www.magazine-industry-usa.com
17
'18
Written on Modified on
Carry cold-rolled screws: innovation, precision and resistance
In mechanical engineering, people are always looking for new solutions. Eichenberger Gewinde AG, a company based in Switzerland, applies this principle every day, in a spirit of innovation based on constructive dialogue with its customers. This is supported by professionally-executed project management, enabling the development of solutions which satisfy all partners.
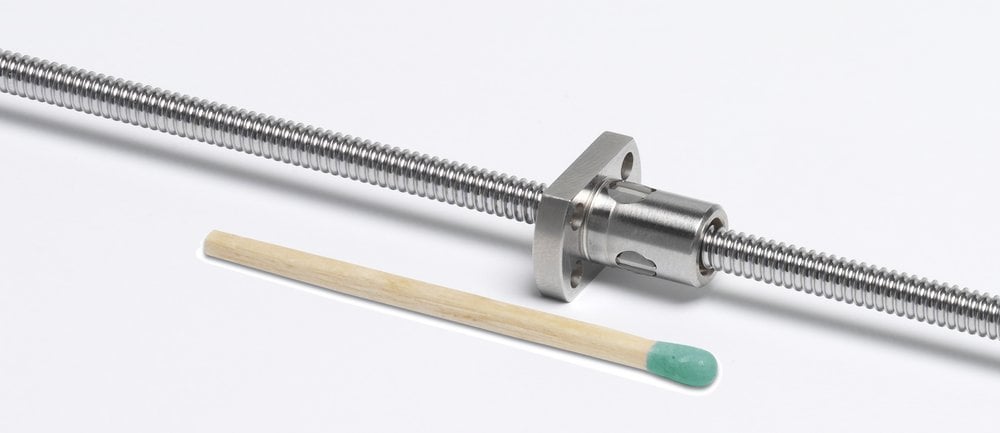
In terms of innovation, nature constitutes an excellent model. Living organisms, among their other characteristics, are adapted to all available habitats, even inhospitable ones. By using their adaptation techniques as a model, similar problems have been solved in mechanical engineering. There is an amazing similarity between ants, with their impressive capacity for work and their incredible strength, and CARRY ball screws, cold-rolled by Eichenberger with their reputation for robustness, precision, strength and efficiency. Although a tiger is capable of dragging a 900 kg buffalo over several hundred metres, an ant, in spite of its small size is the real Hercules of the animal kingdom. It is capable of lifting 50 times its own weight. To match this performance, a strong man would have to lift five tonnes. KGT cold-rolled ball screw drives outdo even this ratio. With a spindle diameter of only 40 mm, a KGT can support a load of 1000 times its inert weight.
What is the reason why CARRY ball screws from Eichenberger have so much resistance and precision? It is because they have been cold-rolled and hardened by induction, in a process developed by Eichenberger Gewinde.
Cold thread-rolling gives the screws precision and resistance
Unlike with grinding, milling or turning, the longitudinal fibres of the material are not cut during the thread rolling but are deflected. A thread is generated by deforming a part between two rotating rolling tools with the application of a radial dynamic force. The rolling tool profiles penetrate the surface of the part. So when the material is cold, it is pressed into the base of the thread-rolling tool and rolled to the nominal dimensions. The result is a dense surface, smoothly laminated, extremely resistant, essential for a long service life of the spindle. The roughness values of around 1.0 Rz at the edges of the thread and in the base radius as well as a significantly reduced susceptibility to indentation are major advantages. The friction coefficient of the steel balls is 0.003 to 0.001. In comparison, lubricated steel has a coefficient of 0.1 to 0.05. The excellent gliding properties of the cold-laminated balls ensure minimal abrasion and offer minimal contact surface to contamination. As a result, it becomes child's play to make the balls run silently. Eichenberger's internal structure is ideally suited to be able to simultaneously offer development, production, quality assurance and parts prototyping, including the threading tools. This capability means that they are remarkably flexible and adaptable. The uncompromising commitment of the employees on the subject of product quality and service is backed up by a modern machine park. Thanks to these advantages, they are able to handle a large number of development projects.