www.magazine-industry-usa.com
21
'09
Written on Modified on
Keyence vision systems speed up pharmaceutical product marking and improve its reliability
GlaxoSmithKline, wanting to improve the manufacturing processes at its Evreux factory, needed to upgrade the vision system for its high-throughput marking lines. The previous system required deactivation of automatic checking, forcing the factory to rely on inspection by the operators. The Keyence solution is showing itself to be not only reliable but also substantially less expensive than that of its competitors.
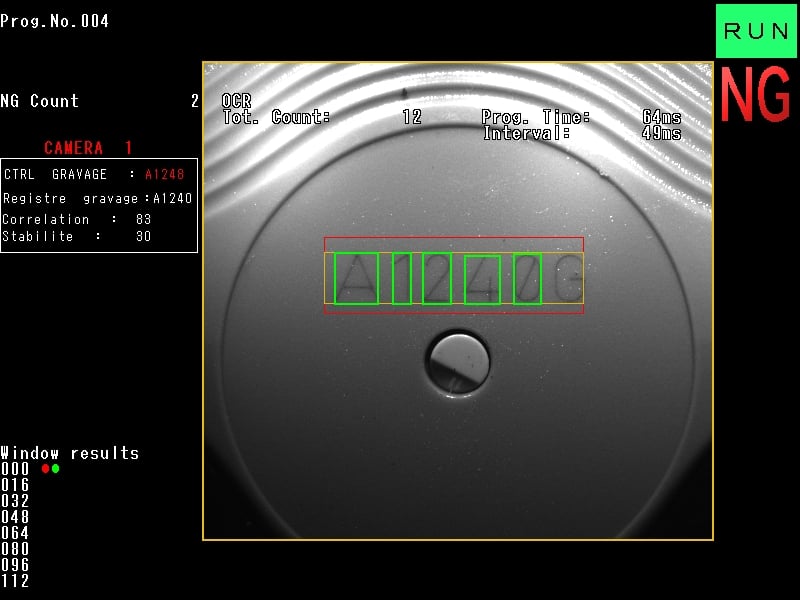
The vision system for monitoring marking consists of three video cameras. “The first is involved in the most demanding phase, as it has to read a black laser marking on plastic cases of various colours: four colours for four different drugs. Although reading is relatively easy on green or orange, it turns out to be complicated on blue or violet, which give limited contrast”, explains project leader Sylvain Bouckenooghe.
The solution was to apply specific lighting: “We consulted Keyence directly, and they were able to find a solution to our problems. The sales engineer suggested the necessary settings, including for the lighting. Keyence then lent us the equipment, which allowed us to see immediately that everything worked perfectly. Since then, a million items have been checked over 4 months in 24-hour three-shift operation without the least failure.”
The second camera checks the concentricity and the position of a label, with a tolerance of about 0.3 mm, while the third camera reads the label to check that the expiry date is printed correctly. For this the vision system uses built-in OCR.
Power at the service of reliable detection
“We knew from the start that the system was easily powerful enough to cope with our production throughputs. However, we are also very satisfied with the detection stability. In pharmaceuticals the constraints are somewhat more demanding, because we cannot accept 99.99% reliability, only 100%”, adds Sylvain Bouckenooghe.
The Keyence CV-5000 is the most powerful standalone vision system on the market. For example, it can process 1 million pixels in 20.5 ms. This processing power also makes production quality control more reliable, offering market-leading system repeatability (7x greater than current standards) and making a range of image processing options available to optimize the precision of the checks. In addition, 18 inspection functions are provided, meeting the needs of the most demanding vision applications (including Shape Trax modes and OCR).
The CV-5000 series models are controlled by a high-speed colour image processing engine and a high-speed RISC (reduced instruction set computer) central processing unit associated with two DSP (digital signal processors) dedicated to image processing. Overall, the series models use four processors in order to handle parallel processing and obtain the highest possible processing speed. The central processing unit and the DSPs enable double the speed of the best current models on the market.
A very economical solution with high performance
“We issued a request for proposals and we were surprised to see that the Keyence proposal was three times less expensive”, explains Sylvain Bouckenooghe. “The difference is explained by the fact that our cameras are much easier to integrate. Keyence France includes in its price the provision of services; consequently, even with similar hardware costs, we are considerably less expensive”, explains Alexandre Bony, Vision product manager with Keyence France.
“Implementation took only 4 days. Project management was relatively straightforward. Our experience with vision systems enabled us to identify the key points rapidly, to avoid wasting too much time and energy on the details,” adds Sylvain Bouckenooghe.
