www.magazine-industry-usa.com
04
'23
Written on Modified on
FRAUNHOFER INTRODUCES ECONOMICAL AND RESOURCE-SAVING GREEN HYDROGEN
Large quantities of hydrogen will be needed to ensure a successful energy transition. As part of the HighHy project, an international team of researchers from Germany and New Zealand is working on improving the efficiency of the emerging AEM electrolysis technology to produce green hydrogen.
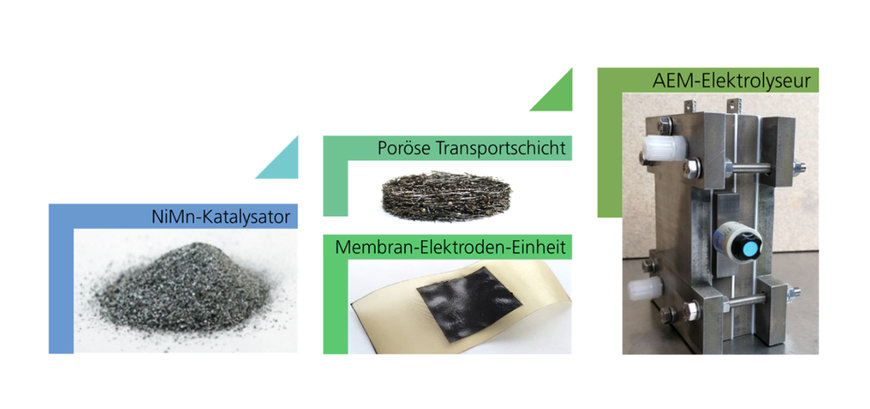
What will we use to get around in the future? How will we operate our industrial plants? Or temporarily store energy for longer periods of time? Hydrogen could be the answer to many of the challenges that come with the energy transition. The lightest element in the periodic table is an all-rounder and can be used in road transport, industry and heat supply. The fact that hydrogen is so versatile means that large quantities of it will probably be needed in the future. However, mass production is still fraught with challenges — many of which the HighHy project team intends to address by developing catalysts for highly efficient and cost-effective hydrogen production.
Producing hydrogen with common electrolysis processes
Hydrogen can be produced through electrolysis on an industrial scale. Electric energy is used to split water molecules into hydrogen and oxygen when immersed in water mixed with a conducting salt — the so-called electrolyte. The energy is absorbed and stored in hydrogen as chemical bonds. This gas is therefore an attractive means of long-term energy storage for energy generated, for example, by wind turbines or solar panels that cannot be directly fed into the grid. Hydrogen generated by renewable energy sources is known as “green”.
There are three main electrolysis processes currently in use on a larger scale. The most technically relevant and historically widespread is alkaline electrolysis (AEL), which involves adding potassium hydroxide to water, for example. A drawback of this process is the limited lower partial load range, i.e., when using a fluctuating power supply, the full range of power cannot be drawn as an electrical load. In the case of electrolysis involving a proton exchange membrane electrolyzer (PEM-EL), hydrogen ions move in a strongly acidic environment through a gas-tight membrane in direct contact with the electrodes (called a membrane electrode assembly, or MEA). This approach yields a high power density and very dynamic load behavior while still retaining a high degree of gas purity. However, the electrodes require the use of rare and expensive noble metals such as iridium to withstand the highly corrosive environment, as well as expensive membranes.
HighHy project: catalysts for highly efficient AEM electrolysis
Electrolysis using anion exchange membranes (AEM) is a relatively new approach. It combines the advantages of AEL, such as high long-term stability and the use of affordable and widely available metals, with those of PEM-EL, i.e. higher performance, adaptability to different loads, and gas purity. AEM electrolysis has not yet been successful in industrial applications because the oxygen evolution reaction (OER) involved in the process is too slow when using non-precious metals. Therefore, the necessary cell voltage for water electrolysis is very high for the desired current densities and as a result, the energy required for hydrogen production is very high.
This is the challenge that the HighHy project is addressing: The German-New Zealand collaboration, which is funded under the “Green Hydrogen Research Collaboration with New Zealand” by the German Federal Ministry of Education and Research (BMBF), is working to develop OER catalysts and, subsequently, high-efficiency AEM electrolyzers. “Together with three New Zealand universities and the University of Bayreuth, we are striving to find the ideal composition for the required catalysts,” says Dr. Christian Bernäcker, head of the Electrochemical Technology working group at Fraunhofer IFAM, summarizing the aim of the project.
