www.magazine-industry-usa.com
07
'19
Written on Modified on
Considerations for computer vision quality control in manufacturing
Computer vision systems are installed in manufacturing plants to assist with a wide variety of industrial quality assurance and control processes, and to a lesser extent in applications of process control.
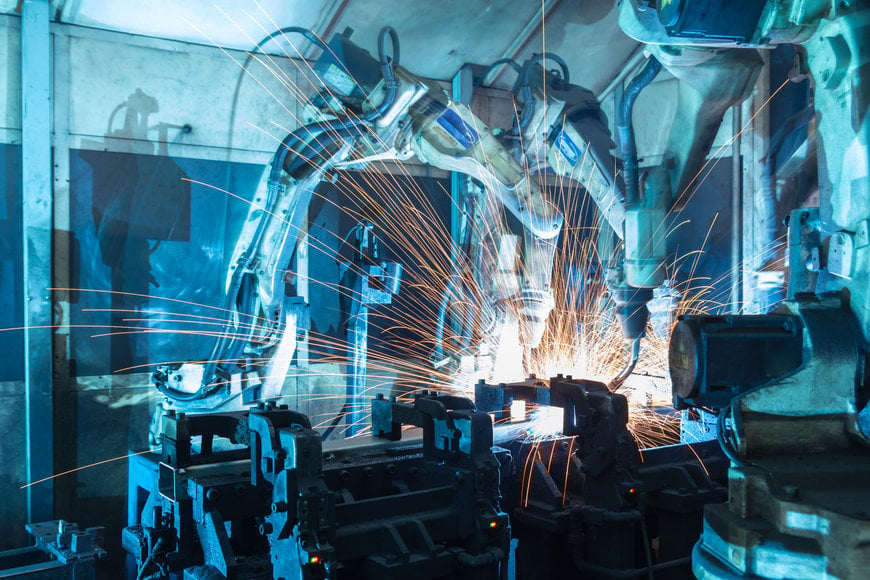
Typical applications usually fall into the following categories:
-Dimensional: inspections of shapes, sizes, orientations of objects
-Surface blemish or defect: inspection or detection of gauges, scratches, pits or marks
-Assembly or completeness: inspection for presence or status of sub components
-Operational status: inspection or detection of erroneous operational events
The main purpose in all applications is to distill a complex photo, or series of photos, into a binary outcome as measured against a predefined set of references or rules. In essence, the camera is asked a complex question, for example “Is this component satisfactory” and is required to answer “Yes” or “No”.
The underlying architecture of how this “Yes” or “No” answer is inferred can further be divided into two distinct categories. Absolute comparison and probabilistic comparison. Absolute comparison is based on the concept of an image being compared to a database of images and the system recognizes the image as one of the provided samples, or in the case of deviation, does not.
Probabilistic comparison utilizes deep neural networks to assign a probability that an image contains features that are comparable to that of a provided training set, allowing the system to answer “Yes” or “No” with a degree of certainty for objects that it had never seen before.
With ever faster computers and the rise of industrial use of machine learning techniques, probabilistic approaches utilizing convolutional neural networks to determine outcomes is fast becoming the technology of choice.
Considerations for the application of a computer vision system
Vision inspection and evaluation systems that are integrally tied to convolutional neural networks are capable of effectively addressing a wide variety of problems, but there are some hard limits to consider before venturing down this road.
Problem definition
Although neural net vision systems can infer and evaluate scenarios that it has not seen before, training towards specific problem sets or applications greatly increases the accuracy and rapidly reduces time required to deploy. It is more effective to define multiple aspects for the system to consider, and aim to narrow the definition, rather than provide it with a broad and ill defined problem set that encompasses a wide spectrum of evaluations. During communication with clients, significant time is spent asking the question: “What exactly are we looking for?”
