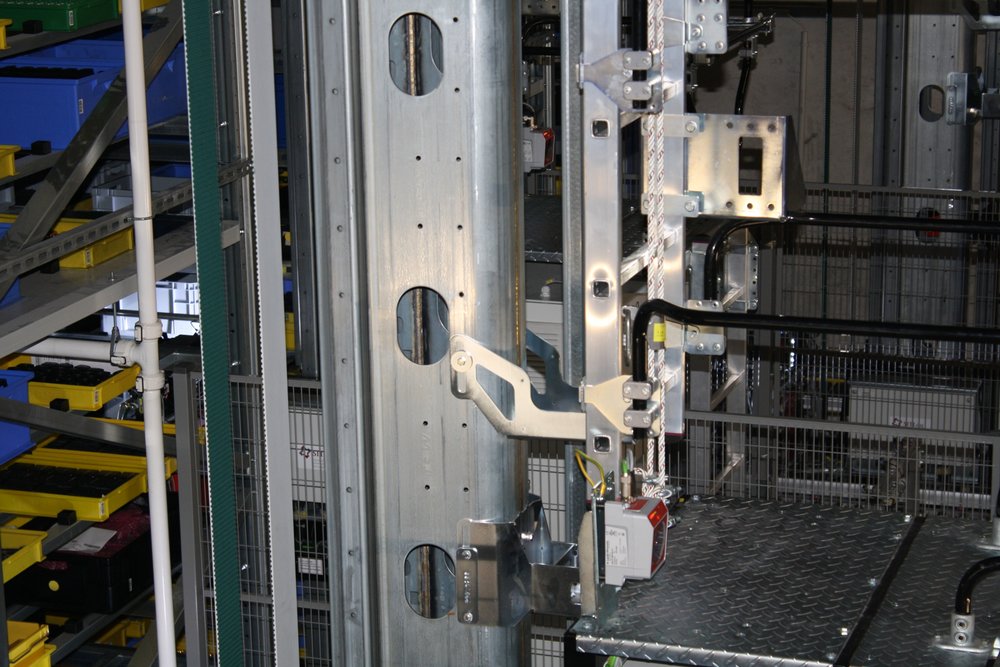
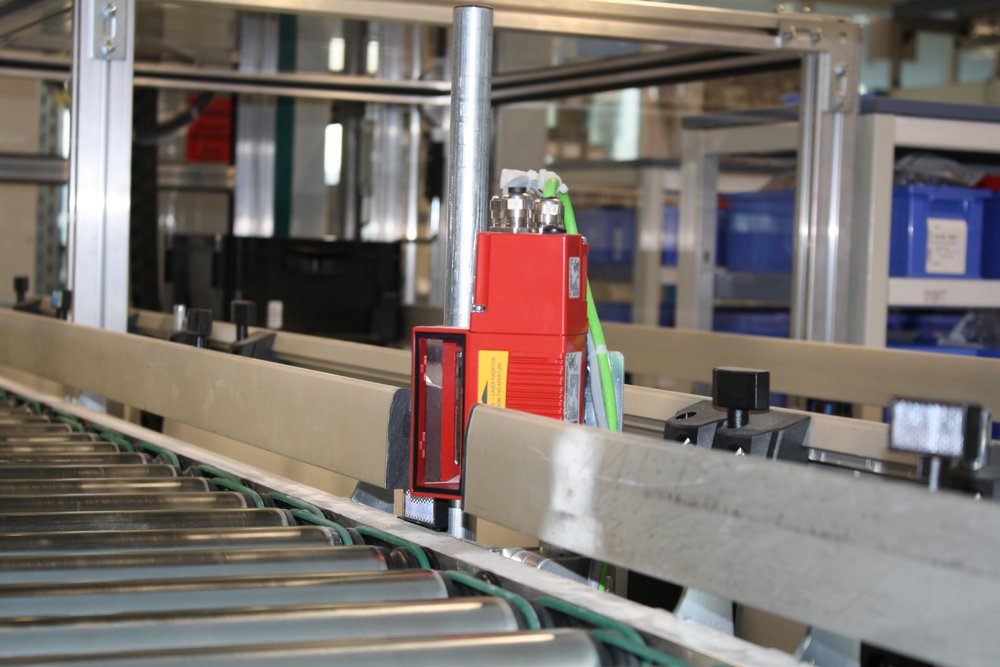
Participating companies
Bürkert
Bürkert Fluid Control Systems, with headquarters in Ingelfingen in the German state of Baden-Württemberg, is a leading global manufacturer of measurement and control systems for liquids and gases. More than 2,500 employees worldwide, 1,600 of whom work in Germany, generated sales of approximately 436.5 million euros in 2015. Products and systems are used in everything from brewery technology to laboratory and medical technology to space technology in more than 300 different industries. The product range includes solenoid valves, process and analysis valves, pneumatic actuators and sensors. In addition to the headquarters in Ingelfingen, Bürkert operates production facilities in Criesbach, Gerabronn and Öhringen as well as in Triembach-au-Val in the Alsace region. Two plants in China and the USA manufacture primarily for the respective local markets. The company is represented worldwide by independent subsidiaries in 36 countries. In addition, there are five system houses for customer-specific solutions in Criesbach, Dresden, Menden (Sauerland region), Charlotte, USA as well as in Suzhou, China.
SITLog
Since its founding in 2000, SITLog Steuerungs- und Informationstechnologie für Logistik GmbH, with headquarters in the Upper-Palatinate town of Altenstadt/Waldnaab, has realized projects ranging from retrofitting and new construction projects in intralogistics as system integrator of individual systems and components to turnkey complete solutions as general contractor. The core areas of the family-run company are control technology for materials handling and high-bay storage devices, warehouse management control and material flow control, visualization, emulation as well as service and maintenance. More than 16 years of experience and over 200 completed logistics systems distinguish SITLog. Just under 100 employees now work for the company. As a general contractor in the area of intralogistics for new installations and modernization, SITLog assumes the overall responsibility for all project-specific building work such as steel construction, ceilings and walls, mechanics, control technology and software.