An Introduction to Digital Manufacturing
Digital manufacturing provides them with the means to meet these demands. Visual Components is a leading supplier of manufacturing simulation software. By helping manufacturers gain a deeper understanding of their processes, our products reduce waste and inefficiency, increase capacity and enable shorter lead times. And now, as a result of our partnership with NVIDIA, simulation from Visual Components can help manufacturers shape and start on their own digital transformation.
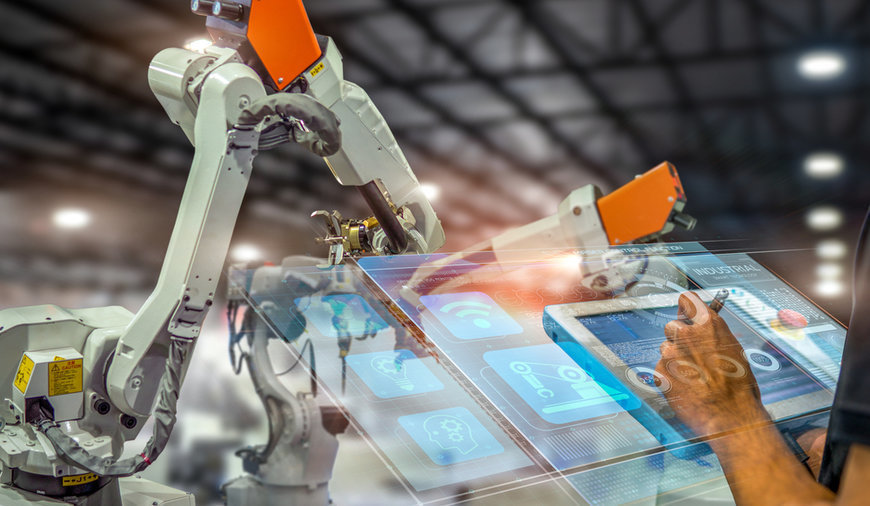
Shorter lead times, more variety, better quality – whatever it may be, manufacturers are constantly seeking ways to respond to the growing demands of customers.
What is digital manufacturing, and, more importantly, how are companies implementing it into their workflows?
To put it simply, digital manufacturing is about integrating the modern computer technologies available to manufacturers in ways that yield real improvement in key metrics.
This article will go through what it means to integrate digitalization in manufacturing, the benefits, and some suggestions for tools and ways to get started.
Individual sections address:
- What is Digital Manufacturing?
- Benefiting From Digital Manufacturing Technologies
- Digitalization in Manufacturing and Processes
- Starting the Digital Manufacturing Transformation
1. What is Digital Manufacturing?
For many manufacturers, digitization began with programmable logic controllers (PLCs) and computer numerical control (CNC). These let machines and equipment run automatically, with superior levels of control to those available from relay logic systems. Then came CAD, CAM, ERP, computerized maintenance management systems (CMMS), and more. Today this patchwork quilt of disparate technologies is overlaid with lean manufacturing, six sigma, and Quality Management methodologies.
As many industry leaders will admit, it’s a bit of a mess.
Digital manufacturing is about integrating these tools, so they work together seamlessly. Product data becomes a digital thread running through the entire manufacturing business, from design and development to distribution and even servicing. Product definition links with simulation and testing, with manufacturing layout planning and machine design, ERP, Quality, and after-sales support.
No two manufacturers are alike, and the same should be true for their implementation and integration of digital manufacturing technologies.
Each business must identify their goals and priorities and plan their own digitization path. Some will focus on cost reduction through labor productivity, others will strive to reduce lead times, and many will look for ways of handling increased product variety and the growing demand for customization.
In their “Smart Factory Study,” Deloitte describes manufacturing digitization in terms of smart factory initiatives. Some of these employ the Industry 4.0 technologies of sensors, communication capabilities, and analytics. Others relate to simulation, visualization, and tools for collaboration.
The Deloitte report lists ten areas where these technologies can be applied. We would summarize them as follows:
- Advanced manufacturing technologies – additive (a.k.a. 3D printing) is seen as having great potential
- Sensor technologies and analytics – for monitoring quality, energy usage, and equipment performance, identifying trends, and targeting
- Improvement efforts
- Product engineering – design, simulation, creation of digital twins, and modeling of virtual manufacturing processes and equipment
- Smart material handling and warehousing – manufacturing robots, autonomous mobile robots, automated storage, and retrieval systems, smart conveyors and smart picking technologies
- Superior decision-making tools – command centers, manufacturing simulation, smarter scheduling with the ability to optimize and adapt on-the-fly
2. Benefiting from Digital Manufacturing Technologies
Disparate computer systems, or worse still, no computer systems, mean more time spent reviewing, parsing, and entering data. That’s why so many operations and processes are still managed primarily through spreadsheets and have minimal ability for analysis and planning. It’s slow and wasteful, and it’s also an opportunity for errors to creep in.
Integrating digital manufacturing technologies cuts this waste, leading to immediate, quantifiable savings. In the report referenced previously, Deloitte found smart manufacturing initiatives:
- Enabled increases in output by 10%
- Raised capacity utilization by 11%
- Lifted labor productivity by 12%
The reality is, though, that these gains are just the tip of the iceberg. The benefits from digital manufacturing go much deeper and are much more impactful (although perhaps harder to quantify).
