www.magazine-industry-usa.com
04
'20
Written on Modified on
A milestone in hybrid production with laser technology
KUKA has been working with the Fraunhofer Institute for Laser Technology (ILT) and other industrial partners on a joint project of the German Federal Ministry of Education and Research (BMBF) and KIT (Karlsruhe) for integrating hybrid LMD technology into the production chain. The process used is laser metal deposition (LMD), popularly referred to as “3D printing”. KUKA robots form the basis of the system.
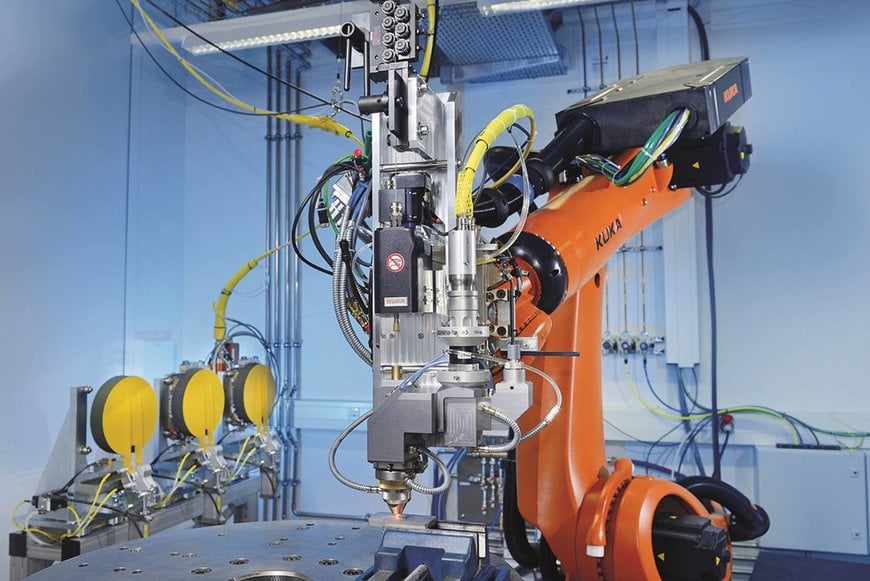
Conventional, subtractive technologies are still the standard in production halls. Forgings and castings with a complex shape often require extensive machining. In the manufacture of high-performance and lightweight components – such as those in the aircraft industry – up to 90 percent of the raw material is still removed. In additive manufacturing, by contrast, the components are built up layer by layer. This not only saves resources and avoids production waste, but also makes manufacturing extremely flexible.
Hybrid additive manufacturing as a practical alternative
Hybrid additive manufacturing is a practical alternative to conventional processes. Blanks are produced conventionally, for example by forging or casting. Additional geometries are then applied to them additively, thereby creating individualized components – within the framework of the ProLMD project sponsored by the German Federal Ministry of Education and Research (BMBF), for example, this is done using LMD laser material deposition. The advantage compared to other additive techniques is the high build-up rate.
This allows the efficient manufacture of locally reinforced structural components for aircraft or highly functional components for turbines, for instance. Up to now, however, the high costs and demanding machining conditions have often prevented comprehensive use of this technology.
"As materials have to be protected from oxidation during laser material deposition and the complete system is located in a shielding gas atmosphere, there are often still limits to the size of the components that can be machined."
Günter Neumann, Head of KUKA Business Unit Laser Applications
Hybrid manufacturing of large components on the basis of KUKA LMD technology
The goal of the ProLMD project is to develop robust and efficient process and system equipment for the application of LMD technology in the manufacture of large components. This system is designed to handle state-of-the-art production techniques and satisfy the high safety requirements in sectors such as the aerospace industry. The standardized system technology based on KUKA robots offers cost advantages. Thanks to the use of a fiber-guided system, the robot remains virtually unrestricted in its workspace. This makes it possible to respond flexibly to component geometry and size – even with small batch sizes.
The advantages of LMD laser metal deposition: shorter production time, lower costs
In the coming years, the results from ProLMD are to be introduced into the production processes of the participating project partners MTU, Airbus and Daimler. “We are anticipating a milestone in the industrial implementation of hybrid manufacturing processes,” says Lars Ott, Project Manager for ProLMD at KUKA. The experts expect this technology to reduce production time by 50 percent and to cut costs by 20 to 30 percent. In addition, implementation can make a lasting contribution to resource efficiency in manufacturing.
In the project, KUKA is able to draw on the many years of experience of the experts at the Aachen location in the field of robot-based laser technology. KUKA designed and implemented two identical production lines for hybrid additive manufacturing in this project. They are already in use in the company’s own production shops at the Würselen site near Aachen and at the nearby Fraunhofer Institute. “In the long term, we want to upgrade the process for series production,” explains Günter Neumann.
www.kuka.com