www.magazine-industry-usa.com
27
'17
Written on Modified on
Brushing up on wind turbine maintenance techniques
As the world looks towards more sustainable sources of energy generation, many countries are continuing to increase their investment in wind turbine technology, with China and the US leading the globe in the adoption of wind energy. In fact, it is widely expected that the global wind power market will reach 760.35 GW by 2020, as continents such as Europe continue to support wind power initiatives with new legislation to reduce carbon emissions. Whilst wind turbines are undoubtedly in demand, this increase in their adoption presents a number of challenges for windfarm owners and maintenance engineers, as turbines typically have a limited lifespan. Repairs are difficult to carry out, give that the replacement of parts can be costly and any engineering work needs to be carried out up to 100m off the ground. As a solution, many in the industry are focusing on improving the reliability of these devices at all costs. In this article, George Finley and Paul Kling from Morgan Advanced Materials explore some of the most effective maintenance techniques for wind turbine management, taking a look at the consequences of turbine failure.
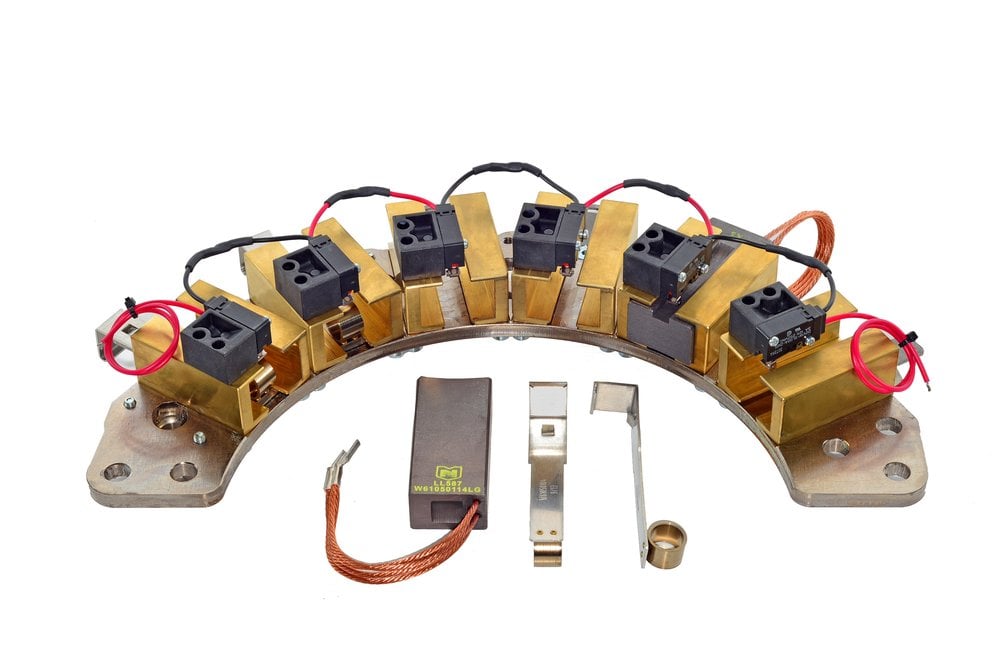
Carbon brush failure – a turbulent issue
Before we explore best practice maintenance for wind turbines, it is important to grasp how component wear and faults can occur. The average life of a carbon brush is difficult to calculate, but it is widely accepted that good carbon brushes will give at least 12 months of consistent service when in operation in a wind turbine. Given the normal wind maintenance schedules and difficulty associated with climbing to replace brushes, shorter life is not acceptable. However, the brush life does largely depend on the individual application, taking into account a number of external factors including the atmosphere and the climate of the operating environment. For example, if a turbine is situated on a cold mountain, the brush will rarely perform to optimum capacity. Likewise, if the turbine is situated on a windfarm where there are frequent bouts of wind, it will generate a lot more power and therefore, the carbon brush will be working harder, exposing it to greater wear and tear, and increasing the likelihood of failure.
Carbon brushes are often forced to perform in very difficult conditions, particularly when a windfarm is very active and over time, this can lead to heavy dusting and damaged slip rings, which are a result of friction chatter, brush instability, improper brush materials (grade), and low spring force. It is also important to remember that all wind turbines are different, with multiple manufacturers often offering different types of turbine. Whilst most are covered by an initial warranty, it is not uncommon for issues with the carbon brush to arise once the warranty expires, particularly in the event that the OEM design presents problems over a period of time. Once a warranty expires, although an affordable component, the cost of maintaining and dusting the brush, together with the inconvenience of having to carry this work out at height, becomes the responsibility of the wind farm owner or operator. When you consider the financial repercussions of having turbines out of service due to a carbon brush failure, you can see why many operators are keen to sweat their assets.
Don’t sweat your assets
When failure occurs, the easiest solution is to simply replace the carbon brush. However, maintenance engineers need to ensure that they always specify the right type of brush, since installing the wrong component can have an even more damaging effect. When an unsuitable grade of brush for the turbine’s operating condition is used, or worn brushes are left unreplaced for too long, they can create additional wear on the slip ring, causing it to degrade or lose shape over time.
