Bunting Unveils High-Precision Magnetiser for Vacuum Cleaner Components
Bunting’s BMCL5030 magnetiser improves the precision and efficiency of neodymium magnet charging in vacuum cleaner assemblies, offering automated fixture control and advanced cooling for high-volume production.
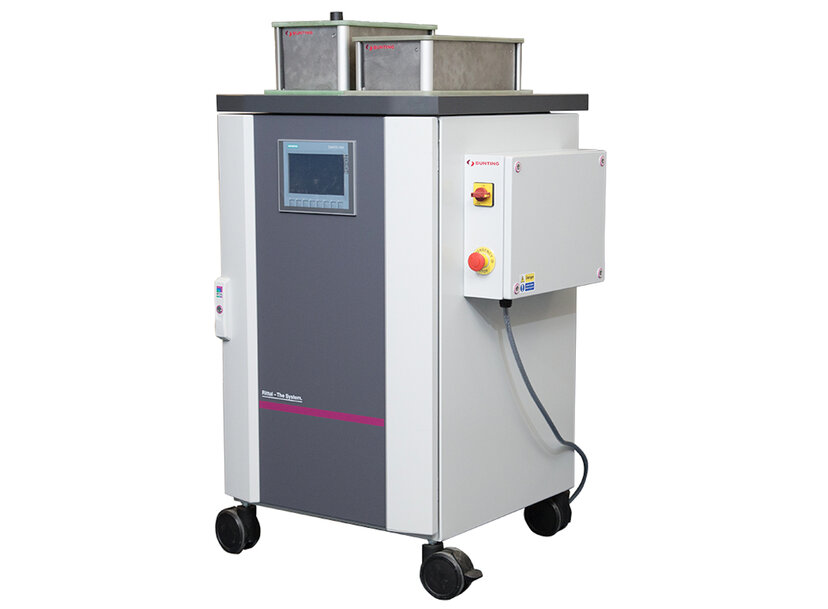
Many everyday electric appliances use high-strength magnets such as neodymium. The nature of the magnet application requires a high degree of magnetic accuracy and control when charging the magnets, especially as many of the magnets are used to interact with sensors to confirm that a component, such as a filter within a vacuum cleaner, is correctly in place.
The BMCL Series is ideally suited for small-part production and laboratories. The mobile magnetiser has a workbench area on top of the unit where the magnetising fixtures are placed for operation and are either hard wired in for permanent installations or connected by quick release plugs for environments where many different fixtures may be used. The standard push button control panel can be fitted with an HMI Interface if preferred.
The standard design features safety interlocks that prevent fixtures from being operated when exceeding specified temperature levels. For applications requiring multiple magnetising fixtures, additional safety interlocks are included.
The process of setting individual magnetising fixture parameters can be automated such that all the operating parameters are stored in the fixture control plug, which once connected to the magnetiser, automatically sets the machine ready for production. This prevents fixtures from being operated at too high a voltage or at a temperature which could damage the magnetising fixture.
The magnetising fixtures provide maximum flexibility, with settings for either peak field, minimum cycle time, or minimum stress (to maximise operational life).
The BMCL magnetisers are designed for magnetising small multipole magnets up to diameters of approximately 50mm, fine pole pitch magnetisation, and more general two-pole magnetisation of most permanent magnet materials including neodymium iron boron and other rare earth magnets.
For the vacuum cleaner project, the BMCL magnetiser is fitted with two magnetising fixtures to enable magnetising of different designs and sizes of magnet components. The operating parameters were for continuous magnetising eight hours per day, six days per week. In production, 60 magnets were charged per hour. To minimise the cycle time. The coil was longer with more surface area to support water pipe cooling adaptations. Although the coil was extended by 25% in length, the unique design ensured that the energy consumption only increased by 10%. The added length provided increased surface area for cooling, which compensated for the extra energy consumption.
“Our magnetiser design flexibility means that we can take a standard model and configure the settings for a wide range of different applications and operating parameters,” explained Matthew Swallow, Bunting’s Technical Product Manager. “Our experience with magnets and magnetising systems is a huge asset when assessing any given application. Often this means working with the client on the final magnet or magnet assembly specification before designing the optimum magnetiser.”
www.bunting-berkhamsted.com