www.magazine-industry-usa.com
25
'17
Written on Modified on
Unidrive M700 VSD helps a large power station maximize cooling tower performance and reduce maintenance costs
The Power Station is now using Control Techniques Unidrive M700 variable speed drives from Emerson to control 22 cooling tower fans across two towers. Replacing a system that was first installed in 1975, the advanced new drive brought many benefits. It means that the fan speeds can be varied to minimize power usage at low unit loads, eliminate wind milling due to a lack of a braking system, minimize freezing potential in winter, mitigate fan vibration without removing from service, and eliminate seasonal blade pitch adjustments required to prevent motor overloads in the winter and low air delivery in the summer. Just the blade pitch adjustment itself resulted in a significant saving in man hours, which the power station estimates to be worth $38,000 per year.
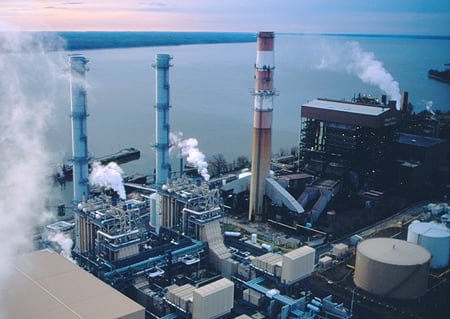
Energy and cost reduction without impacting tower efficiency
• To manage energy usage and cooling capacity meant turning the 200 HP fan starters on and off since they always ran full speed. The capability to vary fan speed and therefore cooling rate for different loads allows all fans to run (best tower efficiency) with much lower energy requirements. The system only moves as much air as is needed to extract heat and results in much less energy consumption.
• To manage vibration on individual fans they had to be shutdown, even when load demand and therefore cooling demand were high. The capability to maintain all fans in operation, with some at reduced speed to manage vibration, provides optimum cooling when needed for unit generation.
• Another issue was the need for manual seasonal fan blade pitch changes, due to differences in air density associated with summer and winter months. That alone demanded close to 480 man hours a year, a significant diversion of maintenance resources from more pressing needs around the plant plus crane rental and safety management required for blade pitch adjustments.
Asset management and protection
• The fans have a 16 foot long fibreglass/metal drive shaft connecting the fan gearbox and motor. With no braking system free wind milling of idle fans was a constant problem that sometimes resulted in bad starting scenarios that caused motor overloads, severe torsion forces on the drive shaft and sometimes gearbox problems. With the new system soft start and prestart braking are inherent in the M700 VSD capabilities. The addition of soft start and fan braking minimized torque peaks that the drive shaft experiences during fan starts and eliminated the wind milling concerns. The motors never see the high current applied by an across the line starter.
• Freezing and thawing are a problem on cooling towers. The existing system required fans to be put in reverse if ice was forming on the sides of the towers in an attempt to thaw the heavy load on the tower intakes. These can have very damaging effects up to and including tower collapse. Properly managed air flow in cold weather using the variable speed capability can eliminate sub-cooling that, in turn, causes ice formation. This eliminates the need to reverse fans except in the most adverse weather conditions.
“We decided to look at variable frequency drive (VFD) solutions and three manufacturers were initially considered,” says Mark Leigh, technical consultant for the power company. “However, Control Techniques [an Emerson company] was the only organization that could meet the very short project delivery times we required. They were also very competent technically in terms of recommending an optimised solution.”
Control Techniques Unidrive M700 AC drives with real-time Ethernet capability were installed in a motor control room at the power station, where it is now used to control 22 cooling tower fans. The drives deliver high performance and flexible control of induction and permanent magnet motors. Most importantly for the station, the new Unidrive M700 has more control of the process.
“In a standard across-the-line starter fan motor, the variables are fan blade pitch and air density with a fixed maximum HP at a fixed speed, which was 1750 rpm in this case,” explains Mr Leigh. “In contrast, the variables in a VFD-controlled fan motor are speed and air density with a fixed maximum HP at a fixed fan blade pitch. It therefore costs nothing in man hours to adjust the speed, as this is done automatically by the VFD based on a 200 HP limit, which is the maximum rating of the motor and starter. We estimate a saving of around four men for three weeks, or about 480 man hours, which equates to approximately $38,000 per annum.”