Creating that single digital thread throughout the factory, from the design office to the warehouse, generates opportunities to do more than has previously been possible and to do it better.
In product development, the digital twin enables simulation and refinement before making a single physical item. Then it’s fed into the design of manufacturing equipment, which can also be designed, simulated, and even commissioned virtually.
The factory itself is modeled and optimized virtually. This allows for evaluating more alternatives and, ultimately, a more efficient layout. Then, as issues arise or orders are received, this digital factory enables faster decision-making, leading in turn to better resource utilization. And finally, when the customer needs help with servicing or staff training, the digital twin makes that easier and more effective too.
3. Digitalization in Manufacturing and Processes
A closer look at what digitalization means and what it can do throughout manufacturing will illustrate applications and potential pitfalls.
Pitfalls, which result in a failure to realize anticipated benefits, usually arise from deploying the wrong tools. This, in turn, starts with not identifying goals for the digital transformation. Only by starting with the end in mind is it possible to determine what’s needed and useful and what isn’t.
As part of this, it’s important to understand the function and capabilities of the tools being considered and to plan and accurately manage their implementation. Three areas that warrant a closer look are:
- Simulation
- Smart manufacturing
- Factory digitization
The role of simulation in avoiding costly mistakes
Simulation is applied to products, machinery, and equipment and to factory layouts. In product engineering, simulation verifies that designs will perform as intended, reducing the amount of testing and number of changes needed.
In manufacturing, the operation of any machine or piece of equipment can be simulated. And in production, it’s possible to simulate cells, lines, and even complete factories.
Simulation is a tool for identifying design or layout aspects that don’t work as intended or expected. It ensures products perform correctly and so minimizes customer complaints and warranty returns. In the factory it allows early detection of mistakes in equipment design and process layout, before they become too costly and disruptive to put right. (Or in some cases, the cost of making changes is so high the business chooses to accept the constraints unintentionally imposed.)
Simulation can also be used to create a digital twin for virtual commissioning of new equipment. This is where, once designed, machine operation is tested in order to find any faults in control logic or elsewhere. It is also an opportunity to start training people who will be working with the equipment. Any problems can be corrected quickly and start up time is reduced.
Smart digital manufacturing
Industry 4.0, the fourth industrial revolution, is about exploiting low cost sensors, communications technologies and analytics to improve quality, raise machine uptime and save energy. Applications range from machine monitoring to adaptive processes and raising efficiency in motor and pump operation.
Machine monitoring can be as simple as tracking current drawn, or include more sophisticated statistics and metrics about cycle times, production rates and material yields. Machine condition data, especially when monitored for trends, can guide predictive maintenance efforts that reduce breakdown frequency and increase availability. Adaptive, or “smart” processes are those where a machine monitors critical aspects and makes adjustments to reduce variability. This raises quality through increased consistency and reduces waste. Quality is also addressed through automated inspection systems. Cameras with machine vision software are one tool, but gauging and detection of hidden defects, (by ultrasound or x-ray,) are other approaches.
Smart machines and equipment can also monitor and manage their energy consumption. Air compressors for example are able to switch into low energy modes when demand drops, but wake up quickly when needed.
Factory digitalization
A 3D simulation provides a virtual representation of a physical manufacturing system. This is used as a planning tool, and also as a decision-support tool. In both cases it’s useful to validate the model by importing actual production schedules and comparing model results with those observed in the real world. A digital twin takes this concept further by maintaining full equivalence with the real-world system. This can involve feeding the simulation with actual machine data, such as that obtained from machine monitoring. Uses of this digital representation of the factory include:
- Evaluating alternative production schedules
- Investigating ways to address capacity constraints
- Reverse engineering problems to obtain insights into their origins
4. Starting the Digital Manufacturing Transformation
Most manufacturers have parts of a digital transformation in place. What they need to do is put it all together. This will undoubtedly involve difficult decisions, many about legacy systems, and spending money. However, there’s also a danger that the apparent scale of the challenge brings about a kind of inertia. To address that, we suggest the following steps:
- Focus. Rather than trying to digitally transform the entire operation, pick an area where digitalization will have a significant, and very visible, impact.
- Establish where you stand right now. Audit the tools in use, and look at those you’re not currently using. Additive manufacturing and robotics may be examples.
- Define your goals. Are you trying to cut costs, reduce time to market, increase flexibility, or is there something else?
- Look at product data. Is this suitable for use as a common source of truth throughout manufacturing?
- If you’re not already using simulation, begin looking for products that will support your digital transformation. If this is a technology you already use, explore whether what you have can scale and integrate with the other tools in current or future use.
Simulation Software from Visual Components is Helping the Manufacturing Industry Digitally Transform
Digitalization in manufacturing is a complex topic and every manufacturer must determine what’s right for their business. For this reason, 3D manufacturing simulations have become a staple in helping manufacturers analyze, plan, optimize and improve factory layouts, machinery and organization.
Simulation involves three distinct stages:
- Create a virtual representation of a real-world machine, process or system
- Validate the model with real-world data, and make adjustments to suit
- Use the model to explore hypotheses, evaluate competing scenarios, find problems and develop solutions
To better understand how you can benefit from 3D simulation in the manufacturing process, below you will find a video featuring some of our experts taking you through the Visual Components software and how it can help you get started on further digitizing your manufacturing processes.
www.visualcomponents.com