The CV-5000 series has functions that facilitate implementation. For example, a lighting setting automatically adjusts the brightness of an acquired image to that of the pre-recorded reference image. This avoids anomalies due to degradation of the lighting and to variation of daylight. Furthermore, up to 16 types of filter can be defined per window (anti-reflection, colour processing, etc.). Lastly, the CV-5000 series is a multi-camera system: up to four cameras from a range of 12 cameras, the widest choice on the market, can be connected to the controller. This is of interest in economic terms when an inspection involves several cameras. This configuration also enables large industrial sites to implement highly consistent solutions, which are consequently simpler and cheaper to install and maintain. The available cameras include 2-million or market-leading 5-million pixel colour CCD models. These cameras can process 2 million pixels in a single operation. The range includes the CV-5000 series 7x high-speed CCD cameras. They are the fastest in their category and are easily installed on ultra-rapid lines and for continuous production of parts. The 1-million pixel camera models are capable of processing in about the same time as conventional 240,000-pixel models.
An open system
“We prefer to have access to the inspection equipment. We did not want a black box like other systems available on the market. It is a strong point of the Keyence solution, as we have the capacity to modify the internal settings or add inspection tools simply, without calling on the supplier. This means that we avoid extra costs after commissioning,” concludes Sylvain Bouckenooghe.
The CV-5000 system provides maximum connectivity: On/off I/O, Ethernet port, USB and RS-232, and more. Interfacing with the controller was immediate. It is obviously used to discard nonconforming products from the production line.
The solution was to apply specific lighting: “We consulted Keyence directly, and they were able to find a solution to our problems. The sales engineer suggested the necessary settings, including for the lighting. Keyence then lent us the equipment, which allowed us to see immediately that everything worked perfectly. Since then, a million items have been checked over 4 months in 24-hour three-shift operation without the least failure.”
The second camera checks the concentricity and the position of a label, with a tolerance of about 0.3 mm, while the third camera reads the label to check that the expiry date is printed correctly. For this the vision system uses built-in OCR.
Power at the service of reliable detection
“We knew from the start that the system was easily powerful enough to cope with our production throughputs. However, we are also very satisfied with the detection stability. In pharmaceuticals the constraints are somewhat more demanding, because we cannot accept 99.99% reliability, only 100%”, adds Sylvain Bouckenooghe.
The Keyence CV-5000 is the most powerful standalone vision system on the market. For example, it can process 1 million pixels in 20.5 ms. This processing power also makes production quality control more reliable, offering market-leading system repeatability (7x greater than current standards) and making a range of image processing options available to optimize the precision of the checks. In addition, 18 inspection functions are provided, meeting the needs of the most demanding vision applications (including Shape Trax modes and OCR).
The CV-5000 series models are controlled by a high-speed colour image processing engine and a high-speed RISC (reduced instruction set computer) central processing unit associated with two DSP (digital signal processors) dedicated to image processing. Overall, the series models use four processors in order to handle parallel processing and obtain the highest possible processing speed. The central processing unit and the DSPs enable double the speed of the best current models on the market.
A very economical solution with high performance
“We issued a request for proposals and we were surprised to see that the Keyence proposal was three times less expensive”, explains Sylvain Bouckenooghe. “The difference is explained by the fact that our cameras are much easier to integrate. Keyence France includes in its price the provision of services; consequently, even with similar hardware costs, we are considerably less expensive”, explains Alexandre Bony, Vision product manager with Keyence France.
“Implementation took only 4 days. Project management was relatively straightforward. Our experience with vision systems enabled us to identify the key points rapidly, to avoid wasting too much time and energy on the details,” adds Sylvain Bouckenooghe.
The CV-5000 series has functions that facilitate implementation. For example, a lighting setting automatically adjusts the brightness of an acquired image to that of the pre-recorded reference image. This avoids anomalies due to degradation of the lighting and to variation of daylight. Furthermore, up to 16 types of filter can be defined per window (anti-reflection, colour processing, etc.). Lastly, the CV-5000 series is a multi-camera system: up to four cameras from a range of 12 cameras, the widest choice on the market, can be connected to the controller. This is of interest in economic terms when an inspection involves several cameras. This configuration also enables large industrial sites to implement highly consistent solutions, which are consequently simpler and cheaper to install and maintain. The available cameras include 2-million or market-leading 5-million pixel colour CCD models. These cameras can process 2 million pixels in a single operation. The range includes the CV-5000 series 7x high-speed CCD cameras. They are the fastest in their category and are easily installed on ultra-rapid lines and for continuous production of parts. The 1-million pixel camera models are capable of processing in about the same time as conventional 240,000-pixel models.
An open system
“We prefer to have access to the inspection equipment. We did not want a black box like other systems available on the market. It is a strong point of the Keyence solution, as we have the capacity to modify the internal settings or add inspection tools simply, without calling on the supplier. This means that we avoid extra costs after commissioning,” concludes Sylvain Bouckenooghe.
The CV-5000 system provides maximum connectivity: On/off I/O, Ethernet port, USB and RS-232, and more. Interfacing with the controller was immediate. It is obviously used to discard nonconforming products from the production line.