www.magazine-industry-usa.com
21
'21
Written on Modified on
Under the surface
Non-destructive testing of composite materials
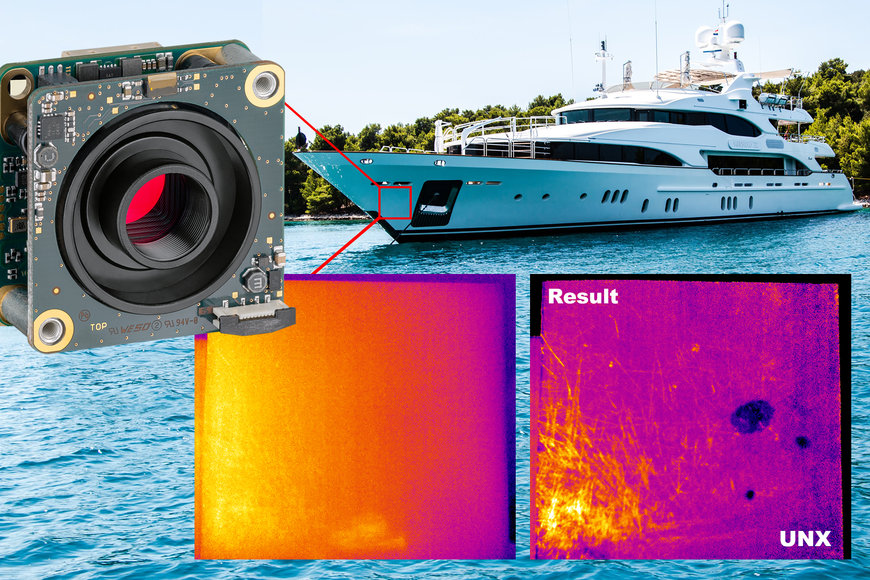
In yacht and boat building the most commonly used materials are the so-called composites. By cleverly combining the positive properties of at least two components, they often have outstanding features - some of them even specially adapted to their respective areas of application. It is hardly surprising that they are also used for high-performance applications in the aerospace industry, in power engineering, e.g. for wind turbines, in medical technology, in sports equipment manufacturing and in the automotive industry. However, wherever there are bindings, these can also "break" - be it through external influences or material fatigue. Regular tests are therefore indispensable. The iX-600 portable inspection system from UNX Technologies Co., LTD. Taiwan provides contactless inspection of multilayer composites, even for large surfaces. It uses image processing to detect weak points that are invisible to the human eye. In addition to a thermal imaging camera, a uEye board level camera with autofocus from IDS Imaging Development Systems GmbH is used.
Especially, in maritime applications the demand for composites is continuously increasing. In addition to floor elements, side walls, ceiling panelling or doors, also toilet compartments and separation units made of composite materials can be supplied. Moreover, load-bearing parts such as floors, walls or roof panels are possible and provide considerable weight savings. A classic example of a composite material used here is CFRP - carbon fibre reinforced plastic. It has a high stiffness and is very light at the same time. Or also GFRP - glass fibre reinforced plastic, a material made of plastic and fibreglass. It is cost-effective and yet very high quality.
With such lightweight construction materials, the individual components are not combined into a single material, but exist virtually side by side. Therefore, damage such as bubbles, pores, foreign inclusions and delamination (peeling off of layers) can occur due to manufacturing processes. Even during operation, i.e. while the vehicle is moving, the strength of the material can be impaired, for example by an impact event. An impact against a composite panel can leave no visible damage on the outside. Inside, however, it will still lead to a reduction in compressive strength. Regular testing of the materials is therefore not only sensible but also vital for safety. Yacht manufacturers usually use the ultrasonic or impact-echo method to detect defects. This is based on the use of sound waves. It was developed in the 1980s for testing reinforced concrete components and is currently widely used. However, this process requires contact between the parts and is time consuming.
