www.magazine-industry-usa.com
05
'23
Written on Modified on
DIGITAL TWIN IN THE FACTORY: A REALITY MADE POSSIBLE
By using digital twin technology, manufacturers can monitor, simulate, and optimize the performance of their assets in real-time, as well as test new scenarios and solutions before implementing them in the real world - By K.A. Gerardino.
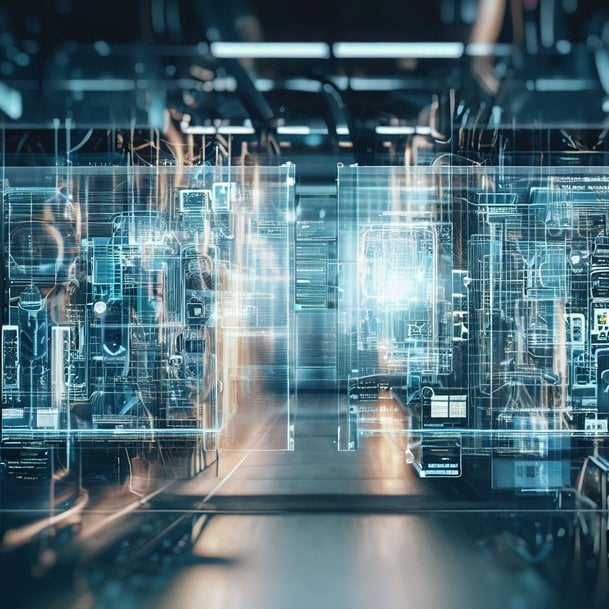
Imagine a factory where you can monitor and control every aspect of the production process, from the machines' design and performance to the product's quality and efficiency. How about a factory where you can test and optimize different scenarios, such as changing the layout, adding new equipment, or adjusting the parameters, without affecting the actual operations? Now, try and visualize a factory where you can detect and prevent problems before they cause downtime, waste, or defects. This is not a fantasy, but a reality made possible by digital twin technology.
Digital twin in a factory is a concept that involves creating a virtual representation of a physical asset, such as a machine, a process, or a building, using data from sensors or other sources. By using digital twin technology, manufacturers can monitor, simulate, and optimize the performance of their assets in real-time, as well as test new scenarios and solutions before implementing them in the real world. Digital twins in factories can help improve efficiency, quality, safety, and innovation in manufacturing systems. In this paper, we will explore the benefits and challenges of the digital twin in factories and some real examples of how it is applied in different industries.
Before we begin, let us go back to history when the digital twin concept first started. According to some sources, the idea of digital twin technology was first voiced in 1991, with the publication of Mirror Worlds, by David Gelernter. However, Dr. Michael Grieves (then on faculty at the University of Michigan) is credited with first applying the concept of digital twins to manufacturing in 2002 and formally announcing the digital twin software concept. He proposed the digital twin as the conceptual model underlying product lifecycle management (PLM). The term “digital twin” was later popularized by John Vickers of NASA in a 2010 Roadmap Report. NASA used digital twin technology to simulate systems in space, such as the Apollo 13 mission in 19703. Since then, digital twin technology has evolved and expanded to various domains and industries, thanks to the advancement of sensors, the Internet of Things (IoT), cloud computing, and artificial intelligence (AI).
Digital Twin in your Factory
Digital twin technology is a powerful tool that can help you improve your factory’s performance, efficiency, and innovation. By creating a virtual replica of your physical assets and systems, you can monitor and control them in real-time, test and optimize different scenarios, and predict and prevent problems. But how can you implement digital twin technology in your factory? What are the steps and benefits of using this technology?
First, you need to acquire data from your physical assets and systems using sensors, operational data, maintenance history, and other sources. This data should be accurate, reliable, and consistent to reflect the current state and condition of your assets.
Second, you need to develop a digital twin by integrating this data into a virtual model of your asset using a digital twin solution. The digital twin should be able to simulate the behaviour and performance of your asset under different scenarios and conditions. You can use various tools and platforms to create and manage your digital twins, such as Resonai, Facilio, or Hitachi Lumada.
