Daring to step into the world of additive manufacturing
Traditionally, Smithstown offers a range of production methods, including milling, rotating, sanding and eroding. The aim was to expand the repertoire to include 3D printing and to set up an additive centre within a recently erected extension. By doing so, the company hopes to provide its medical technology customers with additive solutions, particularly within the R&D sector.
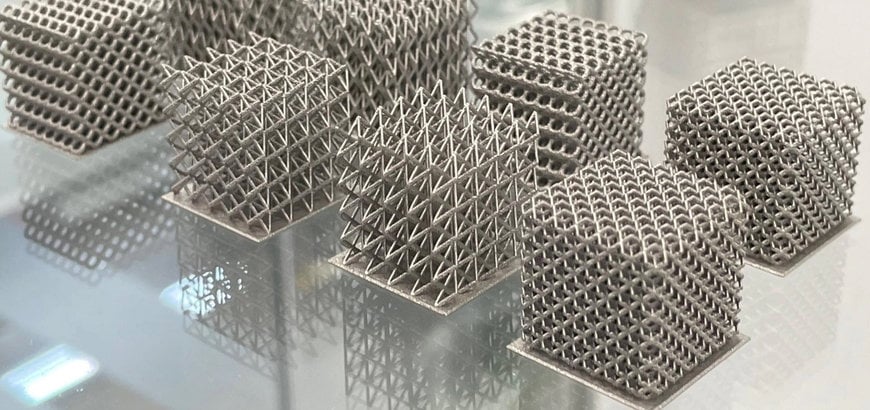
Smithstown Light Engineering
Smithstown Light Engineering was founded in 1974 and started with a team of four qualified toolmakers. The company specialised in the production of medical devices in the early 1990s. The company is certified in accordance with ISO9001 (quality), ISO13485 (medical devices) and ISO14001 (environment), among others. Today, Smithstown concentrates on the provision of precision-machined medical devices, orthopaedic instruments and implants at three sites in Ireland and Poland, typically for the cardiovascular and hip and knee joint areas.
INDUSTRY - Medical technology
NUMBER OF EMPLOYEES - 141
LOCATION
Shannon, Ireland
TRUMPF PRODUCTS
- TruPrint 2000 TruPrint Monitoring AM Consulting
- APPLICATIONS
- Additive manufacturing
Challenges
It can take years in the medical industry for a product to go from the design and test phase through to validated production. The company wanted to accelerate this process and to produce prototypes as well as samples from 17-4 stainless steel in additive processes for a variety of customers. There was special emphasis on the surface quality and level of detail.
Some of our competitors have 3D printers as well, but the TruPrint 2000 definitely gives us the advantage.
KEVIN KELLY
MANUFACTURING ENGINEER
Solutions
Smithstown considered several potential 3D printers before designing their own benchmark and then sending it to possible suppliers. “The quality of the benchmark produced on the TruPrint 2000 caught our eye. Furthermore, the machine‘s volume was perfect for our requirements and the price was competitive,” says Gerard King, Managing Director at Smithstown. The additive process is ideal for Smithstown‘s medical products due to the complex geometries. “Without 3D printing, several processes taking several hours would be required. Additive manufacturing also has the potential for customised adaptations which has obvious advantages for products such as implants.”
Implementation
Since the installation of the TruPrint 2000 at Smithstown, prototypes and samples have been produced constantly from 17-4 stainless steel for medical technology customers. With its small 55-µm laser beam diameter, the TruPrint 2000 provides a high-quality printing result which impresses with its surface quality and level of detail. Two TRUMPF 300 W fiber lasers ensure high productivity across the entire cylindrical build volume of 200 mm (diameter) by 200 mm (height). Deviations in the laser melting process can be detected early via sensors with Melt Pool Monitoring, as critical areas of the component can be visualised. “We are very satisfied with the quality and speed of the TruPrint 2000. We enjoy the best possible support from TRUMPF; they are always ready to hear about our needs,” explains Gerard King.
Forecast
“As soon as we reach the production phase for current projects, it is a real possibility that we will need several 3D printers so that we can provide machines for individual materials,” says Kevin Kelly, Manufacturing Engineer at Smithstown. The company has recently secured several new projects, increasing the need for new employees. In addition, Smithstown‘s future business strategy includes plans to increasingly concentrate on high-volume precision components.The latest manufacturing technologies are a continuous growth driver in this future-oriented company.
www.trumpf.com