www.magazine-industry-usa.com
01
'22
Written on Modified on
Case Study: AI-Powered Failure Analysis and Inspection System Finds Issues Faster
.
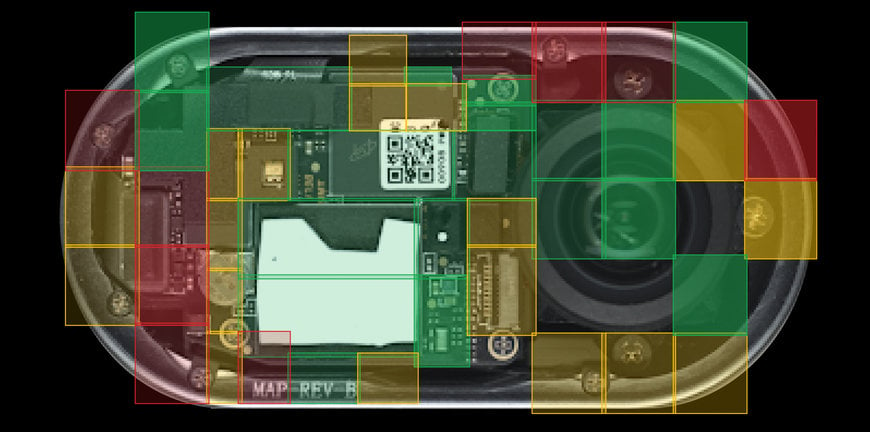
Founded by former Apple engineers, Instrumental is a manufacturing optimization platform that proactively identifies issues in real-time as they appear on the assembly line. Their platform provides engineers and manufacturing teams with the complete data record they need to quickly discover new issues, complete failure analysis, communicate concisely with the factory team, and make process improvements in production. Instrumental helps remote engineering teams discover correlations between multiple data sets from the line, including functional tests and visual records, in order to find the root cause behind failures.
Using 20 MP Blackfly S cameras, Instrumental imaging stations capture high levels of detail required for inspecting small electronic micro assemblies where very small errors can lead to failures (among several other applications).
Unique features and ease of integration provided by Spinnaker SDK combined with our renowned 20 MP Blackfly S USB3 cameras were ideal for Instrumental’s manufacturing optimization platform. The system aggregates images and functional test data from throughout the supply chain, leveraging artificial intelligence to automatically rank potential root causes, enabling customers to accelerate issue resolution, gain faster yield, and improve quality. Read along to learn more and contact a specialist about Instrumental’s inspection solutions and Teledyne FLIR machine vision cameras.
• How Instrumental’s inspection platform delivers automated defect detection
• Platform features that combine root cause analysis and reporting
• Benefits of secure product data management, and native collaboration tools
• Why Instrumental chose Teledyne FLIR’s 20 MP Rolling Shutter CMOS
• Unique features, ease of use and integration enabled by Spinnaker SDK
• How Teledyne FLIR enables Instrumental an easily customizable setup
View Case study