Application
UNX Technologies Co., LTD. Taiwan offers a real alternative. The portable inspection system iX-600 enables a non-contact and therefore guaranteed non-destructive inspection (NDI - Non-Destructive-Inspection) of composite materials. Testing can be carried out with regard to detachment, delamination or porosity. The material properties are analysed beneath the surface and thus defects in the interior of the material are detected. The system also captures large inspection areas or curved structures effortlessly - without requiring a material sample in advance. For composite materials with multilayer structures, the iX-600 can also be used in addition to the manual sequential ultrasonic scanning described above to replace point information with area information.
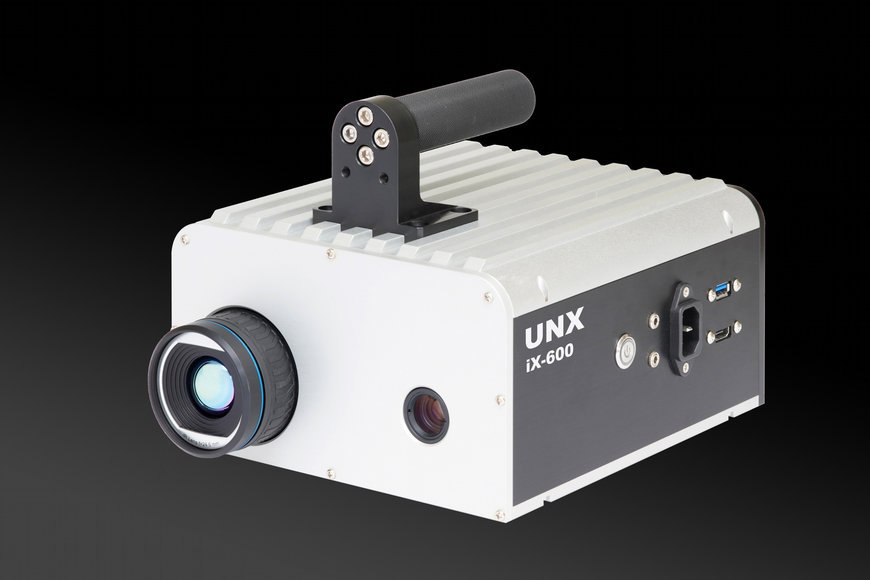
Portable inspection system iX-600
The special feature of this: The fault location can be determined quickly and precisely. In addition to the infrared thermal image for evaluating the general temperature distribution on the test surface, the UNX system receives parallel image information from the integrated industrial camera. Thus it determines the exact defect status of the material. The decisive factor is therefore the combination of an infrared camera with a board level camera with autofocus from IDS, paired with a built-in industrial computer with a 7-inch touch screen and the associated software. The instrument, patented in Taiwan, is mobile and does not require an additional external computer.
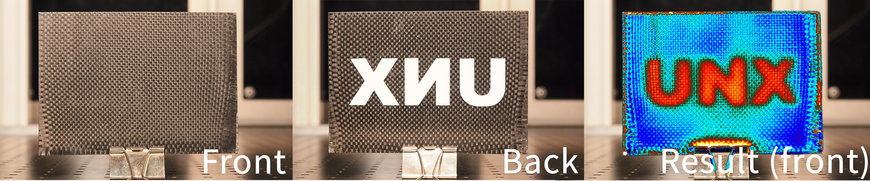
Demo recording
Using the example of the outer skin of a motor yacht, the procedure can be explained in simple terms. The board level camera records the current image of the area to be inspected exactly parallel to the thermal imaging camera during the inspection. With the help of image processing technology, the system can quickly detect defective areas by analysing and matching the image data and display their relative position. All measurement results are clearly displayed and documented in the image. The delamination defect for example (green frame in the picture) can then be easily located for repair.
