Precision Fits: The Key to Maximizing Bearing Performance
Chris Johnson, managing director of SMB Bearings, highlights the importance of precision fits in ensuring optimal bearing performance and longevity, particularly in high-load and high-precision machinery like robotics and wind turbines.
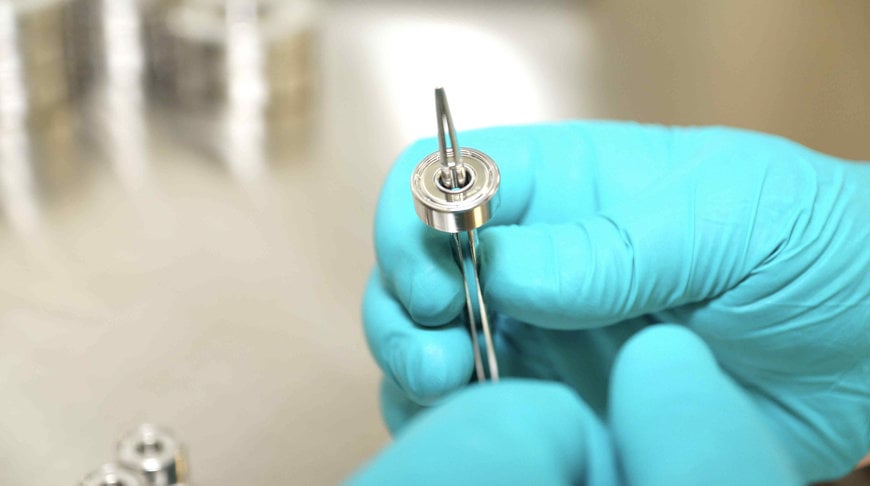
When evaluating bearing performance, material quality and lubrication typically take centre stage, a focus justified by BDS Bearing’s findings that these factors, along with poor fitting, account for up to 70 per cent of bearing failure cases. Despite this, the critical role of precision fits, the exact interplay between a bearing’s inner ring and shaft, or its outer ring and housing, are often overshadowed by other considerations.
At its core, a bearing fit refers to how tightly or loosely the bearing’s rings mate with their respective components. Fits are classified as interference, clearance or transitions and each plays a specific role. For instance, an interference fit secures the bearing in place under heavy loads by creating a tight grip between components, while clearance fits allow slight movement to accommodate thermal expansion or operational misalignments.
Transition fits strike a balance, offering enough security to hold the bearing in place while enabling easier assembly and maintenance. Precision fits, where tolerances are meticulously controlled, ensure optimal load distribution and minimise the risks of slippage, wear or overheating. However, even high-quality bearings can fail prematurely if these fits are misjudged.
For radial ball bearings, the choice of fit can depend on whether the load is rotating or stationary relative to the shaft. For example, when the load rotates relative to the inner ring, as often seen in many industrial applications, an interference fit between the inner ring and shaft is often necessary.
This prevents the inner ring from slipping under load, which can cause wear and vibration. Conversely, when the load is stationary relative to the shaft, a looser fit can suffice. This distinction between rotating and stationary loads highlights the importance of understanding application-specific needs.
Selecting the appropriate fit for a bearing requires a deep understanding of the specific operational demands of the application. Heavy industrial machinery, such as construction equipment or wind turbines, typically benefits from snug interference fits that prevent bearing movement under heavy loads.
In contrast, applications requiring precision, such as robotics or high-speed CNC machines, demand balanced fits to maintain accuracy without distorting the bearing geometry. Engineers must also consider the materials used in shafts and housings. Thermal expansion rates between materials, such as aluminium housings and steel bearings, must be carefully planned to avoid issues like excessive tightness or looseness during operation.
What happens when fits go wrong?
Improper fits can lead to severe consequences. A fit that is too loose may result in the bearing ring slipping against the shaft or housing, a problem known as fretting corrosion. This condition causes excessive vibration and compromises the stability of the entire system.
On the other hand, a fit that is too tight can distort the bearing’s internal geometry, increasing friction and generating heat. This accelerates wear and may even cause failure. As outlined in global bearing manufacturer Timken's bearing damage analysis reference guide, a common result of improper fits is spalling, where material flakes off the bearing surface due to excessive stress. This type of damage often stems from distorted load distribution caused by incorrect interference fits.
For instance, in high-speed spindles used in CNC machines, even minor deviations in fit can produce imbalances, leading to reduced machining accuracy and costly maintenance. Similarly, in heavy-load applications like wind turbines, improper fits can cause misalignments, amplifying stress on critical components and significantly reducing both efficiency and lifespan.
Industries ranging from aerospace to renewable energy face similar challenges when it comes to precision fits. Aircraft engines, for example, must ensure safety and prevent costly delays.
In the automotive industry, the rise of electric vehicles (EVs) presents new challenges. Bearings in EV drivetrains must handle high speeds, variable loads and elevated temperatures while maintaining quiet operation and extended service life. Selecting fits tailored to these demands is crucial for ensuring both performance and reliability.
It is also important to consider bearing temperature differences during operation, as this can impact the effectiveness of a chosen fit. Bearings that run significantly hotter than surrounding components can expand more, effectively tightening the fit during use. In these situations, a fit that seems appropriate at room temperature could become overly tight, leading to increased wear and reduced performance.
Thermal expansion data and operational temperature ranges should be factored into the fit selection process to avoid such issues.
Determining the fit
Determining the most suitable fit begins with evaluating key operational factors. Load and speed are crucial considerations. High-speed applications often require tighter tolerances to minimise vibration and prevent slippage, whereas heavy-load machinery relies on interference fits to secure components and withstand significant forces.
Engineers also need to consider the operating environment. Harsh conditions, such as exposure to extreme temperatures or contaminants, may necessitate precise adjustments to maintain sealing integrity and protect against wear.
Thermal expansion is another critical factor. Material expansion rates must align to avoid performance issues caused by mismatched thermal changes. For example, in applications involving steel bearings housed in aluminium, the higher expansion rate of aluminium must be accounted for to prevent excessive looseness during operation. Similarly, the operating temperature range of the machinery should guide the decision about fits to ensure consistent performance over time.
Maintenance considerations also play a role in fit selection. Bearings that require frequent removal for servicing or replacement benefit from transition fits, which facilitate disassembly without sacrificing operational stability. By factoring in these maintenance needs during the design phase, engineers can achieve a balance between ease of access and reliable performance.
Despite its importance, fit selection often takes a backseat to other design considerations. This oversight may stem from a lack of awareness about the impact of fits or an overreliance on standard configurations that fail to meet the unique needs of specific applications.
Industry standards and guidelines, such as those from The International Organization for Standardisation (ISO), offer valuable frameworks but must be applied judiciously to account for application-specific requirements. Addressing this issue require a proactive approach. By consulting a bearing specialist early in the design phase, engineers can achieve optimal fits that prolong bearing life, reduce maintenance costs and enhance equipment performance.
www.smbbearings.com