www.magazine-industry-usa.com
10
'24
Written on
Modified on
SCHUNK News
SCHUNK AT THE AMB STUTTGART 2024
SCHUNK will showcase a variety of automation options, making manufacturing processes more efficient and companies fit for the future.
schunk.com
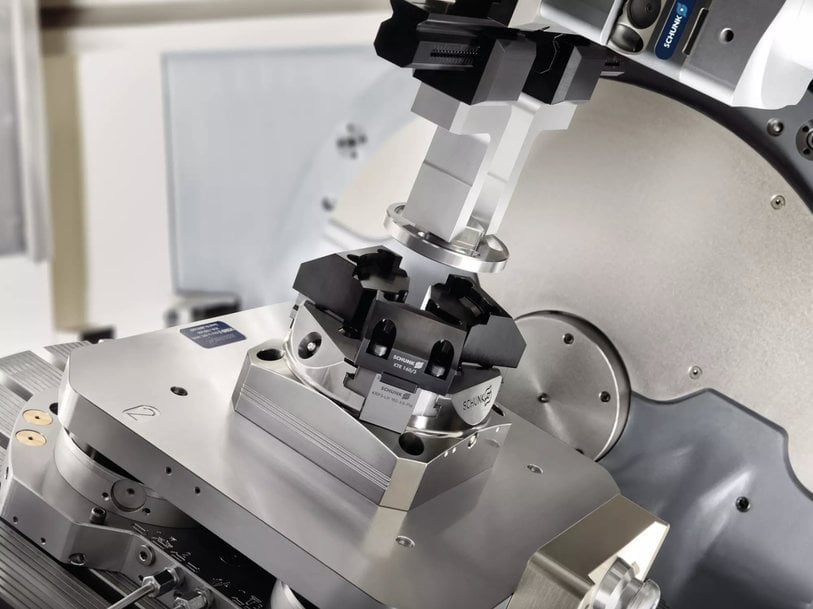
If you want to bring speed into your production, automation is essential. Innovative customized solutions are the cornerstones of healthy manufacturing in productive and economically successful companies. At the AMB (10-14 September), the international exhibition for metalworking 2024 in Stuttgart, SCHUNK will showcase a variety of automation options, making manufacturing processes more efficient and companies fit for the future. True to the SCHUNK motto: “Hand in Hand for tomorrow“.
Automation is the key to manufacturing productively and cost-effectively despite a shortage of skilled workers and cost pressure. But automation does not start in the machine. To fully exploit the machine’s productivity potential, it is essential to ensure reliability and speed even during loading and unloading. SCHUNK, the specialist in toolholding and workholding, gripping, and automation technology, offers an extensive portfolio of components, necessary for automated manufacturing inside the machine, as well as for automated parts loading and unloading. At least as important: SCHUNK supports customers with well-founded component and application know-how in the selection and construction of the individually optimal automation solution.
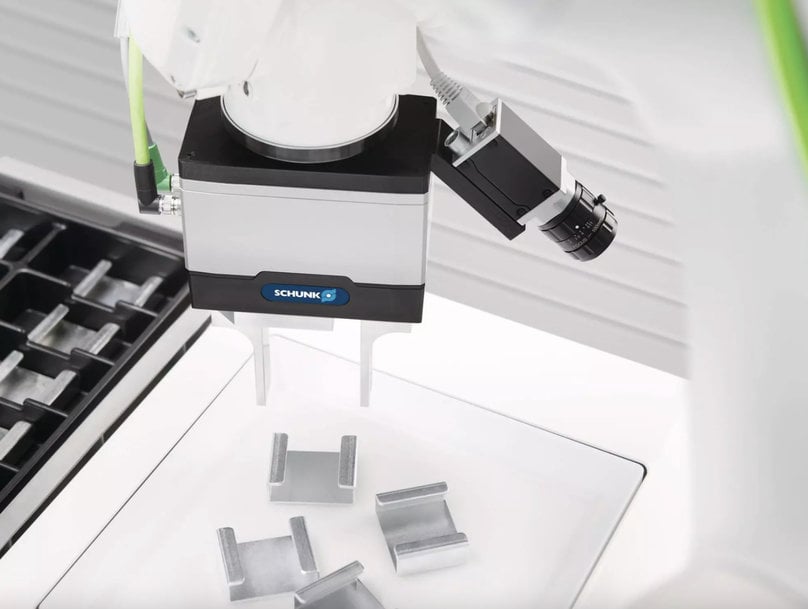
The 2D Grasping Kit from SCHUNK was honored with the HERMES Award. It enables easy entry into AI-supported handling of non-location-oriented objects. Image: SCHUNK
From simple tool handling to intelligent machining
The right automation method depends on various parameters; process chains, space conditions, lot sizes and part variances, for example, play a decisive role. At the AMB, SCHUNK will showcase diverse approaches of automated machine loading from simple entry to high-end solutions. In addition, visitors will experience vivid examples of automated workpiece handling with innovative handling solutions. The 2D Grasping Kit, for example, which was honoured with the HERMES Award 2024, enables a quick and easy introduction in the process-reliable automated handling of unsorted parts. Brand new is the mechatronic EZU centric gripper: The robust and resistant gripper is perfectly suited for harsh working conditions and handles cylindrical or eccentrically positioned workpieces of various sizes without loss of gripping force. A variety of communication interfaces, PLC function modules and plugins to renowned robot manufacturers ensure easy integration.
