Predictive Maintenance, Artificial Intelligence and Factory Efficiency
Predictive maintenance increases manufacturing efficiency, saves on maintenance costs, and contributes to a healthy bottom line. By Milton D'Silva.
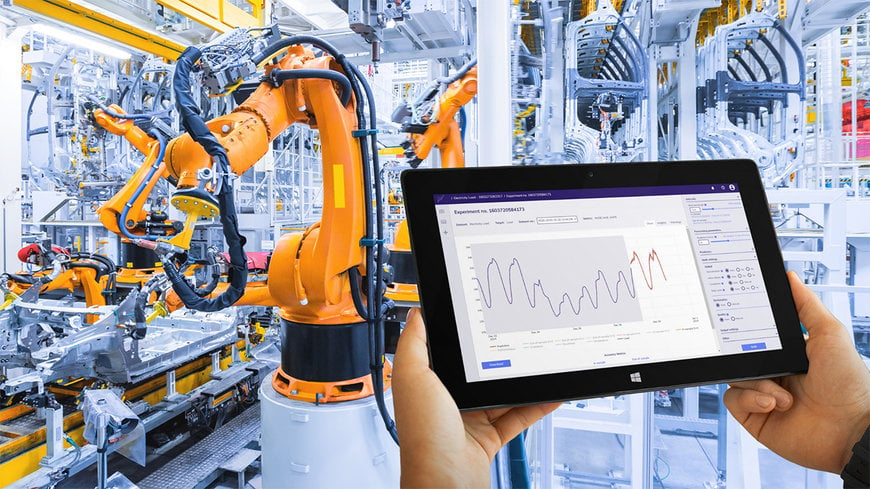
Siemens adopts Tangent Works’ InstantML technology to deliver AI capabilities. Photo credit: Tangent Works
Historically, right from the time of the first Industrial Revolution that originated around two centuries ago, to the present era of Industry 4.0, technology has helped improve production and raise efficiency to unprecedented levels in industry. But even today, it is estimated that poor maintenance strategies reduce a plant’s overall productive capacity by 5 to 20 percent; the resultant unplanned downtime in turn costs manufacturers an estimated US$50 billion each year. In fact, ‘The True Cost of Downtime’, a report released by Senseye, the leading global company for automated machine health management, estimates the direct and indirect costs of unplanned downtime to major manufacturers is up to a staggering US$1 trillion! These figures underline the importance of sound maintenance practices in industry today.
Maintenance of industrial machinery and equipment traditionally falls in three categories – reactive maintenance where assets are run to failure; preventive maintenance where the emphasis is on preventing problems before they occur; and predictive maintenance which goes a step further to predict or anticipate problems and take planned remedial action that increases plant reliability. Each of these three maintenance strategies has its advantages and disadvantages. Essentially, a company may adopt different types of maintenance services based on the value of assets as well as the seriousness of the situation should a breakdown occur. Most modern manufacturing plants have long abandoned the practice of reactive maintenance in favor of preventive maintenance and are now moving towards predictive maintenance. Since predictive maintenance monitors asset condition in real time and enables corrective actions before failures disrupt production, it is generally considered to be the most advanced and intensive type of maintenance. In other words, in the manufacturing ecosystem, predictive maintenance is now increasingly adopted as a strategy for dealing with unplanned machine downtime.
Predictive maintenance monitors asset condition in real time. Photo by Anton Dmitriev on Unsplash
Predictive maintenance
There is no clear record of the origins of Predictive Maintenance (widely referred to as PdM) in industry, but it has been prevalent in some form or other for several decades now, with automation and use of sensors facilitating what is known as condition monitoring. Some accounts mention that predictive maintenance began with condition-based maintenance, and attribute it to CH Waddington, who was a biologist assigned to the UK's Royal Air Force during World War II. It was his observation that planned maintenance actually increased breakdown in aircraft (termed Waddington Effect) that led to the concept of PdM based on condition monitoring, which dramatically increased aircraft availability. Others believe that though PdM existed in some form or other, it was only adopted widely from the 1990s by the manufacturing industry.
What exactly is condition-based monitoring on which predictive maintenance is based? Condition-based monitoring may be defined as a strategy that makes use of sensors and other tools to continuously monitor the condition of machines and assets to determine their ‘health’ and predict their condition to decide when is the right time to intervene with maintenance, without disrupting the regular production schedule. There are various types of sensors that record a wide range of data, such as sound/noise, temperature, pressure, vibrations and even conductivity, which enables an engineer to predict the failure of an asset while allowing it to be repaired or replaced in advance, before a breakdown occurs. Predictive maintenance helps maximise the life of an asset and reduce maintenance costs and equipment downtime. As a result, it finds extensive applications in manufacturing, energy and utilities, aerospace, defense, transportation and logistics, and healthcare industries worldwide. Used effectively, predictive maintenance increases manufacturing efficiency, saves on maintenance costs, and contributes to a healthy bottom line.