Cycle times
The computational loads that are associated with neural net driven vision systems, demand respect for expected cycle times. Super-fast cycle times are easily achievable, but the cost and complexity of hardware quickly escalates with the introduction of specialized, reliable cameras and embedded computing requirements.
Image quality
More sophisticated problems require more detailed images. A single instance may require images from multiple angles, taken by multiple cameras, often with more than one exposure setting to achieve the desired contrast levels. As these images are often taken from products or equipment in operational environments, the systems adjust for variations in orientation, location, focal distance and changes in environmental conditions such as time of day, dust levels, temperature or other that can and will affect image quality.
To allow for the inevitable expansion of the system or the so called “Can your system also check for this” scenario, image quality should be as good as is feasibly possible, and at the very least double that of what is expected to be “good enough”.
Where will near term breakthroughs come from?
Nearly all imaginable discreet applications of vision systems already exist in some form. The near term breakthroughs in system adoption will come from integration and standardization.
-Integration of vision systems into existing infrastructure: many industrial environments have a wide base of varying quality CCTV systems in operation, typically monitored by either safety or security personnel. Integration of ML models into these legacy systems allows evaluation against pre-defined scenarios. “Is that human wearing the required PPE gear?” may be the typical application.
Technology that achieve this functionality is already well established, but cost effective integration into existing systems that have grown organically and consists of a wide variety of multi generational hardware components remains challenging.
-Standardization and integration: as with everything else, scalable vision deployments will benefit from, and also contribute to standardization. From software protocols to hardware interfaces, vision integration into modern PLC’s and industrial robots are already on the rise in the form of augmented or assisted production processes. Various levels and systems are in use today, and out of the current experimental environment standards and norms will emerge.
Using neural networks in the interpretation of digital images rapidly increases the levels of functionality, but is significantly more complex than most legacy systems that rely on comparison with a predefined data set, and as such, training of the neural nets to achieve the required level of accuracy is both challenging and critical for success.
The vast improvements in quality and accuracy seen when applying neural networks to vision systems in the manufacturing and industrial sectors have rendered classic computer vision techniques almost obsolete. In particular, the use of convolutional neural networks - neural networks more apt for processing and classifying images - has made classifying products, detecting the presence or absence of specific items in complicated contexts, and the detection of visible defects in products far more precise and reliable than was possible before.
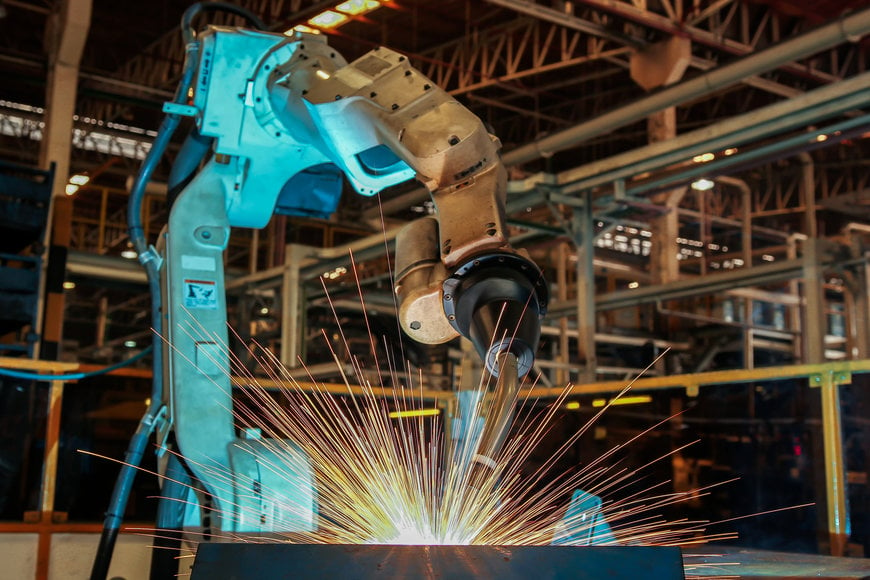