STRATASYS ADVANCES SHIFT TO ADDITIVE MANUFACTURING AT SCALE
Stratasys Ltd. (NASDAQ: SSYS), a leader in polymer 3D printing solutions, highlighted today at the RAPID + TCT Show solutions for advancing additive manufacturing at production scale, including new innovative material offerings, an expanded software partner ecosystem, and the availability of new polymer 3D printing systems for the U.S. market.
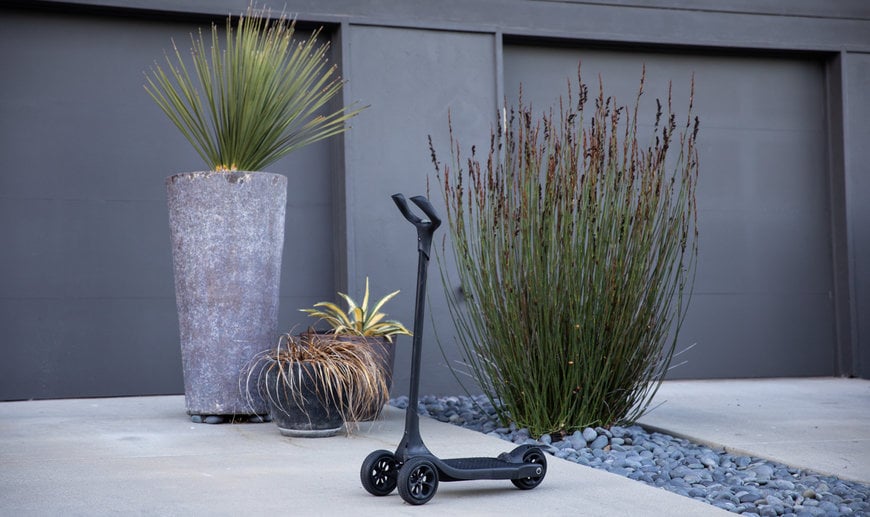
Kick scooter printed with Stratasys Dura56 by LOCTITE
- New systems for the entire product value chain to be highlighted at the RAPID + TCT Conference
- New software partner and 3D printing materials help bring additive manufacturing to the factory floor
“We are at the forefront of the shift to full-scale additive manufacturing, powered by 3D Printing, with our best-in-class solutions for the entire product value chain,” said Stratasys Americas President Rich Garrity. “That’s why every system in our booth introduces innovation well beyond our offering at the last RAPID conference in 2019. Our systems are supported by the broadest materials ecosystem, Industry 4.0 software strategy, and our best-in-class industry expertise of over 30 years.”
Expanded material options for new manufacturing systems
Stratasys continues to expand its ecosystem of materials to offer customers a variety of options across 3D printing technologies and solutions. Today the company announced new materials for the Stratasys H350 and Stratasys Origin One 3D printers and a new Origin® Open Material License (OML) for the Origin One.
The SAF powered Stratasys H350 3D printer is specifically designed for the mass production of end-use parts with consistency, and the ability to customize and control the production workflow. The H350 will initially utilize High-Yield PA11, a sustainable material derived from 100% bio-based castor beans. In addition, in 2022, PA12 (also known as Nylon 12) will be available for the H350. PA12 provides dimensional stability, chemical resistance and impact strength, and has been used across various additive manufacturing printing technologies for creating jigs and fixtures, tooling, and functional end-use parts.
Stratasys has further expanded its ecosystem of materials with two new materials by Henkel for the Stratasys Origin One. Stratasys Dura56 by LOCTITE® is a durable, impact-resistant photopolymer with exceptional surface finish and a low cost per kilo. The material was created to address applications with high material consumption and for functional applications where aesthetics and robustness are critical. Dura56 is ideal for end-use parts such as housings, parts with mating features, or class A surfaces.
“Together with Stratasys, we are delighted to introduce the new Dura56 material which is formulated to meet the specific needs of Stratasys’ customers and to provide print technicians with greater efficiency,” said Cindy Deekitwong, Global Head of Marketing at Henkel’s Loctite, a global leader in industrial adhesive solutions. “Together we will continue to drive innovation and deliver high-performance photopolymers that will allow engineers to realize the full potential of using additive manufacturing for end use parts across a wide range of industries.”