The PdM market size
If one looks at the Google search result for predictive maintenance market, it shows a large number of reports with wide variations, depending on the scope and segments covered by the research agency. Some of these reports cover the entire spectrum, including utilities apart from all industry segments, which explains the variation. However, one thing is common across all these reports; the CAGR is in the range of 20-30%, which indicates a very rapid growth. For the purpose of this article, the report pertaining to the manufacturing segment makes better sense. According to a research report released by ResearchAndMarkets.com in early 2020, the global market for Predictive Maintenance for Manufacturing Industry, which was an estimated US$1.2 Bn in the year 2020, is projected to reach a revised size of US$3.9 Bn by 2026, growing at a CAGR of 21.4% over the analysis period.
This healthy growth in the PdM market is characterised by three trends:
- The intense competition in the manufacturing industry is forcing companies to exploit all avenues of increasing productivity and efficiency of their operations, and effective asset performance management is among the top priorities.
- Most companies are now in the process of digital transformation of their operations where maintenance is getting a technology led makeover with use of advanced data capturing and analytics tools that facilitates end-to-end integration of PdM with the entire lifecycle of the industrial plant.
- Stringent workplace safety regulations and growing emphasis on occupational safety norms coupled growing awareness among the tech savvy workforce.
Among the leading vendors of technologies catering to PdM are global MNCs like General Electric Company, IBM Corporation, Siemens, ABB, Robert Bosch, Rockwell Automation, Schneider Electric SA, Dassault Systèmes, Software AG, Accenture plc, Cisco Systems, Hitachi, Honeywell, Microsoft, and Oracle Corporation, not necessarily in the same order.
Speaking about the Indian market, Preshit Murudkar, Managing Director & CEO, Comau India Pvt Ltd, confirms the general growth trend. The “India Predictive Maintenance Market if considered in a holistic way is a big market and is growing at a CAGR of 25%. It is expected to reach US $ 4 Bn by 2026, and further with the evolution of 5G technology this will disrupt, and bring in a lot of opportunities,” he says. According to him, the market by deployment modes is divided between On-premise and Cloud, and by verticals, comprises: Government and Defense; Manufacturing; Energy and Utilities; Transportation and Logistics; Healthcare and Life Sciences; and others.
Nimish Danani, Director Consulting Services, Hitachi Application Reliability Centre, has a different set of figures, in conformity with the observation made earlier about the variations. “Going by various research and reports, the global market for predictive maintenance in the next 5 years will be about $16 Bn to $18 Bn. In the last estimate I read it is growing at about 30% CAGR. The Indian market for predictive maintenance could inch up to $4 Bn in the next 4 to 5 years growing at about 25% CAGR,” he says.
Predictive Maintenance in the IIoT Era
If predictive maintenance is generally considered to be the most advanced and intensive type of maintenance, it has further reinforced this position in the age of Industrial Internet of Things (IIoT), with data analytics adding to its reliability, making it an ideal solution. While sensors were always part of predictive maintenance practices, their modern versions are highly evolved and become intelligent, and in combination with remote diagnostic tools and analytics software, make predictions even more accurate than ever before. In effect, predictive maintenance relies mainly on the data gathered by sensors and analysed to get insights that facilitate early fault detection.
With IIoT, every machine or equipment in the plant is equipped with internal sensors for constant monitoring of running status. This real-time data collection, analysis and simulation provides insights on equipment performance, based on which maintenance schedules are planned, without interrupting regular production. But how effective is data analysis in making the correct diagnoses without missing anything of critical importance? Sensors typically collect humongous amounts of data of which almost all is of routine nature. The anomalies are hidden in a fraction of this data. So in the end it boils down to the quality of data analytics, which opens the doors for artificial intelligence (AI).
