www.magazine-industry-usa.com
11
'23
Written on Modified on
LASERS JOIN LIGHTWEIGHT SANDWICH STRUCTURES
Fraunhofer IWS has developed a process to produce lightweight panels and profiles significantly faster as well as cheaper than with conventional methods.
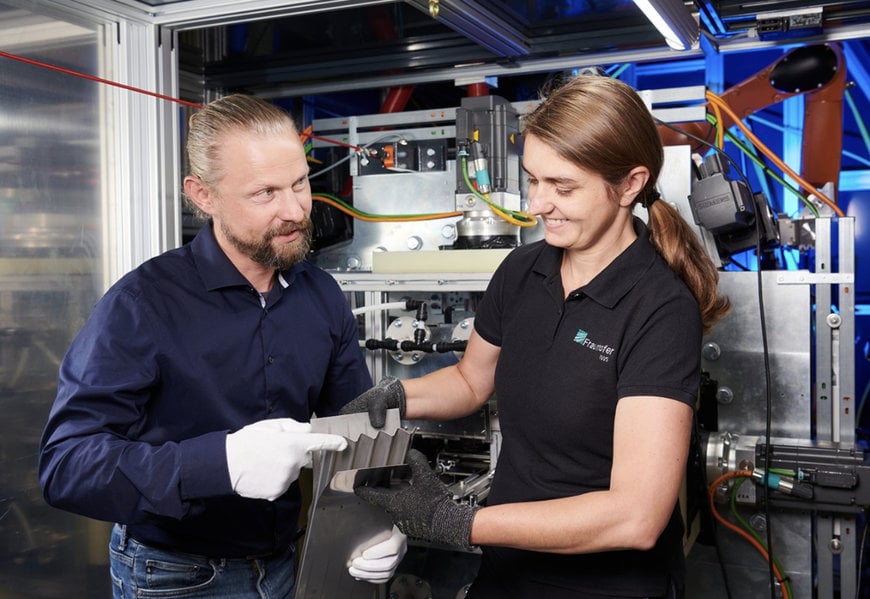
The new, laser-based “sandwich plating” offers a lot of technological, economic as well as ecological potential for industry: “With this technology, lightweight panels and profiles can be produced significantly faster and more cost-efficiently than with conventional methods,” emphasizes Andrea Berger, researcher at Fraunhofer IWS. “In addition, the new process eliminates the need for adhesives and other additional materials. This facilitates the recycling of the lightweight structures produced with it.”
Instead of centimeter-thick heavy steel plates, many lightweight builders often use sandwich plates. Despite their significantly lower weight compared with solid steel, these are strong enough for partition walls and ceilings in vehicles, aircraft or halls. These sandwich panels and profiles consist of honeycomb, trapezoidal, web or spherical hollow chamber structures. Typical starting materials are thin steel, aluminum, plastics or other materials. On these inner structures, manufacturers weld or glue thin sheets on both sides.
Classical extrusion reaches its limits
A challenge that a large wagon manufacturing company approached Fraunhofer IWS with started the new laser rolling process: The company was already using lightweight aluminum profiles for its vehicle technology. However, the applied extrusion process did not allow for arbitrarily thin inner webs. Approximately 1.5 millimeters constituted the technological lower limit. This was and still is opposed by the desire to save as much material and weight as possible or to use filigree internal structures.
Fraunhofer IWS researchers solved this dilemma with a laser welding rolling mill. Using this system, they guide a flexible core layer of very light internal structures between two rollers, over which a cover sheet rolls at both top and bottom. Scanner-controlled lasers aim obliquely from both sides precisely into the thin gap between the core layer and the cover sheet. There they heat the metal surfaces with pinpoint accuracy. Depending on the sheet material selected, local temperatures of between 660 and over 1400 degrees are generated. The rolls then press the slightly melted surfaces of core layer and cover sheet together so firmly that they bond permanently.
Laser process cuts energy consumption and facilitates recycling
Such particularly lightweight sheets can be produced in a single pass using a rolling process. Compared with conventional methods such as extrusion at high temperatures, laser welding saves a significant amount of energy because the energy-rich light only has to melt the metal surfaces locally to a wafer-thin thickness. It also suits low-cost mass production. Even the laboratory prototype achieves a high production speed. Developed to industrial scale, such systems could produce more than ten meters of lightweight sheet per minute, estimates Andrea Berger. In addition, such machines can be quickly converted to new profile or sheet structures. Extrusion presses, on the other hand, require a different tool for each application when the customer orders a new plate model.
Laser sandwich plating can also be used to produce stable structures that are only a few tenths of a millimeter thick. This alleviates the mentioned dilemma in rail car manufacturing, for example. Since laser roll cladding enables inexpensive lightweight construction solutions made of pure, heat-resistant steel, such panels can also be installed in places traditionally off-limits to many conventional lightweight structures for fire protection reasons – for example in certain areas of shipbuilding. Such wider use of lightweight construction in turn reduces material consumption in supply industry, can lower the weight of vehicles, aircraft and ships, and thus save fossil fuels or electricity. Another ecological benefit arises at the end of the component life cycle: laser-joined sandwich panels contain neither adhesives nor solder or other foreign materials requiring laborious separation again later in recycling plants.
Prospective applications in shipbuilding, hall construction and vehicle manufacturing
Marko Seifert, head of the Heat Treatment and Cladding department at Fraunhofer IWS, sees potential early adopters of the new process in subcontractors for shipyards and vehicle manufacturers, among others. Initial application scenarios could include lightweight staircases or ship partitions, for example, in which power cables and other media can be laid invisibly thanks to the hollow inner structures of the plates. The new technology could also quickly become established for truck trailers and hall construction. As for the next steps, the Fraunhofer researchers are looking for partners to transfer the idea into practical applications.
www.fraunhofer.com