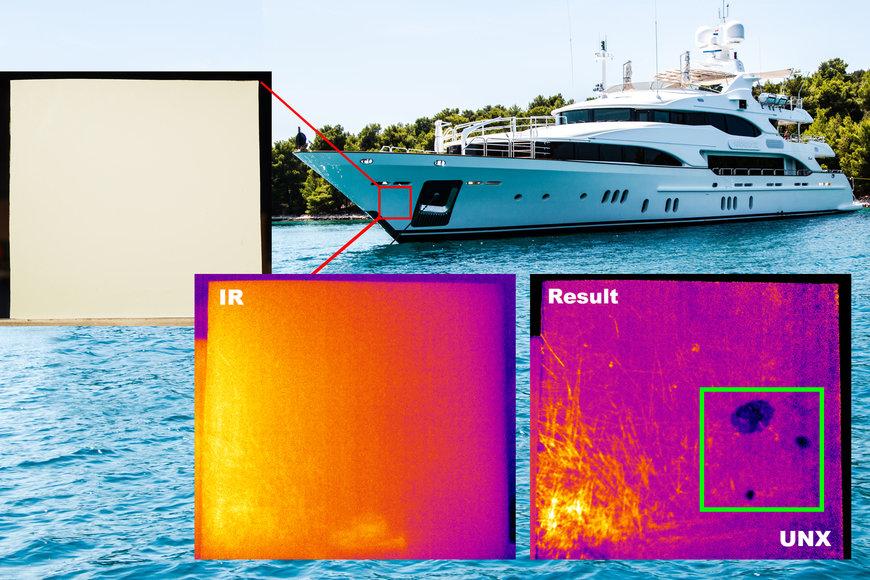
Inspection of the outer skin of a yacht
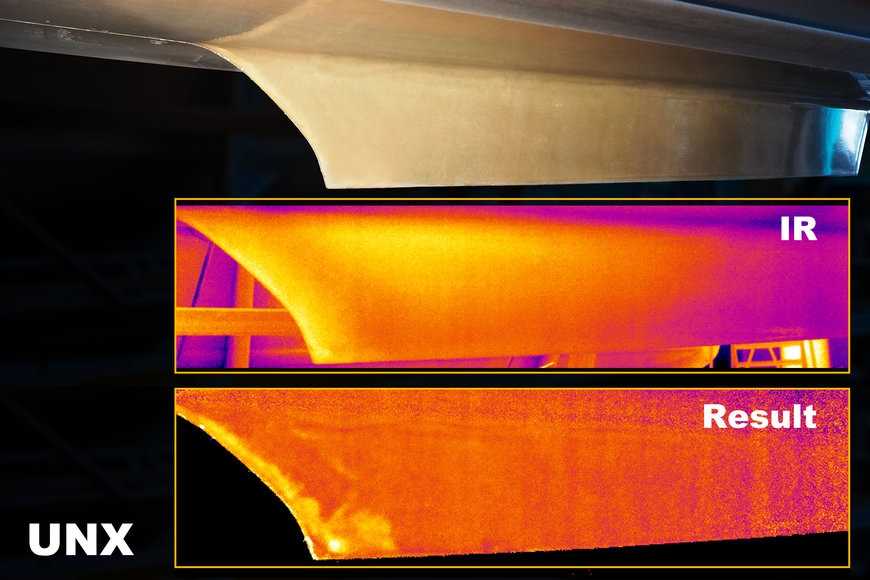
Evaluation result of the iX-600
Industrial camera with autofocus
UNX Technologies was looking for a compact camera for the mobile system that would also allow quick changes between different focal planes. "The iX-600 is a portable device. It must therefore be small and light. The same applies to its components, of course. In addition, the integrated camera must have a computer-controlled autofocus function due to the different working distances," explains Dr. Yu-An Lai of UNX Technologies.
The uEye LE AF USB 3.1 Gen 1 boardlevel camera from IDS meets all these criteria. It is suitable for the use and control of liquid lenses and offers a practical autofocus function. This allows for optimally focused images at variable object distances. The automatic system is based on an "active" liquid lens control and can be easily triggered by software. Depending on the application, the autofocus can be individually configured and ensures perfectly sharp images in no time at all. UNX has specifically chosen the model UI-3881LE AF with S-Mount lens mount. The camera is equipped with the 1/1.8" rolling shutter CMOS sensor IMX178 from the Sony STARVIS series and enables a resolution of 6.41 MPixel (3088 x 2076 px) at a frame rate of up to 58 fps. In addition to its high resolution, the sensor scores with speed and sensitivity, so that excellent images are achieved even under low-light conditions.
