www.magazine-industry-usa.com
26
'22
Written on Modified on
SIEMENS: THE PATH TOWARDS DIGITALIZATION AND THE FUTURE
Big data, Industry 4.0, IIOT, Edge Technology and the Cloud are all terms we know. Whether you’re a machine tool builder, a job shop or contract manufacturer, you’re thinking about digitalization and the best way to get started.
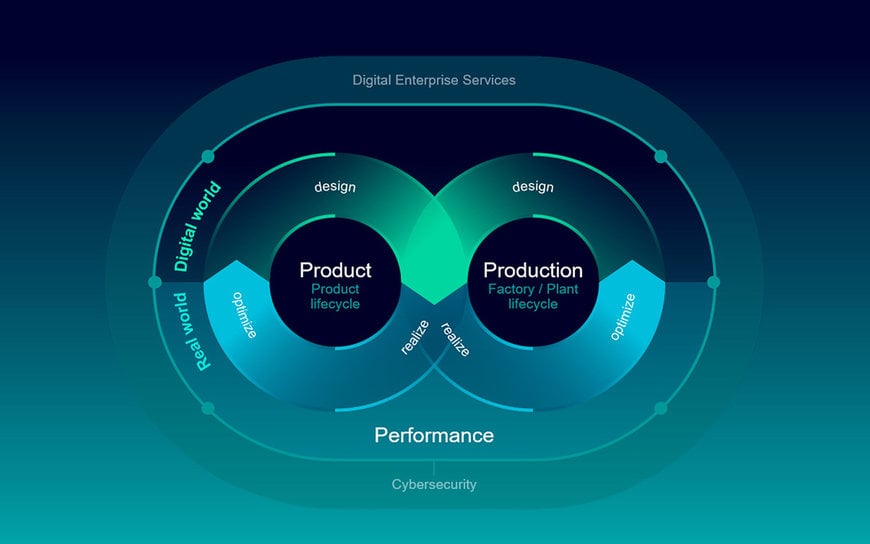
For the machine builder, it’s about managing big data from the machine, reducing time-to-market and using the newest technology to create smart machines. These are cognitive computing systems, meaning they can make decisions and solve problems without the help of a human. This is where artificial intelligence (AI) enters the equation, as the machine learns from what it does. In addition, machines must be ready to engage the Internet of Things (IOT) to be successful in the current market. Machine builders still sell on the features and benefits of their machines, but this isn’t the only way to distinguish themselves from the competition.
The digital twin concept in machine development allows simulation of a machine tool not only in its design, but also in its physical performance, before the machine is even started physically.
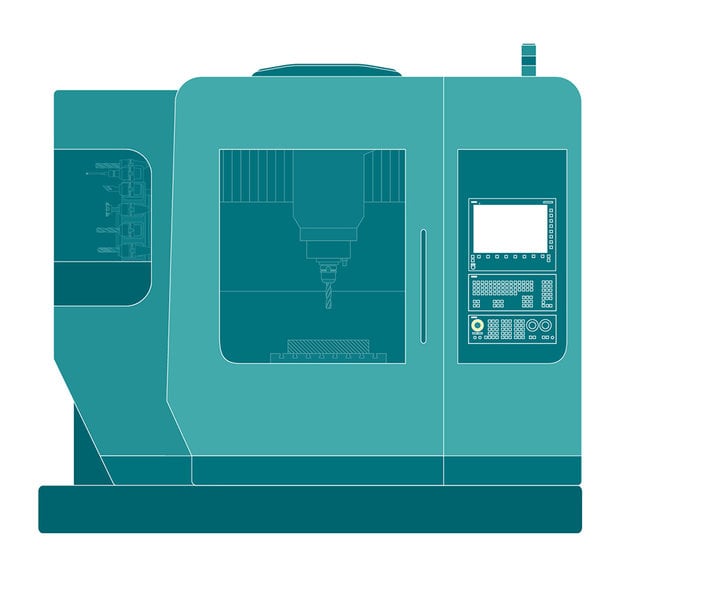
With the digital twin, every condition on the machine is simulated in real-time, with feedback to the design loop. That way, engineers don’t need to waste time on the shopfloor or in a test center as they’ve done previously, with the “trial and error” method. The science has developed, so the build process must likewise.