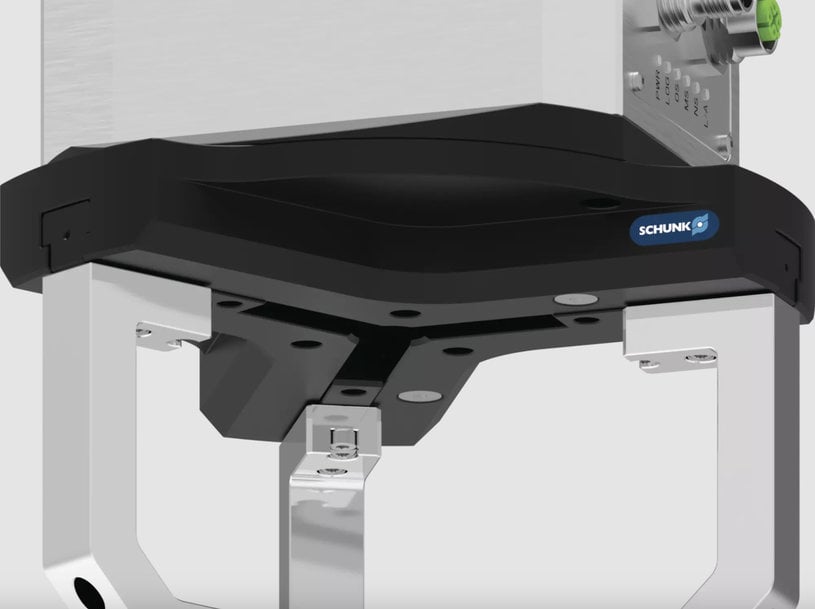
The robust, mechatronic EZU 3-finger universal gripper also works reliably in harsh environments. Thanks to many variations, it is versatile in use and easy to integrate.Image: SCHUNK
More freedom in workpiece clamping
SCHUNK also offers manual, automatic, and intelligent clamping solutions for almost any application in its product line for workpiece clamping technology. The existing product lines are continuously expanded and adapted to customer requirements. For example, with the flexible, manual 4-jaw compensation chucks ROTA-ML flex 2+2 any workpiece geometry can be clamped. The product range was revised from size 500 mm in diameter: The chuck heights were reduced up to 30 percent, and therefore the chuck weight lowered up to 40 percent. This gives users significantly more freedom in terms of size and weight of the workpiece to be machined.
With the KONTEC KS-H-LH, SCHUNK launches a compact and strong hydraulically actuated long stroke vise with an overall clamping force of 80 kN. Therefore a clamping range of 20 to 345 mm is achieved with a hydraulic clamping stroke of 110 mm. In addition, data such as path measurement or dynamic pressure can be transferred to the machine control via IO-Link.
There are also new developments in the field of magnetic clamping technology: SCHUNK has reworked the proven magnetic chucks MAGNOS MFRS and equipped them with an additional digital feature: a new ePaper status display provides the user with information about the clamping statuses “MAG ON”, and “MAG OFF” to ensure reliable clamping and maximum process reliability.