The UI-3881LE AF has a twist-proof USB Type-C connector as well as USB power delivery and can be easily integrated into embedded systems. Due to its compact design (36 x 36 x 20 mm) it can be installed in the smallest space and is perfectly suited for classic machine vision applications and tasks in the fields of microscopy, medical technology, metrology and traffic monitoring. It is also predestined for installation in small industrial devices, such as the iX-600 from UNX Technologies.
The Taiwanese company uses the IDS Software Development Kit to integrate the camera. IDS Software Suite is a free software package that is exactly the same for uEye industrial cameras (model designation "UI") and can easily handle a mixed operation of USB 2.0, USB 3.0, and GigE uEye cameras. In addition to the camera drivers, it contains sample programs in various programming languages such as .NET. "This shortened our development time considerably," explains Dr. Yu-An Lai.
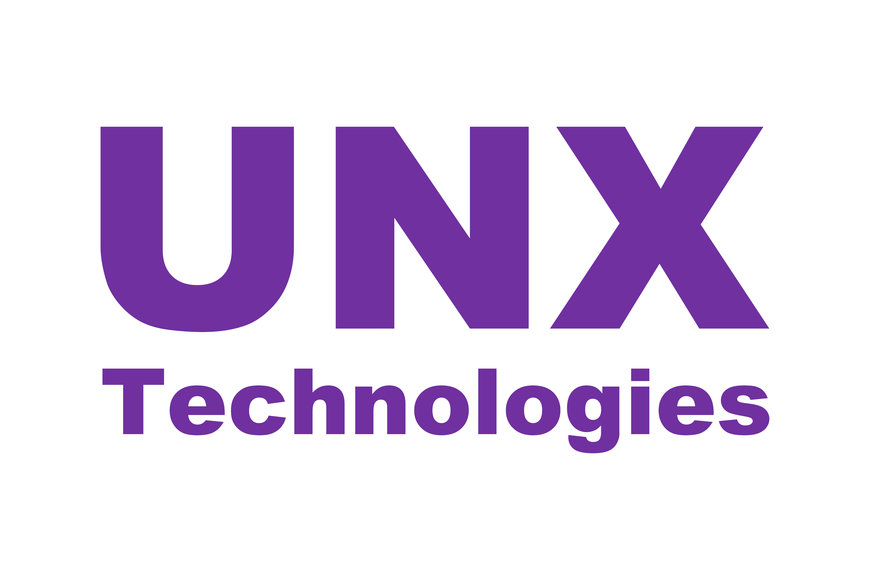
Outlook:
The iX-600 inspection system focuses on the market for non-contact and thus non-destructive testing of composite components. A market that holds a lot of potential. This is because the areas of application for composites are often sensitive. Whether in maritime applications, as described here, in space travel, medical technology or sports equipment construction - the load-bearing capacity of the materials used is essential and makes regular testing indispensable.
However, UNX Technologies is also considering applications that will require industrial cameras with higher resolution or C-mount lens connection in the future. Here the company has the "sister camera" UI-359xLE AF in mind. Just like the UI-3881LE AF model used in the iX-600, it offers the possibility of focusing liquid lenses conveniently via the camera using software. On the sensor side, however, it is equipped with a 1/2" rolling shutter CMOS colour sensor from ON Semiconductor, which delivers an extremely high resolution of 18.10 MPixel (4912 x 3684, 20.0 fps), 4K Cinema (4096 x 2304, 38 fps) and Ultra HD (3840 x 2160, 40 fps).
No matter which variant is used, the compact and powerful industrial cameras open up countless application possibilities. In mobile solutions, such as the iX-600, they make everyday work easier for the user in every regard and at the same time ensure greater safety. For those who can “see-through”, know what is happening under the surface.