CNC machine users need their machines to be smart, as well — communicating with each other and the control center in their shop or in a large production facility. Thinking you can’t implement digitalization because you’re a small machine shop? Think again. Key performance indicators (KPIs) can be established and achieved sooner in terms of production, machine run time, maintenance and even energy use. For CNC users, the digital twin enables a machine shop to be IOT-ready. The higher-end software permits real-time adjustment in-process, everything from cycle time to tool tip position or tool magazine loading for the next jobs, to facilitate both faster startup and precision workflow.
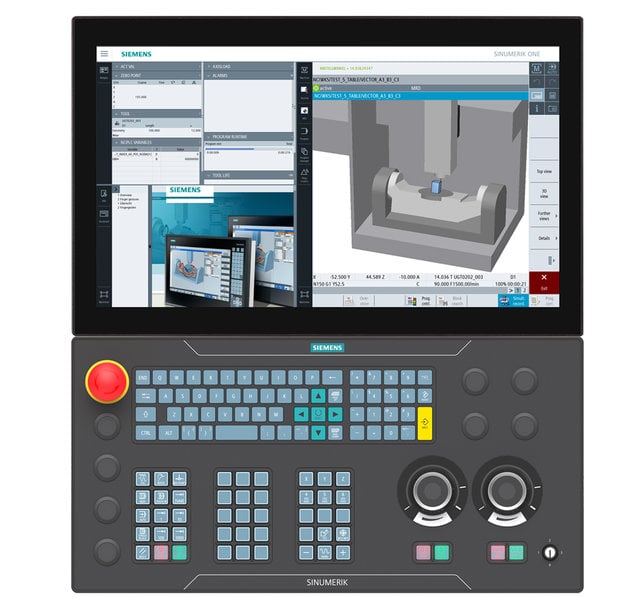
This can be achieved with a competent digital team that is both in-tune with the current technology and how to implement it in a particular environment. If needed, take time to find a system integrator in your area (we have a nationwide network of solution partners) that can provide you with relevant technical and industry knowledge. This is vital to your success.
Our newest digital-native CNC, SINUMERIK ONE, for example, will open the next chapter in the machine tool world’s journey towards digitalization. It features the latest power and software options to allow expansion, as the job volume increases, or the complexity of the work increases for you.
Virtually, it offers the machine builder and end-user total flexibility to move from the CAD to the CAM to the CNC machining steps, then onto the virtual shopfloor and into a virtual production, all before the first cut is made on the machine.
As ransomware attacks have become common in the industrial environment, the issue of cybersecurity has taken on new importance. Preventing any attack means taking into consideration several issues. One is the integrity of the network. The other is the effect of the wireless network in the plant and externally. The third, and most important, is how effective the defense is. Like a football game, one wrong move from a player can adversely impact the game plan. Furthermore, there must be several layers of specific security, so that setup, operation and programming, maintenance and plant operations/control personnel all have different defined levels of access to machines and data. This is often a time-consuming, but very worthwhile endeavor.
If we look towards the future, what we see is digitalization at essentially every level of your factory. This would include robotic handling and the transfer of materials to the next machine. The “factory of the future” wouldn’t be without people, however. Rather, personnel will take on higher level tasks that don’t involve machining. Cobots and CNC will work with a human or directly with the machine intelligently.
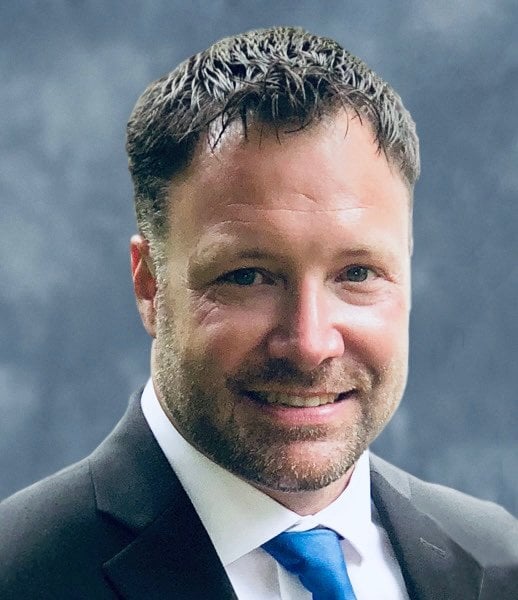
Brian McMinn is the head of the Machine Tool Business at Siemens Industry, Inc. He is an electrical engineer with 25 years in the motion control and drives business. He has a passion for the emerging technologies in machine automation and control.
Digitalization is here to stay, so get started today!
www.siemens.com