www.magazine-industry-usa.com
07
'17
Written on Modified on
De Dietrich Process Systems is successful with Hygienic Drying in a Vacuum Spherical Dryer for API production. Fast drying. Emptied completely. Cleaned in a flash.
Following the manufacture by wet chemical processes, Active Pharmaceutical Ingredients are precipitated or crystallized out from the solvent. The subsequent steps are usually isolation and drying. Hygienic drying in a vacuum requires a lot of attributes. The innovative spherical dryer design provides the highest performance according process control and latest GMP standards. De Dietrich Process Systems is currently delivering several units in that field.
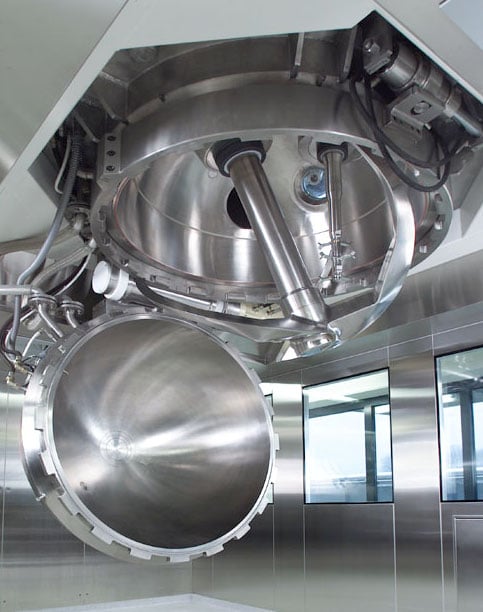
Important advantages at a glance
- Fast drying, mixing and granulation
- Easy cleaning (WIP/CIP)
- Total product discharge
- Short drying time due to high heat transfer design
- Easy to inspect by quick lock opening
- Explosion pressure shock resistant design
- Compact design allows easy installation in existing production buildings
The lower half of the sphere is removeable either by pivoting or dropping. This allows total and full visual and manual access to the process area and the accessibility, cleanability and a fast and residue-free discharge are the most important prerequisites for the production of high-quality products. Effective trouble free washing and cleaning (WIP/CIP) is required to maintain the systems in order to meet strict hygienic standards.
These conditions are a real challenge to agitated vacuum dryers and are met by the characteristics of the patented top driven Rosenmund® Spherical Dryer design.
Superior mixing with three arm agitator
The spherical dryer achieves a high grade of mixing via a three arm agitator specially designed to conform to the spherical wall. The agitator drive together with the shaft seal is mounted on the upper sphere. For sealing the rotation either gas or liquid lubricated double acting mechanical seals are supplied.
By heating the agitator and a high rational speed, the heat exchange can be increased. A reduced clearance between the body and the agitator improves the heat transfer and prevents wet goods from being baked onto the hub and blades. These are ideal conditions for excellent solid mixing in contact with the heated wall surface which results in short drying times and reproducible drying results.
To prevent the formation of agglomerates, a high speed chopper can break up the lumps and assist the removal of moisture from within.
Fully dischargeable
At the center and lowest point of the sphere, a dead-space free design of valve allows the product to flow without restriction and the risk of building bulk bridges. With this free passage and a gentle rotating agitator valuable products can be fully discharged without being jammed.
Pack off system
For the packing of the discharged product the dryer can be supplied with a pack off system. These systems are regularly supplied with a continuous liner to prevent active ingredients being exposed to the ambient. With a weighing scale and a permanent actuated discharge valve the product can be dosed to a preset value. A mill can also be placed between the discharge valve and the pack off system as an integrated part to achieve smaller particle sizes.
Cleaned in a flash
In the pharmaceutical industries federal agencies set requirements for cleaning process equipment. These good manufacturing practices are regulations put in place to ensure equipment is maintained in a clean and orderly fashion. The main concerns is to avoid contamination of the product and cross-contamination (by improper cleaning, bad maintenance) both of which can lead to product call-backs.
