Magnetising 100,000 Loudspeaker Magnets Annually
Bunting’s BMC150/LGC industrial magnetiser enables a European manufacturer to produce over 100,000 ferrite loudspeaker magnets annually, enhancing efficiency and meeting evolving speaker technology requirements.
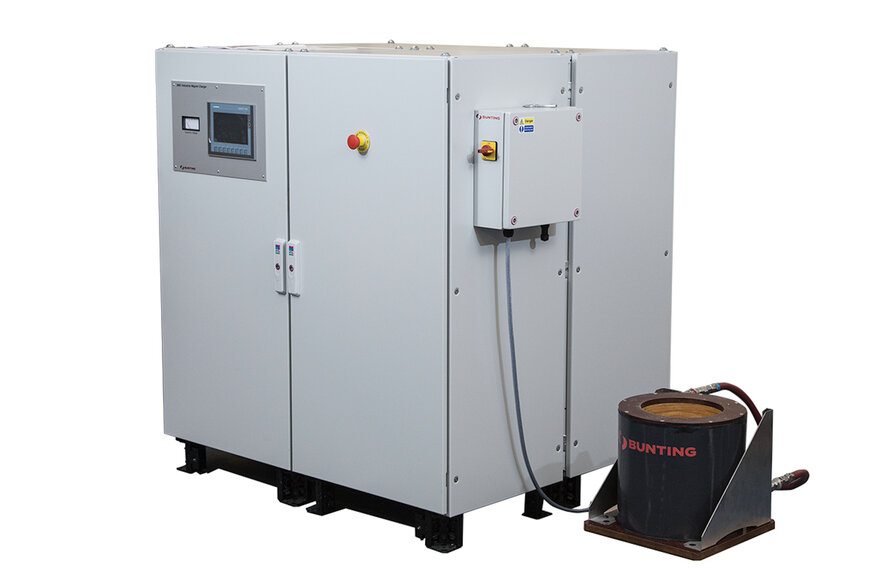
Industrial magnetisers charge and subsequently magnetise permanent magnets and magnet assemblies. Bunting’s specialist industrial magnetisers are commonly bespoke for specific applications, being designed by the in-house engineering team and built on site at the UK-based manufacturing facility.
Permanent magnets are found in the core of a loudspeaker. The fixed polarity permanent magnet interacts with the electromagnet created in the speaker's voice coil. The polarity of the voice coil alternates back and forth when delivering an alternating current electricity feed. As magnets with opposite polarities attract and with the same polarity repel, the attraction and repulsion of the voice coil to the permanent magnet creates the motion of the loudspeaker and the sound waves that are then emitted.
The majority of loudspeakers, especially larger units, use ferrite magnets. Ferrite magnets have low magnetic properties, but are also cost-effective and resist corrosion. Subsequently, for speaker applications, the magnets are relatively large.
With the increasing demand for smaller and more compact speakers with the same output, loudspeaker manufacturers are turning to stronger neodymium iron boron (NdFeB) magnets. The high magnetic strength of Neodymium magnets allows for smaller, lighter speaker designs whilst still producing a powerful magnetic field, which is needed for high sound quality, particularly in compact and portable audio devices.
The industrial magnetiser designed and built for this new loudspeaker manufacturing facility meets the operating criteria of short charging cycle times. In operation, the ferrite magnets are automatically loaded into the magnetising fixture of the magnetiser and then charged within a 20 second cycle time. This design of industrial magnetiser is also capable of magnetising neodymium magnets.
Designing and building this new industrial magnetiser is one of many speaker-related projects. Annually, Bunting builds over 40,000 medical speaker magnets for implanted hearing aids. These flat disc magnets sit under the scalp and magnetically hold the sound processor in place. In a separate project for a high-sensitivity speaker, Bunting configures the magnet setter and magnetiser to magnetise two different permanent magnets, Alnico and samarium cobalt (SmCo), to produce the same magnetic output.
As a supplier of both magnets and industrial magnetisers, Bunting’s engineering team is in a unique position to provide support and advice on any speaker application.
The growth in demand for the model BMC industrial magnetiser has led to Bunting introducing a stocking programme for basic models. These standard designs are then adapted and modified to suit specific applications.
“Bunting’s ability to design and supply industrial magnetisers, magnets and magnet assemblies has led to a growth in sales of magnetisers,” explained Matthew Swallow, Bunting’s Technical Product Manager. “The magnetics experience of our engineering team enables a deeper understanding of the customer’s requirement and a better end solution.”
www.bunting.com