Role of Artificial Intelligence in Predictive Maintenance
Artificial intelligence has wide applications in industry in the IIoT era thanks to its ability to make sense of the mountains of data generated by various sensors and devices. In ‘The True Cost of Downtime’ report quoted at the beginning, Senseye has demonstrated how by implementing AI-driven machine-health monitoring and predictive maintenance across large industrial organisations, it is possible to reduce levels of unplanned downtime by 50% and recoup investments in this technology in less than three months. In fact, predictive maintenance has been enriched and enhanced by the use of AI-powered algorithms which sift through the datasets gleaned from equipment history and maintenance logs. In a 2019 article published in Harvard Business Review, McKinsey partners Michael Chui, Nicolaus Henke, and Mehdi Miremadi have stated that in manufacturing, the greatest value from AI can be created by using it for predictive maintenance, thanks to its ability to process massive amounts of data, including audio and video, which means it can quickly identify anomalies to prevent breakdowns, whether that be an odd sound in an aircraft engine or a malfunction on an assembly line detected by a sensor.
Dassault Systèmes offers its 3DEXPERIENCE® platform to manufacturers which contains a suite of collaborative digital solutions to boost workforce optimisation. The company believes manufacturers have only begun to capitalise on artificial intelligence (AI) and machine learning (ML) capabilities on the factory floor today, for driving overall equipment effectiveness (OEE), optimising processes and creating a pivotal role in predictive maintenance. “AI is required for effective predictive maintenance. With it, manufacturers can evaluate multiple inputs like usage, vibration and noise directly from the machine, compare that to historical events and forecast when a machine failure is likely to occur. It then schedules the appropriate maintenance activities at the last reasonable moment before the expected failure,” states Mike Bradford, DELMIA Strategic Business Development, Dassault Systèmes.
Global technology giant ABB, which uses its Ability platform for Predictive Maintenance of assets ranging from turbines to compressors and diesel driven generators to motors, is also using AI in what the company calls a hybrid approach that combines domain knowledge with machine learning algorithms. According to ABB, merely collecting data to detect anomalies is not enough because forecasting maintenance is not straight-forward. To effectively schedule maintenance, it is necessary to predict how a detected abnormal condition is likely to develop in the future. The innovative hybrid approach follows a three-pronged process:
• Condition monitoring that can provide early detection of faults
• Identification of specific failure mode(s) related to the fault detection, and
• Quantification of the extent of fault development to support maintenance planning.
ABB’s innovative hybrid approach provides them with the basis to predict future conditions. Photo credit: ABB
Other technology companies are also riding the AI bandwagon when it comes to predictive maintenance. In January 2022, Siemens MindSphere® unveiled its first artificial intelligence application for industrial IoT called ‘AI for Everyone’, developed using the TIM InstantML technology from Tangent Works, a Belgian company. TIM, or Tangent Information Modeler, is an automatic predictive model building engine that automates the forecasting and anomaly detection process by analysing time series data and generating accurate models based on the patterns it detects. The aim of this new application is to reduce the technological barrier to powerful machine learning and AI tools. This no-code approach will allow people across manufacturing organisations to make informed decisions on future actions. “Thanks to the integration of Tangent Works’ InstantML technology, Siemens customers and partners can now better turn data into real and actionable insights and value. With the ability to use AI/ML to generate hyper-automated predictive analytics, even citizen data scientists can leverage data and achieve immediate insights, at scale. This ultimately reduces complexity and puts the power of IoT data in the hands of the user,” stated Raymond Kok, Senior Vice President of Cloud Application Solutions @ Siemens.
Schneider Electric, the global leader in the digital transformation of energy management and automation, has also demonstrated the use of AI-powered services through its EcoStruxure platform. It has documented a use case of the Nestlé Al Maha factory in Dubai of how the EcoStruxure technology evaluates data in real time from the plant’s electrical equipment and uses cloud-based predictive analytics to identify and resolve potential faults. With its open, scalable architecture, the EcoStruxure platform connects to smart devices across the electrical system and integrates with process control systems and enterprise data platforms. Data is analysed by cloud-based algorithms, and the solutions provide insights into equipment health and suggest predictive maintenance schedules, allowing for a proactive approach to asset management.
The Nestlé Al Maha factory in Dubai uses technology from Schneider Electric for predictive maintenance. Photo credit: Schneider Electric
Comau, the Italian company, offers In.Grid, an innovative networking platform that combines digital and physical worlds through sensorisation, data analysis and real-time monitoring of equipment, systems and production lines. The data collection, processing and connectivity is done at a machine level, line level or plant level, while the data analysis platform with its high-level algorithms, AI capabilities and storage features can be hosted at the plant itself, at an external data center or on a private cloud. “Our In.Grid platform is aligned with market needs from IIoT or Industry 4.0 point of view from both critical aspects. For End Product Traceability, the In.Grid MES solution is one of the flexible solutions using the latest technology of docker & microservices not only scalable but also portable, upgradable. This includes features starting from flexible User Management, Product Configuration, Flexible Connectivity with any device, Production Planning, Quality Data Traceability, Alarm Management, Cycle Time Analysis, OEE and ANDON,” says Murudkar. In its other role for Maintenance of Plant and Machinery, the In.Grid platform is easily configurable for monitoring and predicting health of the machines which are critical to avoid unplanned breakdown. “Features like Digital A/PM (similar to G-Calendar), Predictive Analysis with CBM Alarms (auto learning configurable and customisable algorithms), Machine Alarm Analysis, real time monitoring of health and alarms, make it ideal to leverage the power of Industry 4.0 in a cost-effective and highly efficient manner,” he adds.