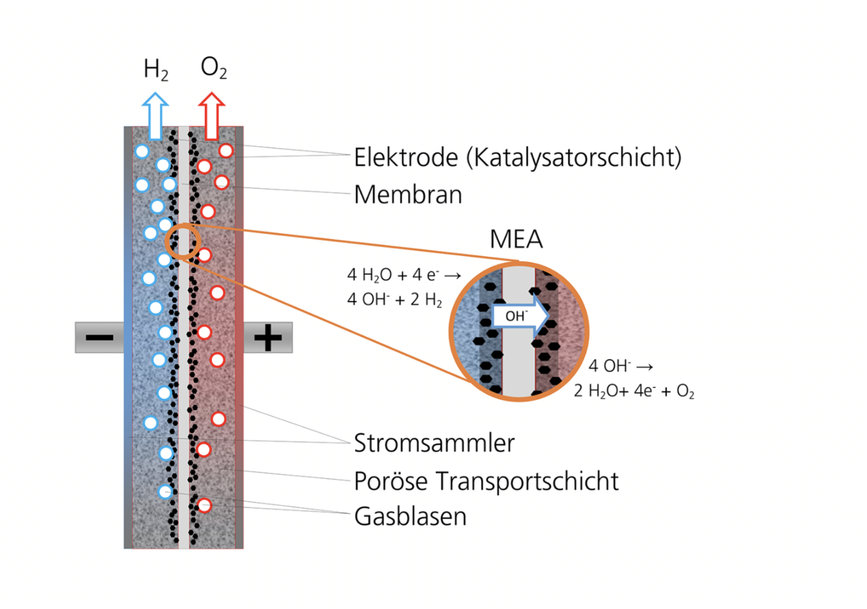
Available and affordable: nickel and manganese catalyst compound
The HighHy project researchers intend to use an innovative nickel-manganese compound as an OER catalyst to produce green hydrogen on an industrial scale via AEM electrolysis. This compound boasts crucial advantages: Both metals are inexpensive and readily available as raw materials. They also feature promising chemical activity. The HighHy teams are working simultaneously on potential solutions with the goal of developing an ideal compound for use in industry. Dr. Clemens Kubeil, research scientist in the Hydrogen Technology department at Fraunhofer IFAM in Dresden, where he is responsible for the project, explains their approach: “The complementary approach is quite special: The project partners are testing many different synthesis methods, compositions, surface structures and material sizes to coat the catalysts. Ultimately, the best solution will be selected and subjected to extensive testing with a demonstrator created in New Zealand.”
The Fraunhofer IFAM team is contributing its expertise in powder metallurgical strategies to this catalyst development: Not only is the electrochemical activity of the catalyst important, but the electrical contact between the electrodes and the electrolyte flow must also be optimized, allowing the gas bubbles to be guided away from the electrode in the best manner possible. Know-how regarding porous structures, like those created when nickel-manganese powder is used for coatings, is a key factor here. The researchers hope that the new catalysts will reduce the amount of electrical energy required for oxygen generation and thereby improve the efficiency of AEM electrolysis.
Price, flexibility, hydrogen purity: high potential of AEM electrolysis
There is great potential for AEM electrolysis suitable for use in industry: The EU targets for electrolysis energy use in the new process are set at approximately 48 kilowatt-hours per kilogram of hydrogen produced by 2030. This means that AEM-EL would be capable of achieving around 80 percent efficiency, i.e., similar values to the previously established AEL and PEM-EL processes, while offering significantly greater flexibility in terms of loads driven and places of use, as well as significantly lower material costs. “The price target for the acquisition costs of the AEM electrolysis system, when calculated down to the hydrogen produced, is around 300 euros per installed kilowatt, whereas the PEM-EL comes in at around 500 euros. Even for classic alkaline electrolysis, the target is currently still 400 euros. This means that AEM-EL is the only serious electrolysis solution in terms of price,” concludes Clemens Kubeil. “The fact that it can be produced under high pressures due to the gas-tight membrane and the lower-concentration electrolyte and asymmetric electrolyte flow is yet another advantage. This results in the production of very pure and compressed hydrogen that is easier to feed in. In turn, this would allow systems to start up and shut down faster and operate at partial load, which is very interesting when bringing an application to the fluctuating market.”
www.fraunhofer.com