www.magazine-industry-usa.com
25
'18
Written on Modified on
SGD Pharma upgrades its Chinese plant toward an automated and improved production.
SGD Pharma's Zhanjiang (China) plant produces 1.2 million Type II & III flint molded glass vials daily for the parenteral market and for health care beauty products. With a surface of 85,000 m2, the plant included a glass furnace, 6 production lines, an ISO 8 clean room of 2,000 m², a resorting room and a customization workshop. Early 2018, SGD Pharma invested 7 million Euros to improve the automation and the production, including the rebuilding of the furnace, to make the Zhanjiang plant an exemplary production center.
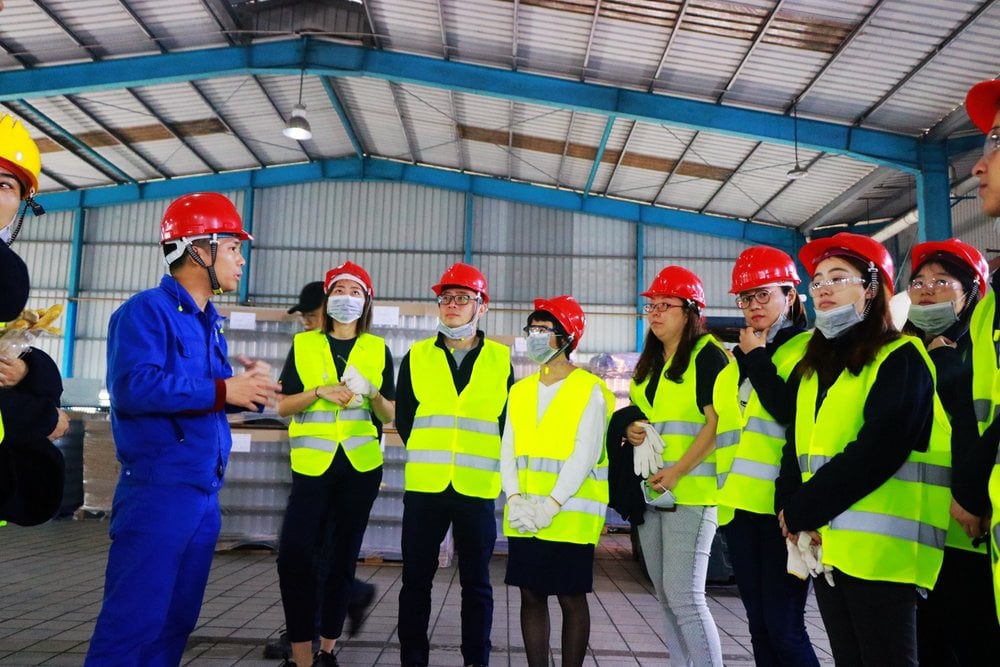
The rebuilt of the furnace in Zhanjiang took place in February. This improvement project, that includes the renewal and reorganization of the equipment for the production lines, the clean room and the resorting as well as the automation of the decoration workshop is part of the desire to increase the production capacity, improve the quality of glass and offer a better flexibility for deliveries.
A furnace completely rebuilt to increase production
The energy supply for the furnace has been modified; Whereas previously it was fuel-based, it now consumes natural liquid gas, which reduces the carbon footprint. This transformation brings the furnace into compliance with China's new environmental regulations. In addition to this reduction, the plant has shown a reduction in non-carbon emissions (SO2).
The furnace components have also been transformed to obtain a more precise refinement that improves the quality of the glass. The rebuilt took 40 days and the overall production has increased by 11%.
Improved process and renewed production lines
For the Hot end zone, for the transformation of glass into flasks, one of the 6 production lines has been completely renewed. In addition, 2 lines have been completely upgraded with the most advanced equipment on the market.
As the Cold end zone, the ISO 8 clean room has been completely redesigned and enlarged in accordance with ISO standards. New inspection machines have also been installed for an optimized process.
The plant is certified ISO 15378, 22000 & SA 8000 and benefits from the Group's technologies, processes and European expertise for its production made in China.
With 5 plants around the world, SGD Pharma guarantees its customers the same level of quality, reliability and safety of its products.
A furnace completely rebuilt to increase production
The energy supply for the furnace has been modified; Whereas previously it was fuel-based, it now consumes natural liquid gas, which reduces the carbon footprint. This transformation brings the furnace into compliance with China's new environmental regulations. In addition to this reduction, the plant has shown a reduction in non-carbon emissions (SO2).
The furnace components have also been transformed to obtain a more precise refinement that improves the quality of the glass. The rebuilt took 40 days and the overall production has increased by 11%.
Improved process and renewed production lines
For the Hot end zone, for the transformation of glass into flasks, one of the 6 production lines has been completely renewed. In addition, 2 lines have been completely upgraded with the most advanced equipment on the market.
As the Cold end zone, the ISO 8 clean room has been completely redesigned and enlarged in accordance with ISO standards. New inspection machines have also been installed for an optimized process.
The plant is certified ISO 15378, 22000 & SA 8000 and benefits from the Group's technologies, processes and European expertise for its production made in China.
With 5 plants around the world, SGD Pharma guarantees its customers the same level of quality, reliability and safety of its products.
https://www.sgd-pharma.com/