This is why Morgan Advanced Materials works very closely with the aftermarket to develop engineered solutions that add further improvements to the OEM design, essentially creating a drop-in solution, which can save operators money over traditional replacement components. While many typical replacement carbon brushes contain a conducive contaminant which can cause flash over time, Morgan has worked closely with turbine operators to develop a solution which has no variability in brush box alignment, eliminating brush instability and facilitating a fast and easy install, doubling the service life of the carbon brush.
Although these simple, drop-in solutions will be required when carbon brushes do eventually fail, operators are advised to get into the habit of carrying out preventative maintenance to their turbines, rather than trying to sweat their assets. When a carbon brush fails, the effect is similar to when a light bulb fades, triggering a series of further component failures within the turbine. Telling signs that a brush is approaching failure are poor overall turbine performance, banging sounds coming from within the turbine, and the smell of smoke or creation of sparks. However, once these signs are realised, it can often be too late to save other components inside the turbine, which may have been rendered faulty as a consequence of a damaged carbon brush, for example the slip ring. The cost of repairing a slip ring can be up to ten times more expensive than the cost of replacing a complete set of carbon brushes. Furthermore, when you consider the labour costs and windfarm downtime caused by a turbine being inactive, the cost can escalate even further. Morgan’s advice is for windfarm operatives to replace the carbon brush at regular intervals to ensure maximum efficiency. Since replacement can be difficult, it is recommended that the entire set of brushes in a turbine be replaced at the same time, for absolute peace of mind and to save time spent having to further make individual replacements.
Special attention should also be given to brush springs, since these can significantly prolong the life of the brush when maintained frequently. It is easy for the brush springs to be overlooked, particularly when you consider that it can be extremely difficult to identify when a spring has become worn. Wear on the springs can cause leakage, triggering the carbon brush to dislodge and destroy the electrics within the slip ring. To avoid this, it is best practice to replace all springs at the same time at regular intervals. When only one spring is replaced in isolation, an inconsistent spring force occurs, which again, can reduce the effectiveness and lifespan of the carbon brush.
There is little doubt about the effectiveness and growing popularity of wind based technology as the world looks towards more environmentally friendly, and sustainable methods for energy generation. However, if windfarms are to be cost effective, operatives need to ensure they are carrying out pro-active maintenance instead of investing time and money into replacement components, which can be a false economy. By regularly replacing carbon brushes and springs, operatives can prolong the life of their slip rings and reduce downtime, as well as time-consuming trips up and down turbines, and the practical concerns associated with working at height. In addition, the selection of appropriate components and frequent maintenance can increase power generation uptime, and help create conditions which allow for the maximum operational efficiency of windfarms.
For further information, please visit: http://www.morganelectricalmaterials.com/wind-brush
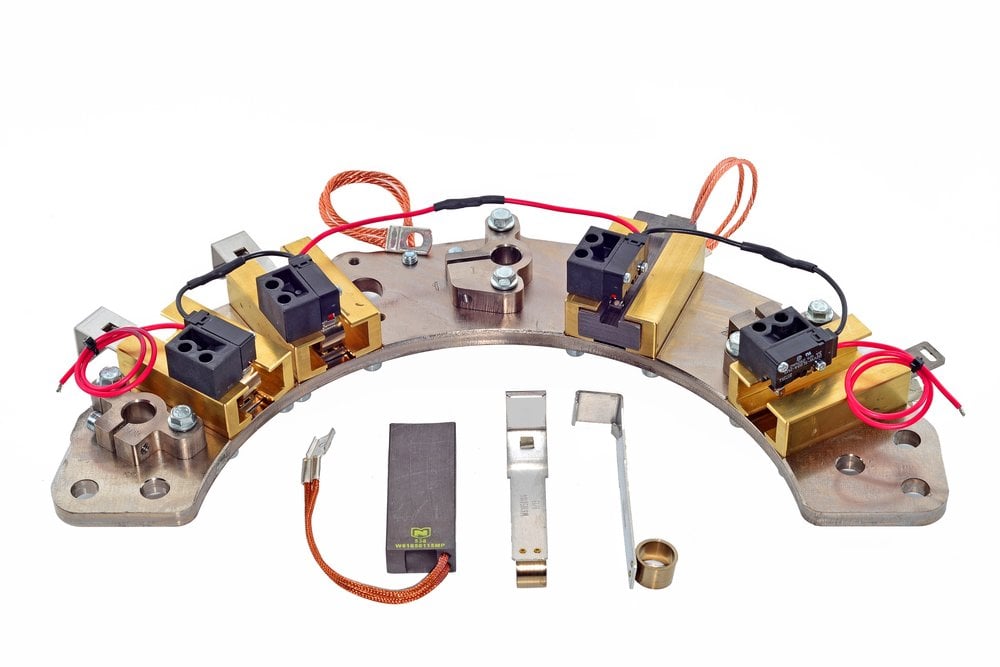