Third, you need to boost the capabilities of your digital twin by adding more data layers and analytics to support new use cases. You can use artificial intelligence and advanced modelling techniques to enable your digital twin to provide predictions, prescriptions, and optimizations for your asset. You can also connect your digital twin with other digital twins to create a network of interconnected assets and systems.
Fourth, you need to monitor and control your digital twin by using dashboards, visualizations, and alerts. You can use your digital twin to track the performance and health of your asset, detect and prevent problems, test, and optimize solutions, and implement changes in real-time. You can also use your digital twin to learn from the past, understand the present, and anticipate the future.
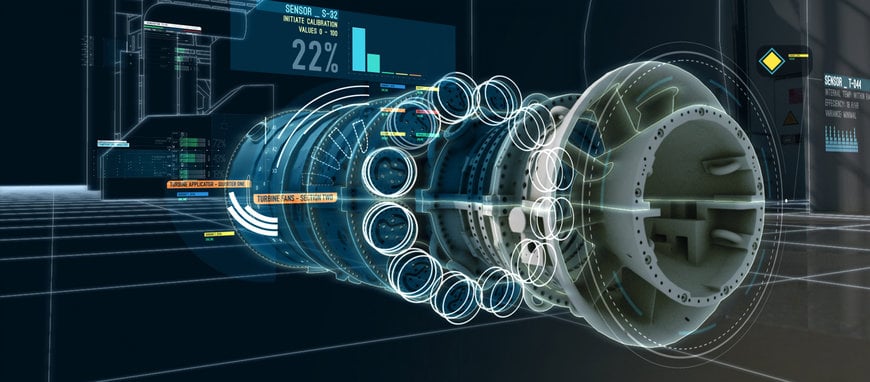
Photo: General Electric
Difficulties in Applying Digital Twin Technology
The digital twin is a powerful technology that can create a virtual copy of a real-world component in the manufacturing process. By using inputs from sensors, data analytics, and simulation, the digital twin can help optimize performance, reduce costs, and improve quality. However, implementing and maintaining a digital twin is not without challenges.
Data quality and availability: A digital twin requires a large amount of data from various sources, such as sensors, machines, products, and processes, to create an accurate and realistic model of the factory. However, data quality and availability may vary depending on the factory’s infrastructure, connectivity, and security. Poor data quality and availability can affect the reliability and validity of the digital twin and its simulations.
Data processing and storage: The digital twin also requires a high level of data processing and storage capacity to handle the complex and dynamic data streams from the factory. This may pose a challenge for some factories that lack the necessary hardware, software, and network resources to support the digital twin. Moreover, data processing and storage may incur additional costs and energy consumption for the factory.
Data privacy and security: Digital twin technology involves collecting and sharing sensitive data from the factory, such as intellectual property, trade secrets, and personal information. This may raise concerns about data privacy and security, especially when the data is transmitted over the internet or stored in the cloud. Data breaches, cyberattacks, or unauthorized access may compromise the confidentiality, integrity, and availability of the data and the digital twin. Therefore, digital twin requires robust data protection mechanisms and policies to ensure data privacy and security.
Interoperability and standardization: Digital twin requires interoperability and standardization among different data sources, formats, protocols, platforms, and systems to enable seamless data exchange and integration. However, interoperability and standardization may be challenging due to the diversity and complexity of the factory’s components and processes. Moreover, there may be a lack of common definitions, frameworks, methodologies, and metrics for developing and validating digital twins across different industries and domains. Therefore, the digital twin requires harmonization and coordination among different stakeholders and organizations to ensure interoperability and standardization.
Skills and expertise: A digital twin requires skills and expertise in various fields, such as engineering, computer science, mathematics, statistics, artificial intelligence, machine learning, data science, and domain knowledge. However, skills and expertise may be scarce or unevenly distributed among the factory’s workforce. Moreover, digital twins may require continuous learning and training to keep up with the rapid changes and innovations in technology. Therefore, the digital twin requires investment in human capital development and education to ensure skills and expertise.