Due to the spherical design and the location of critical parts like the mechanical seal above the product level, washing and cleaning in place (WIP/CIP) procedures can be carried out efficient with minimum quantity of detergents. Moving and retractable cleaning ARD- Nozzles (Aftertreatment Regeneration Device) with rotating spray heads enter by pressure of the cleaning liquid from the vessel wall to the center of the sphere and enable a good coverage of the detergents on the product contacted surfaces. When the spraying is completed, the ARD nozzles retract themselves under spring load to be flush with the inner surface of the vessel, thus closing free of dead spaces. Due to the slope in direction to the outlet valve cleaning fluids and dissolved product residues are drained at the lowest point of the vessel.
For the purpose of conducting a qualitative coverage test of the spray devices, a riboflavin test can be performed to measure the accuracy of the cleaning. The results of this procedure can be useful for in the development of cleaning validation protocols.
Easy access for inspection
To allow a quick inspection at any time the Rosenmund® top driven spherical dryer can be opened easily by swiveling the lower half of the sphere. This operation is simply achieved by a hydraulic driven quick lock bayonet at the main flange and a hinge at the joint of the two spheres.
A further advantage of this partition into two halves is the possibility to install the dryer between two floors. The product discharge area with its lower part of the sphere can be located in a classified clean room whereby the upper part of the sphere is separated in the technical area.
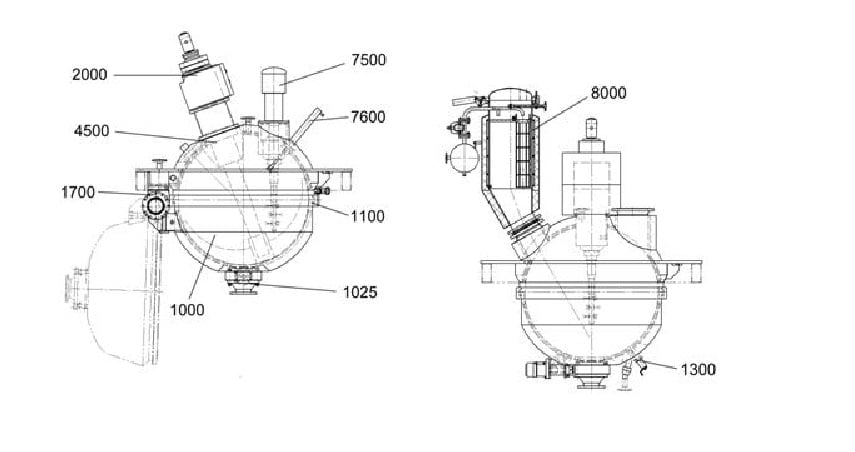
Module Description
1000 Sphere
1025 Discharge valve
1100 Quick lock (bayonet)
1300 Sampling valve
1700 Hydraulic actuated hinge
2000 Drive unit/Agitator
4500 Mechanical seal
7500 Chopper
7600 Spray balls (ARD nozzles)
8000 Dust filter
Versatile design features and sizes
Since dryers are usually designed for vacuum operation, the risk of thermal decomposition or dust explosion requires them to be designed for higher pressures in many cases. The spherical shape with maximum volume and minimum surface is the ideal geometry for an explosion containing shock resistant design.
The dryer can be manufactured either in stainless steel or, for high corrosive applications, in nickel alloys with high resistance to acids. The size ranges are from 100 to 4’000l net volume. The vessel is fully jacketed, insulated and covered by welded metal sheeting. Normally the dryer come along with skids for heating / cooling and vacuum including a condensation of the vapors. Particle fines which can be fluidized during drying are withheld by a dust filter with cartridges whereby the filtration media can either be made of a textile cloth or by a sintered wire mesh.
To optimize the performance it is important to adjust the peripheral equipment like heating / cooling and condensing / vacuum to match the specific requirements of the drying performance.
For heating / cooling mostly indirect loop systems are used in which a thermal liquid such as water, a glycol-water mixture, or thermal oil circulates through the dryer jacket. This liquid passes through a heat exchanger that respectively transfers the heat from the heat source (e.g. steam). Sensitive products may require rapid cooling at the end of the drying to maintain product quality so care must be taken that heat from the product can be removed to the coolant.
Condensers, typically shell-and-tube type, are used mostly to recover valuable process solvents which are evaporated during drying. Condensers used with dryers are operated in a way that vapors are condensed inside the tubes instead outside. The advantage is that the straight tubes bundles can be cleaned more efficiently.