So whether it is GE and its various predictive maintenance technology platforms for different sectors, or Rockwell Automation’s Predictive Maintenance as a Service offering that leverages FactoryTalk Analytics and apply machine learning technology, a variety of companies offer solutions in the predictive maintenance space. “From established large players to start-ups who have specific products, solutions, platforms for helping companies implement predictive maintenance solutions, thereby reducing downtime, improving yield, profitability and uptime for suppliers,” says Nimish Danani.
Optimising asset utilisation with Predictive Asset Maintenance. Photo credit: Rockwell Automation
While established companies are all well entrenched in this space, there are the proverbial new kids on the block – the start-ups – that are now creating a niche with their boutique offerings of hardware and software solutions, or a combination of both. One such company is Infinite Uptime, which began product development in 2017 and entered the market with a solution in 2020. “As markets matured to the Industry 4.0 reality, more and more manufacturing industries realised the potential impact of predictive analytics and IIoT in their manufacturing operations. We had to quickly scale our teams to meet the global demand and maximise our reach and serviceability for our customers,” says Dr Raunak Bhinge, Founder and CEO – Infinite Uptime. The company has since added 190+ manufacturing clients across 14 industry segments across the world, as their Digital Transformation and Reliability Services partner. To date, it claims to have digitised more than 750 plants, saving 6300+ hours of downtime which has resulted in more than USD 20 Mn being saved by the businesses.
Nanoprecise Sci Corp is another start-up that specialises in the delivery of comprehensive, cloud-based solutions for the lifecycle monitoring of equipment, using IoT, AI and Data science applications. This automated predictive maintenance solution provider offers an integrated AI-based solution that consists of a unique 6-in-1 IIoT sensor and an AI-based automated analytics platform. The wireless IIoT sensor measures Vibration, Acoustics, RPM, Temperature, Humidity and Magnetic Flux. The analytics platform utilises advanced signal processing algorithms to analyse the 6 streams of data in real time for predicting the remaining time to failure. The company was recently awarded first place in the Mobility and Automobile Innovation Lab (MAIL) programme by Maruti Suzuki India Limited (MSIL), India’s largest automobile manufacturer. The programme offers tech start-ups with digital innovations an opportunity to do a Proof-of-Concept project with Maruti Suzuki India Limited. “It can be very difficult to monitor the condition of various machines, especially when it involves cyclic-operations. With our AI-based solution, automobile manufacturers can rely on an automated system to monitor the health & performance of machines and equipment sets in near real-time. It offers the capability to detect minor changes in their operational parameters, monitor progression, and provide insights before they impact production or cause downtime,” stated Prashant Verma, Co-founder & Product Head, Nanoprecise Sci Corp.
Automated, sensor-based predictive maintenance solution from Nanoprecise. Photo credit: Nanoprecise Sci Corp
Future trends
With so much at stake, predictive maintenance, which has made rapid strides in recent years aided by emerging technologies, would be an essential component of maintenance strategies for most companies. Speaking about the most prominent emerging trends, Nimish Danani is of the view that with adoption of predictive maintenance, there is a lot of data being collected, analysed and AI applied to build models to start predicting failures and forecast more accurate maintenance updates.
“Based on our experience and exposure within the Automation industry the following features are the most sought after,” says Preshit Murudkar, listing them as:
- Data Traceability
- Predictive Analysis & Maintenance
- Remote Analysis & Maintenance
- Customised reports and charts, and
- OEE & ANDON.
Going forward, the sector will see increased investment in predictive data analytics based on AI and ML to minimise downtime and maintenance costs. While adoption of IoT is also a given, digital twins and AR/VR/XR are other emerging technologies that will feature prominently in predictive maintenance. Finally, more vendors would offer ‘Predictive Maintenance as a Service’ like Rockwell Automation, to make it easier for the user industries to benefit from a single source solution.