Examples of Companies Using Digital Twin
Digital twin technology is widely used in various industries, such as manufacturing, aerospace, healthcare, and energy. Here are some examples of real-life scenarios in the factories using digital twin technology:
Manufacturing
In the manufacturing sector, a digital twin can help design, test, and monitor products and processes.
For example, Ford develops seven digital twins for each model of vehicle it produces. These digital twins can simulate different scenarios, such as weather conditions, road surfaces, and driving behaviours, to improve the safety and efficiency of the vehicles. Moreover, digital twins can help detect and prevent defects, reduce downtime, and optimize maintenance schedules.
Another example is Tesla – they adopted digital twin technology by creating a virtual replica for each car they have sold. Sensor data from thousands of cars, apps, and even superchargers continuously stream into each car’s simulation at the factory.
BMW, on the other hand, is building a digital twin of one of its automotive plants to bring new efficiencies to its business. The digital twin will enable BMW to simulate the impact of changes in production schedules, optimize resource management, and improve quality control.
Next, Nissan is using digital twin technology to design and test new vehicles before they are manufactured. The digital twin allows Nissan to evaluate the performance, safety, and reliability of different models and configurations in various scenarios.
Aerospace
In the aerospace industry, digital twins can help improve the reliability and performance of aircraft engines.
For example, Rolls-Royce uses digital twins to monitor the health and condition of its engines in real-time. The digital twin can collect data from sensors, such as temperature, pressure, and vibration, and analyze it to identify potential issues and optimize fuel consumption. Furthermore, digital twins can help predict the lifespan and performance of the engines under different operating conditions.
Next, Boeing is using digital twin technology to create virtual replicas of its aircraft and their components. The digital twins enable Boeing to monitor the performance, quality, and safety of its products in real-time, as well as optimize the manufacturing and maintenance processes.
In addition, Airbus is using digital twin technology to design and test new aircraft models before they are built. The digital twins allow Airbus to simulate the aerodynamics, structural integrity, and fuel efficiency of different configurations and scenarios.
Healthcare
In the healthcare sector, Digital twins can enable personalized diagnosis, treatment planning, and simulation for each patient based on their unique data and characteristics. It can also help monitor the health status and vital signs of patients in real-time, as well as predict and prevent potential complications or adverse events. Digital twins can accelerate the development and testing of new medicines, devices, and therapies by simulating their effects and outcomes on virtual models of human physiology and pathology. This technology can also help optimize the design, performance, and maintenance of medical devices and equipment by using data from sensors and feedback loop. This powerful technology can improve the efficiency and quality of healthcare services by using data-driven insights to manage the capacity, staffing, and care models of healthcare facilities. It can also help reduce costs and risks by enabling data-driven decision-making and risk-based assessments.
Here are some examples of healthcare companies using digital twin in their factories:
- Philips is a global leader in health technology that provides integrated solutions across the health continuum. Philips is using digital twin technology to create virtual models of medical devices, such as ventilators, scanners, and monitors, to optimize their design, performance, and maintenance.
- Siemens Healthineers is a leading medical technology company that offers innovative products and services in diagnostic and therapeutic imaging, laboratory diagnostics, and molecular medicine. Siemens Healthineers is using digital twin technology to create digital representations of human organs, such as the heart, lung, and liver, to enable personalized diagnosis, treatment planning, and simulation.
- PrediSurge is a French startup that develops digital twin solutions for cardiovascular surgery. PrediSurge is using digital twin technology to create realistic 3D models of patients’ arteries and blood flow, to help surgeons plan and perform safer and more effective interventions.
Market Overview in 2023
The global digital twin market size is projected to grow at a compound annual growth rate (CAGR) of 37.5% from 2023 to 2030. The market is expected to grow significantly over the forecast period in line with the growing adoption of the Internet of Things (IoT) and big data analytics and the growing need to ensure cost-efficient operations, optimized processes, and reduced time to market.