The second material for the Origin One printer is LOCTITE® 3D IND405 Clear, a one-part semi-rigid 3D printable clear photopolymer resin that provides smooth surface finish, good impact resistance and elongation. Parts printed in IND405 can be polished to an optically clear finish. The material can be machined, tapped and polished, and is ideal for microfluidic devices as well as guide overlays. Its qualities are most comparable to unfilled polypropylene.
Stratasys is also introducing the Stratasys Origin Open Material License (OML) for the Stratasys Origin One system, which is expected to ship this year. With the Origin OML software toolkit, advanced print users and material companies will be able to develop, beta test, and experiment with custom workflows and new materials. OML users will have the ability to override light, temperature, force, velocity and pressure on a layer-by-layer basis for ultimate control over the print process. The OML is designed to help materials companies and super-users accelerate iterations of material formulations and push products to market in weeks, not years.
Supporting Industry 4.0 with a growing software ecosystem
The GrabCAD Software Partner Program has added eight software partners so far in 2021, enabling Stratasys customers to integrate additive manufacturing into their Industry 4.0 initiatives. Stratasys today announced the newest addition to the GrabCAD Software Partner Program - AMFG.
AMFG, a leading provider of Manufacturing Execution System (MES) and workflow automation software for additive manufacturing, has partnered with Stratasys to deliver advanced AM solutions that combine AMFG's workflow automation expertise with Stratasys’ 3D printers and GrabCAD software. AMFGs software solution enables connectivity across the production workflow, streamline processes, and provide greater levels of traceability and visibility. Further, the combination of Stratasys 3D printing solutions with AMFG’s fully automated order management, routing and production scheduling tools enable fully automated end-part production at scale.
“The combination of Stratasys hardware, GrabCAD software and AMFG’s market leading AMES platform, is a game changer for AM operations looking to scale through automation, whilst increasing overall traceability, utilization, and quality,” said Danny Winn, Vice President of Growth and Innovation for AMFG. “The ability to pull data from AM systems into a centralized software solution is not just a nice to have – it’s critical for the future of scalable end-part manufacturing, especially in heavily regulated industries such as aerospace and medical.”
Transforming additive manufacturing technology
Stratasys’ latest systems are already transforming the operations of leading manufacturers. For example, Daikin Applied, a member of Daikin Industries, Ltd., designs and manufactures advanced commercial and industrial HVAC systems for customers around the world. The company is using the large build volume of the new Stratasys F770 3D printer to print batches of end-use parts for HVAC cabinets, which has allowed them to achieve a 93% time savings over purchasing custom injection molded spacers. Daikin is also using the F770 to print nozzle clamps used in Daikin test chambers, again saving time and costs over traditional manufacturing.
Daikin Applied HVAC cabinet spacers printed on the Stratasys F770
In February 2021, Stratasys announced the acquisition of UK-based RP Support Ltd. (RPS), a provider of industrial stereolithography 3D printers and solutions. This acquisition provided Stratasys customers with a new 3D printing technology option that produces high-quality parts with superior surface quality, accuracy and detail.
“With the inclusion of the Stratasys Neo in our service bureau, we can provide our customers with fast, accurate parts and prototypes, in a variety of materials, and with superior surface quality, all with little post processing on our part,” said Steve Grundahl, President and Founder of Midwest Prototyping, an additive manufacturing service bureau in Blue Mounds, Wis. “Beyond the quality and types of parts we could print, one of the things that really attracted us to the Stratasys Neo was the system simplicity for ease of use and service – everything that makes the total cost of ownership more advantageous for us.”
The Stratasys Neo Series of printers can produce concept models and prototypes with industry-leading accuracy, exceptional sidewall quality and crisp feature resolution, as well as rapid tooling and master patterns. Furthermore, the Neo Series of printers are designed with an open resin material system. This allows customers to choose the material that best suits their application.
Stratasys solutions for enabling the future of additive manufacturing at scale will be on display at the Rapid + TCT conference September 13 to 15 at McCormick Place in Chicago. During the conference, Stratasys experts will participate in speaking sessions and be on-hand in the Stratasys booth (E8201) to discuss the company’s additive manufacturing solutions for design, prototyping, production-scale parts, and the healthcare industry.
www.stratasys.com