www.magazine-industry-usa.com
05
'20
Written on Modified on
Safran inaugurates a new “Factory 4.0” to make primary mirror segments for the Extremely Large Telescope
Martin Sion, Chief Executive Officer of Safran Electronics & Defense, and Xavier Barcons, Director General of the European Southern Observatory (ESO), today inaugurated Safran's new production unit at the company's Saint-Benoît plant near Poitiers in central France, which will make the primary mirror segments for Europe's Extremely Large Telescope (ELT).
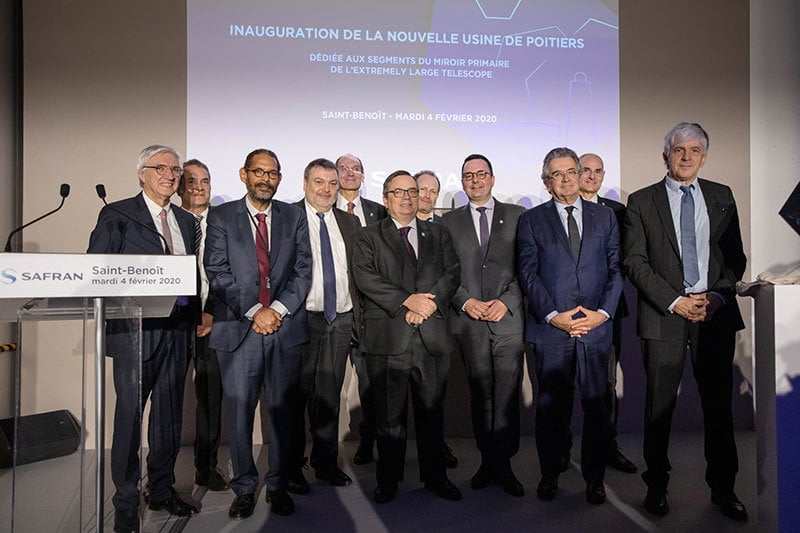
Built with support from the Nouvelle Aquitaine region, this new facility will produce segments for the primary mirror on the ELT, which is operated by ESO and will be the most powerful telescope in the world when it enters service. Safran Reosc, a subsidiary of Safran Electronics & Defense, has won contracts for all mirrors on this telescope.
The ELT is being built on top of the Cerro Armazones mountain in the Atacama Desert region of northern Chile, at an altitude of 3,046 meters (about 10,000 feet). Comprising five mirrors, M1, M2, M3, M4 and M5, it will drive significant progress in astronomy by offering unprecedented observation capability. The ELT is scheduled to start operation – "first light" – in 2025.
Its primary mirror, which will collect light for the telescope, is formed from 798 segments and has a diameter of 39 meters (128 feet). Safran Electronics & Defense is constructing its new production unit to make these segments by calling on the complementary areas of technological expertise offered by Safran Reosc and its legacy production plant, a long-standing specialist in optics and optronics (electro-optical equipment).
The new 5,000 square meter (54,000 square foot) facility is dedicated to the polishing of the segments for the M1 mirror, mounting them on their cradle and testing them. This new production line features several robots and automated and interconnected production cells, to ensure fast, precise and dependable operations, for polishing of blanks. Digital data from the production and testing systems allows the production process to be controlled in real time and make sure it is as efficient as possible. Operators have been trained to use this new machinery. A total of 931 segments will be produced (798 for the telescope + 133 spares) by polishing and then mounting them on substrates, to an accuracy of less than a few nanometers – in other words, if each segment were as large as France, a surface defect smaller than a ladybug!
Right from its launch, this new production unit was accompanied by a digital twin, dubbed BIM (Building Information Modeling). Using 3D modeling of the facility, engineers could study the best location for machinery and optimize workflows to meet the challenge of rolling out one complete segment per day over a period of three years.
"The ELT will be the largest telescope of its kind ever built. It will allow us to tackle many unanswered questions about our Universe and give us clues about where life might exist outside our Solar System. This is a gigantic technical challenge, where European industry has a very central role to play", said Xavier Barcons, Director General of ESO.
"The inauguration of this advanced facility is a major step forward, giving us a world-class production tool," added Martin Sion, CEO of Safran Electronics & Defense. "The automated and robotized production line will mark a disruptive advance in terms of production competitiveness and agility, and will help ensure the complete satisfaction of our customer, ESO."
www.safran-group.com