The key drivers of the market growth include the increasing public and private investments in digital transformation solutions, the implementation of emerging technologies such as cloud computing, artificial intelligence (AI), IoT, and machine learning (ML) in digital twin solutions, and the rising demand for digital twin solutions across various end-use industries such as aerospace & defence, automotive & transportation, manufacturing, healthcare, retail, energy & utilities, real estate, IT and telecom, and others.
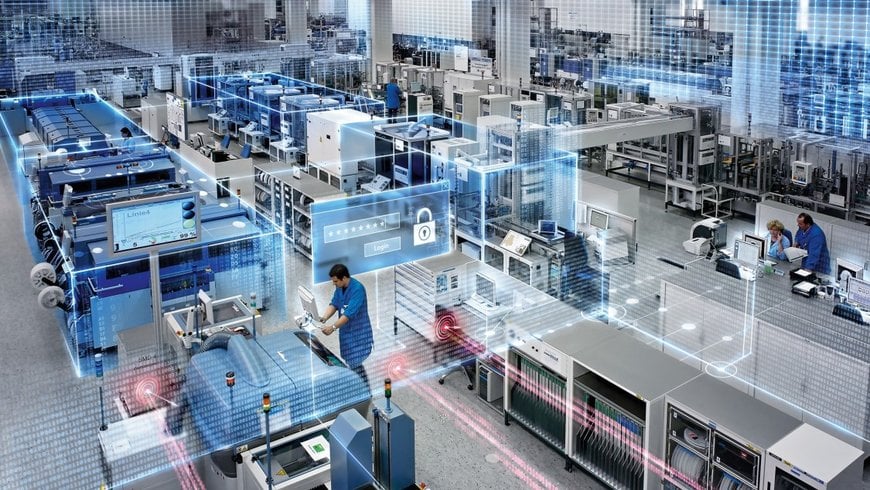
Photo: Siemens
Top 10 Key Players
Here are the top 10 key players in digital twin technology:
Microsoft Corporation: Microsoft is a global technology company that offers a range of software, hardware, cloud, and AI solutions. Microsoft’s digital twin platform, Azure Digital Twins, enables users to create and manage comprehensive digital models of physical environments and assets, and leverage IoT, AI, and analytics to optimize performance and efficiency.
IBM Corporation: IBM is a global technology and consulting company that provides innovative solutions in cloud, AI, IoT, blockchain, and cybersecurity. IBM’s digital twin platform, IBM Maximo Asset Monitor, enables users to monitor the health and performance of their physical assets and processes, and use AI and analytics to gain insights and improve outcomes.
General Electric Company: GE is a global industrial company that operates in various sectors such as aviation, healthcare, power, renewable energy, and digital. GE’s digital twin platform, Predix Platform, enables users to create and manage digital models of industrial assets and processes, and use IoT, AI, and analytics to optimize operations and productivity.
Siemens AG: Siemens is a global engineering and technology company that offers products and services in automation, digitalization, electrification, and mobility. Siemens’ digital twin platform, MindSphere, enables users to connect and manage their physical and virtual worlds, and use IoT, AI, and analytics to enhance performance and innovation.
Dassault Systèmes SE: Dassault Systèmes is a global software company that provides 3D design, engineering, simulation, and collaboration solutions. Dassault Systèmes’ digital twin platform, 3DEXPERIENCE Platform, enables users to create and manage digital models of products, systems, and experiences, and use simulation and analytics to improve quality and sustainability.
Oracle Corporation: Oracle is a global technology company that offers a range of cloud, database, and software solutions. Oracle’s digital twin platform, Oracle IoT Cloud Service, enables users to create and manage digital models of their physical assets and processes, and use IoT, AI, and analytics to optimize performance and efficiency.
PTC Inc: PTC is a global software company that provides solutions for industrial IoT, augmented reality, CAD, PLM, and SaaS. PTC’s digital twin platform, ThingWorx, enables users to create and manage digital models of their physical products and systems, and use IoT, AI, and analytics to enhance innovation and customer experience.
SAP SE: SAP is a global software company that offers enterprise applications, cloud solutions, analytics, and business networks. SAP’s digital twin platform, SAP Asset Intelligence Network, enables users to create and manage digital models of their physical assets and processes, and use IoT, AI, and analytics to improve reliability and productivity.