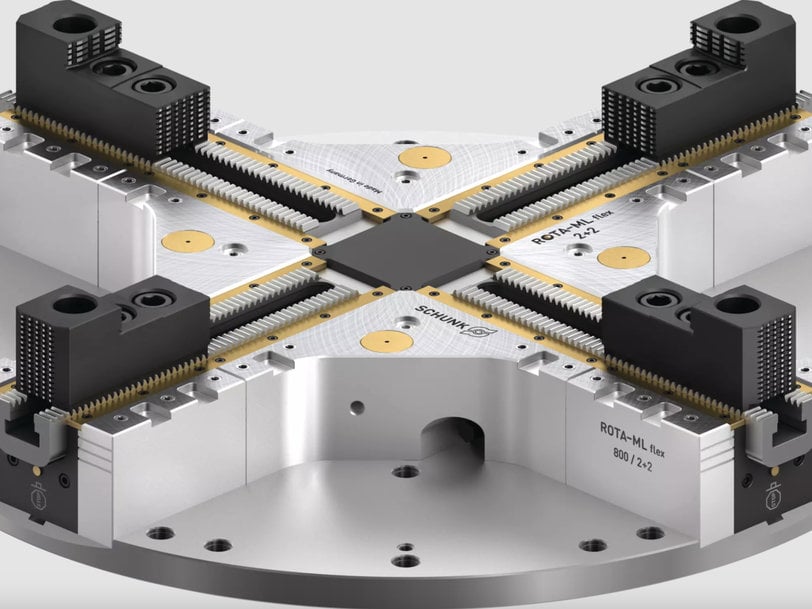
More streamlined: The 4-jaw compensation chucks ROTA-ML flex 2+2 are up to 40 percent lighter than its predecessor versions, but all the stronger. Image: SCHUNK
Intelligent process monitoring
There is also news in the field of intelligent process monitoring with iTENDO²: Its range of applications has been significantly expanded. Via the iTENDO2 magnetic holder, customers can now place the intelligent real-time sensors freely in the machine room and use them for tests and process optimization. Another hydraulic expansion toolholder is now also part of the iTENDO2 product range: The slim iTENDO² Slim 4ax in standardized heat shrinking contour also offers process monitoring options in axial and radial fine machining now. Both modules can be seamlessly connected with the basic pad version for evaluating vibration data.
These innovative automation and digitalization modules help to create a healthy and economically successful production process.
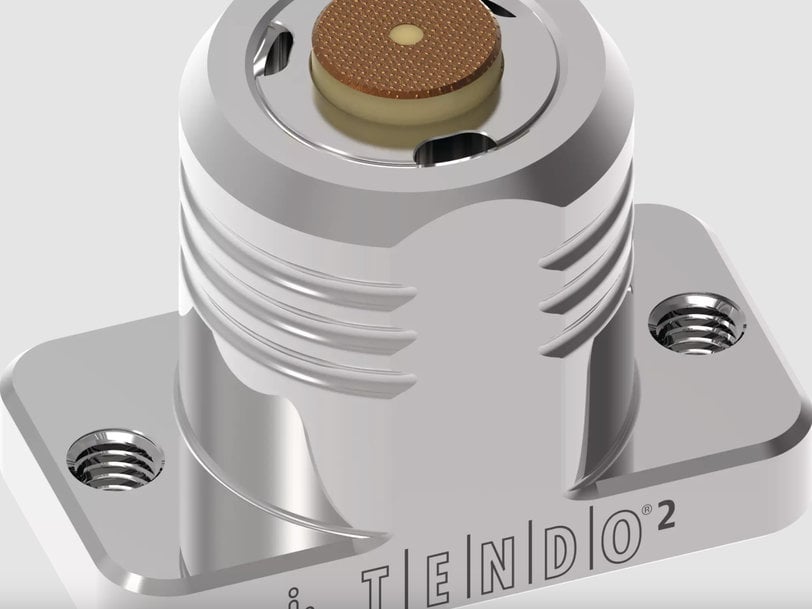
Intelligence for any application: With the iTENDO2 magnetic holder, users can now position the intelligent real-time sensors anywhere in the machine room and use them for tests and process optimization. Image: SCHUNK
Timo Gessmann, CTO of SCHUNK summarizes: “Small to medium-sized industrial companies, in particular, achieve a productivity boost with automation, which compensates for gaps in skilled labor and secures their competitiveness. At the AMB, we will show ready-made solutions, but also how we at SCHUNK are already using artificial intelligence to increase process efficiency and boost our customers‘ productivity.“
We are looking forward to welcoming you at the AMB. Please visit us in Hall 1, Booth 1G30.
www.schunk.com