www.magazine-industry-usa.com
14
'18
Written on Modified on
Eichenberger Gewinde : Safety in the area of high voltage with cold-rolled ball screws. When the ball screw is in control of the electric arc
Electricity is, figuratively speaking, the lifeblood of our modern society and economy. Without it, nothing is possible. Circuit breakers are essential for the safe operation of our power supply. Among others, their task is to turn the entire output of a power plant on and off (in the gigawatt range) and to direct voltages up to 1,500 kV. The cold-rolled Carry ball screw from Burg (CH) plays an extremely important and responsible key part in this.
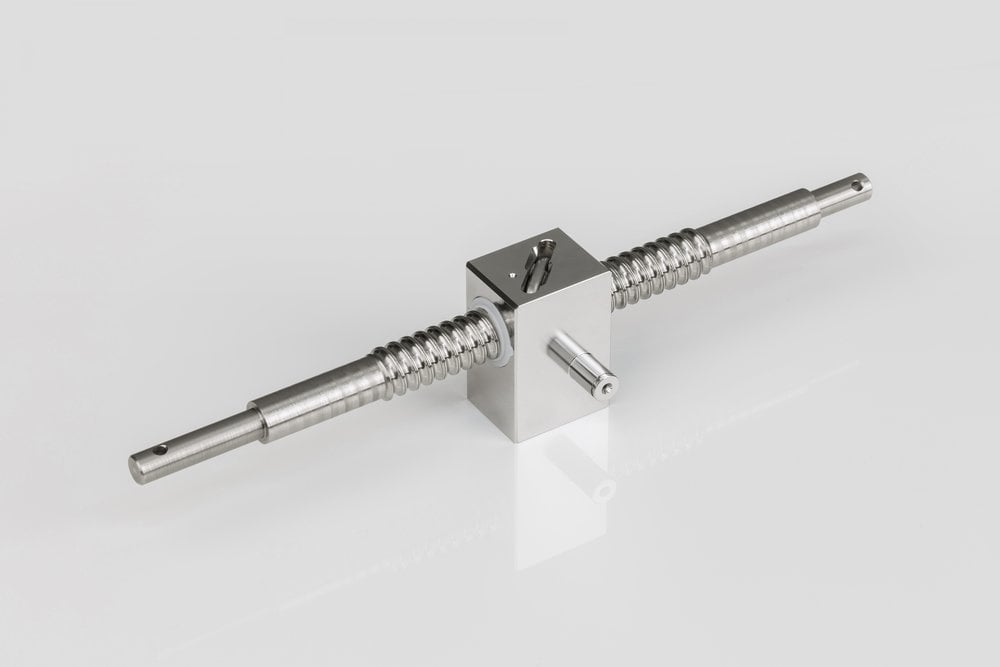
Electrical energy is transported from the power generator, for example the power plant, to the power consumer. In order to save on loss and therefore costs during electricity transfer, the goal is to produce the lowest possible currents. So that a lot of output can still be transferred, high voltages are used. High voltages and maximum voltages of up to 1,150 kV are utilised. The entire European power grid has a length of about 1.8 million kilometres.
One step ahead with the right technology partner
A globally leading technology company was looking for a totally reliable drive solution to instantly separate the heavy metal contacts in circuit breakers. When the energy technology company found Eichenberger Gewinde AG, the search was over. The Swiss thread specialist has been providing screw solutions for decades which don’t just stand out in terms of performance, quality and reliability, but also support the essential innovative lead. When it’s about the construction of specifically integrated drive components, customers all over the world benefit from Eichenberger's profound knowledge and its remarkable development and manufacturing potential.
The thread rolling company always focuses on a requirement-orientated, constructive exchange with its partners. On the one hand, the trick is to develop extraordinary customer solutions and, on the other hand, to ensure powerful and sophisticated production procedures. Future-orientated, energetic thinking is firmly established in Eichenberger's corporate culture. The perfect “in-house” company structure means that development, production, quality assurance and agile prototype creation, including thread rolling tools and end machining, can be offered at the same time. This releases an exceptional flexibility and adaptability. The employees’ deep-seated quality consciousness is coupled with a corresponding modern plant. Thanks to these factors, a lot can happen, especially when the location is Switzerland. Constant development of practical customer solutions is a passion of Eichenberger's. Thread shapes outside the norm are the sought-after assignments.
Advantages of thread rolling
Having realised the potential of this drive, the energy technology manufacturer backed the robust cold-rolled ball screws from Burg (CH), which are being produced in large numbers using a cost-effective thread rolling process. As opposed to grinding, milling or turning, during thread rolling, the material’s longitudinal fibres are not cut but diverted. The result is a compressed and extremely resilient surface which has been rolled smooth. This is essential for the long service life of a screw. The roughness values around Rz 1.0 on the edges of the thread and in the base radius as well as significantly reduced notch-sensitivity, are also excellent advantages. In steel ball bearings, the rolling friction co-efficient is 0.003 to 0.001 compared with sliding friction of steel on steel (lubricated) of 0.1 to 0.05. The excellent sliding properties of cold-rolled ball screws ensure minimal friction and provide little scope for contamination. The quiet rolling of the balls is therefore very easy.
Total reliability
A high voltage short circuit reaches its maximum value after as little as 5 milliseconds. Luckily, interrupting the power supply in the event of a short circuit is not often needed. However, if this occurs unexpectedly, the total reliability of the mechanical drive elements is indispensable! The Carry ball screw guarantees maximum functional safety with enormous power (efficiency > 0.9) and robustness. Carry prepares the mechanical power-on and power-off operation in the circuit breaker using helical springs. Two solid thrust rods are firmly connected on both sides with the custom-made nut, the so-called carrier. These two levers move the huge strikers which are subjected to spring pressure and which separate the metal contact extremely quickly. Despite adverse weather conditions and extreme temperature differences, the cold-rolled, resilient Carry does its job totally reliably, whilst being maintenance-free.
The customer-specific requirements for the ball screw with integrated customer interface in the nut are “substantial and varying”. When it comes to axial force and geometry, requirements are high. Tribological aspects such as friction, wear and lubrication are important prerequisites that must be fulfilled. The tricky task of adapting the outside of the body of the nut to the particular interface requirements and the kinematic conditions is particularly challenging. Based on the entirety of the demands, for global use, all sorts of different dimensions were developed for the Carry ball screw, consisting of the cold-rolled screw and the specific carrier nut.
When reliability and customer benefits are no coincidence
The flexibility of mechanical-dynamic functional elements is a major contribution to the success of projects in drive technology. The realisation that quality and reliability have to be “integrated into the development” of a product, is crucial. Eichenberger Gewinde AG's high-tech testing systems are therefore indispensable during many stages of product creation. Only when screws, nuts, balls and lubrication are in perfect balance, can the highest demands be met. Based on the tight tolerances in torque, axial play and concentricity, a 100 % test is carried out on a special test bench. The most stringent requirements, for example concerning complete traceability, are not only a must in the automation, vehicle or medical industry. On request, Eichenberger will simply etch data references on ball screws or lead screws using permanent laser labelling as a data matrix. These days, everything is about technological advantages and increased performance density, at generally reduced investment costs. When the inventor of the product is also its most competent manufacturer, the advantages are obvious.