Schneider Electric SE: Schneider Electric is a global leader in energy management and automation solutions. Schneider Electric’s digital twin platform, EcoStruxure Platform, enables users to create and manage digital models of their physical assets and processes, and use IoT, AI, and analytics to enhance sustainability and efficiency.
Wipro Limited: Wipro is a global IT services company that offers consulting, digital transformation, cloud, cybersecurity, and engineering solutions. Wipro’s digital twin platform, Wipro HOLMES AI Platform for Industry 4.0 (HAPI), enables users to create and manage digital models of their physical assets and processes, and use IoT, AI, and analytics to optimize performance and quality.
Latest Trends
Some of the latest trends in digital twin in 2023 and beyond are:
Increased Internet of Things (IoT) adoption
IoT devices and sensors are the key sources of data for digital twins. As IoT adoption grows across different sectors, such as manufacturing, healthcare, energy, and smart cities, more data will be available to create and update digital twins. IoT will also enable real-time connectivity and communication between digital twins and their physical counterparts.
Empowering DTs with artificial intelligence (AI)
AI techniques, such as machine learning, deep learning, computer vision, and natural language processing, can enhance the capabilities and applications of digital twins. AI can help analyze the data collected by digital twins, generate insights and recommendations, automate actions and decisions, and enable self-learning and adaptation.
Integrating with virtual reality (VR) & augmented reality (AR)
VR and AR technologies can provide immersive and interactive experiences for users to interact with digital twins. VR can create realistic simulations of digital twins for training, testing, and visualization purposes. AR can overlay digital information on physical objects or environments to enhance user awareness and engagement.
Emphasis on sustainability
Digital twin technology can help address the environmental and social challenges faced by various industries. Digital twins can help optimize the use of resources, reduce waste and emissions, improve safety and quality, and enhance social impact. Digital twins can also help monitor and measure the sustainability performance of products, processes, and systems.
Adoption of cloud-based platforms
Cloud computing provides the infrastructure and services to support the creation and management of digital twins. Cloud platforms can offer scalability, flexibility, security, and cost-effectiveness for digital twin solutions. Cloud platforms can also enable collaboration and integration among different stakeholders and systems involved in digital twin projects.
Advancements in blockchain technology
Blockchain technology can provide a secure and transparent way to store and share data among digital twins. Blockchain can also enable trust and verification among different parties involved in digital twin transactions. Blockchain can also facilitate smart contracts that can automate actions and payments based on predefined rules.
Incorporating process intelligence
Process intelligence is a technique that combines process mining, business intelligence, and AI to analyze and optimize business processes. Process intelligence can help create digital twins of business processes that can monitor, measure, and improve their performance and outcomes. Process intelligence can also help identify bottlenecks, inefficiencies, risks, and opportunities for improvement in business processes.
Imposed security awareness
Security is a critical aspect of digital twin technology as it involves sensitive data and systems that can be vulnerable to cyberattacks. Security awareness is the practice of educating users about the potential threats and best practices to protect their digital assets. Security awareness can help prevent unauthorized access, manipulation, or damage to digital twins and their physical counterparts.
Conclusion
Digital twin technology can help you improve your factory in many ways, making your products more reliable and efficient; saving your time and money, boosting your innovation and customization, and supporting your sustainability and social responsibility. This powerful technology can also help you adapt to the changing world of the Fourth Industrial Revolution, where customers demand extra, competitors challenge further, regulations require a great deal, and technologies offer to no end. It is the future of factories, where you can design, produce, and deliver value to your customers and stakeholders with ease and excellence. Digital twin technology is expected to grow significantly in the future, as more data, devices, and platforms become available. Lastly, digital twin is not just a concept, but a reality that can be achieved and experienced in the factory floor.
The global digital twin market size is projected to grow at a compound annual growth rate (CAGR) of 37.5% from 2023 to 2030. The market is expected to grow significantly over the forecast period in line with the growing adoption of the Internet of Things (IoT) and big data analytics and the growing need to ensure cost-efficient operations, optimized processes, and reduced time to market.