For the fast and gentle drying at reduced evaporation temperature a vacuum system is required. A wide range of pumps are available on the market whereby screw or liquid ring vacuum pumps are generally used.
Optimizing and scale up the drying Process
Either to optimize existing processes or to develop the best possible process parameters for new or modified products, trials are recommended. The Rosenmund® spherical dryers cover a wide range of applications. From pure drying to combined processes with mixing and granulation results on drying and product quality can be optimized. Therefore pilot scale machines are installed at the site of the pharmaceutical manufacturer to implement the spherical dryer to the running process.
To summarize: Spherical dryers are the ideal dryer in the production of high valuable products like pharmaceutical ingredients. The spherical design allows a full discharge and cleaning can be performed easily to avoid the risk of cross contamination. From pure drying up to mixing and granulation the Rosenmund ®spherical dryer can cover a wide range of application. Due to the high heat transfer and optimized peripheral equipment drying time can be reduced significantly.
Rosenmund ® is a brand of De Dietrich Process Systems, dedicated to filtration, drying, containment solutions :
https://www.dedietrich.com/en/solutions-and-products/liquid-solid-separation
https://www.dedietrich.com/en/solutions-and-products/vacuum-drying-solutions
https://www.dedietrich.com/en/solutions-and-products/containment
De Dietrich Process Systems designs, produces and markets solutions based on equipment which uses glass-lined steel, stainless steel, special alloys, and borosilicate glass technologies respectively for the chemical and pharmaceutical industries.
De Dietrich's business also covers the engineering, planning, installation and commissioning of chemical units in materials resistant to corrosion and provides the corresponding service provisions.Founded in 1684, De Dietrich Process Systems has a strong global presence, with offices located in fifteen countries.
IMAGES
Three arm agitator with enhanced heat transfer design and high speed chopper
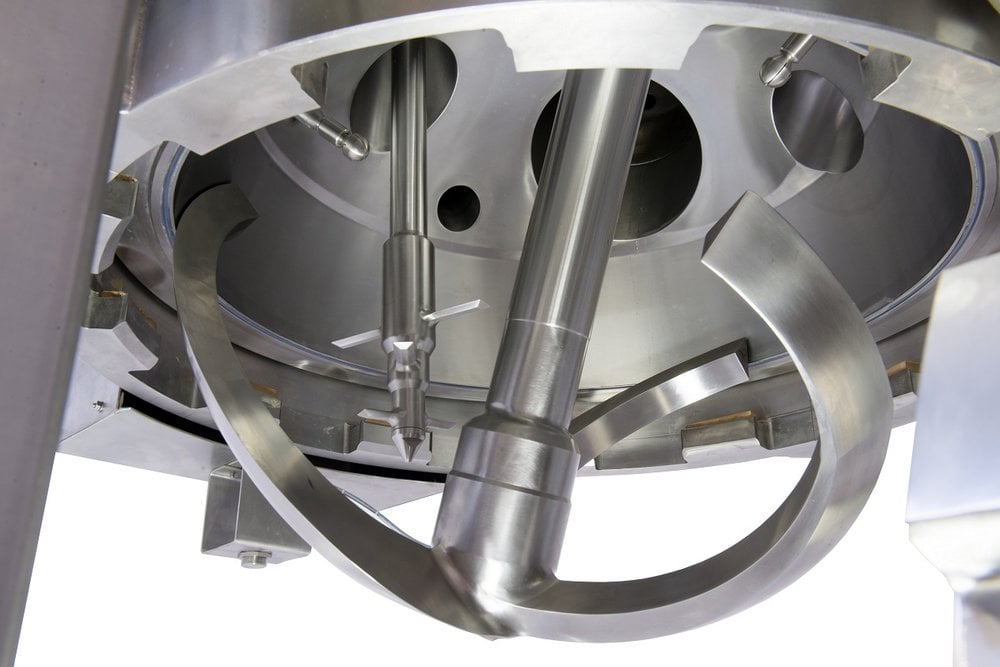
Rosenmund® Spherical Dryer Pilot Scale Machine