The key drivers of the market growth include the increasing public and private investments in digital transformation solutions, the implementation of emerging technologies such as cloud computing, artificial intelligence (AI), IoT, and machine learning (ML) in digital twin solutions, and the rising demand for digital twin solutions across various end-use industries such as aerospace & defence, automotive & transportation, manufacturing, healthcare, retail, energy & utilities, real estate, IT and telecom, and others.
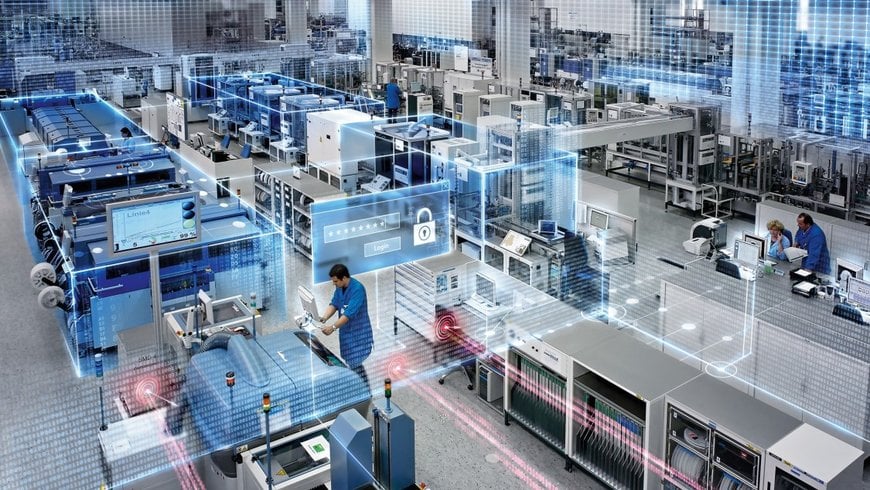
Photo: Siemens
Top 10 Key Players
Here are the top 10 key players in digital twin technology:
Microsoft Corporation: Microsoft is a global technology company that offers a range of software, hardware, cloud, and AI solutions. Microsoft’s digital twin platform, Azure Digital Twins, enables users to create and manage comprehensive digital models of physical environments and assets, and leverage IoT, AI, and analytics to optimize performance and efficiency.
IBM Corporation: IBM is a global technology and consulting company that provides innovative solutions in cloud, AI, IoT, blockchain, and cybersecurity. IBM’s digital twin platform, IBM Maximo Asset Monitor, enables users to monitor the health and performance of their physical assets and processes, and use AI and analytics to gain insights and improve outcomes.
General Electric Company: GE is a global industrial company that operates in various sectors such as aviation, healthcare, power, renewable energy, and digital. GE’s digital twin platform, Predix Platform, enables users to create and manage digital models of industrial assets and processes, and use IoT, AI, and analytics to optimize operations and productivity.
Siemens AG: Siemens is a global engineering and technology company that offers products and services in automation, digitalization, electrification, and mobility. Siemens’ digital twin platform, MindSphere, enables users to connect and manage their physical and virtual worlds, and use IoT, AI, and analytics to enhance performance and innovation.
Dassault Systèmes SE: Dassault Systèmes is a global software company that provides 3D design, engineering, simulation, and collaboration solutions. Dassault Systèmes’ digital twin platform, 3DEXPERIENCE Platform, enables users to create and manage digital models of products, systems, and experiences, and use simulation and analytics to improve quality and sustainability.
Oracle Corporation: Oracle is a global technology company that offers a range of cloud, database, and software solutions. Oracle’s digital twin platform, Oracle IoT Cloud Service, enables users to create and manage digital models of their physical assets and processes, and use IoT, AI, and analytics to optimize performance and efficiency.
PTC Inc: PTC is a global software company that provides solutions for industrial IoT, augmented reality, CAD, PLM, and SaaS. PTC’s digital twin platform, ThingWorx, enables users to create and manage digital models of their physical products and systems, and use IoT, AI, and analytics to enhance innovation and customer experience.
SAP SE: SAP is a global software company that offers enterprise applications, cloud solutions, analytics, and business networks. SAP’s digital twin platform, SAP Asset Intelligence Network, enables users to create and manage digital models of their physical assets and processes, and use IoT, AI, and analytics to improve reliability and productivity.
Schneider Electric SE: Schneider Electric is a global leader in energy management and automation solutions. Schneider Electric’s digital twin platform, EcoStruxure Platform, enables users to create and manage digital models of their physical assets and processes, and use IoT, AI, and analytics to enhance sustainability and efficiency.
Wipro Limited: Wipro is a global IT services company that offers consulting, digital transformation, cloud, cybersecurity, and engineering solutions. Wipro’s digital twin platform, Wipro HOLMES AI Platform for Industry 4.0 (HAPI), enables users to create and manage digital models of their physical assets and processes, and use IoT, AI, and analytics to optimize performance and quality.
Latest Trends
Some of the latest trends in digital twin in 2023 and beyond are:
Increased Internet of Things (IoT) adoption
IoT devices and sensors are the key sources of data for digital twins. As IoT adoption grows across different sectors, such as manufacturing, healthcare, energy, and smart cities, more data will be available to create and update digital twins. IoT will also enable real-time connectivity and communication between digital twins and their physical counterparts.
Empowering DTs with artificial intelligence (AI)
AI techniques, such as machine learning, deep learning, computer vision, and natural language processing, can enhance the capabilities and applications of digital twins. AI can help analyze the data collected by digital twins, generate insights and recommendations, automate actions and decisions, and enable self-learning and adaptation.
Integrating with virtual reality (VR) & augmented reality (AR)
VR and AR technologies can provide immersive and interactive experiences for users to interact with digital twins. VR can create realistic simulations of digital twins for training, testing, and visualization purposes. AR can overlay digital information on physical objects or environments to enhance user awareness and engagement.
Emphasis on sustainability
Digital twin technology can help address the environmental and social challenges faced by various industries. Digital twins can help optimize the use of resources, reduce waste and emissions, improve safety and quality, and enhance social impact. Digital twins can also help monitor and measure the sustainability performance of products, processes, and systems.
Adoption of cloud-based platforms
Cloud computing provides the infrastructure and services to support the creation and management of digital twins. Cloud platforms can offer scalability, flexibility, security, and cost-effectiveness for digital twin solutions. Cloud platforms can also enable collaboration and integration among different stakeholders and systems involved in digital twin projects.
Advancements in blockchain technology
Blockchain technology can provide a secure and transparent way to store and share data among digital twins. Blockchain can also enable trust and verification among different parties involved in digital twin transactions. Blockchain can also facilitate smart contracts that can automate actions and payments based on predefined rules.
Incorporating process intelligence
Process intelligence is a technique that combines process mining, business intelligence, and AI to analyze and optimize business processes. Process intelligence can help create digital twins of business processes that can monitor, measure, and improve their performance and outcomes. Process intelligence can also help identify bottlenecks, inefficiencies, risks, and opportunities for improvement in business processes.
Imposed security awareness
Security is a critical aspect of digital twin technology as it involves sensitive data and systems that can be vulnerable to cyberattacks. Security awareness is the practice of educating users about the potential threats and best practices to protect their digital assets. Security awareness can help prevent unauthorized access, manipulation, or damage to digital twins and their physical counterparts.
Conclusion
Digital twin technology can help you improve your factory in many ways, making your products more reliable and efficient; saving your time and money, boosting your innovation and customization, and supporting your sustainability and social responsibility. This powerful technology can also help you adapt to the changing world of the Fourth Industrial Revolution, where customers demand extra, competitors challenge further, regulations require a great deal, and technologies offer to no end. It is the future of factories, where you can design, produce, and deliver value to your customers and stakeholders with ease and excellence. Digital twin technology is expected to grow significantly in the future, as more data, devices, and platforms become available. Lastly, digital twin is not just a concept, but a reality that can be achieved and experienced in the factory floor.