www.magazine-industry-usa.com
22
'24
Written on
Modified on
Schmersal News
PROTECTING CONVEYOR SYSTEMS - WITH THE HELP OF ARTIFICIAL INTELLIGENCE
Schmersal and SHG Conveyor Control GmbH present the new belt monitoring system 'Rip Prevent+'.
www.schmersal.com
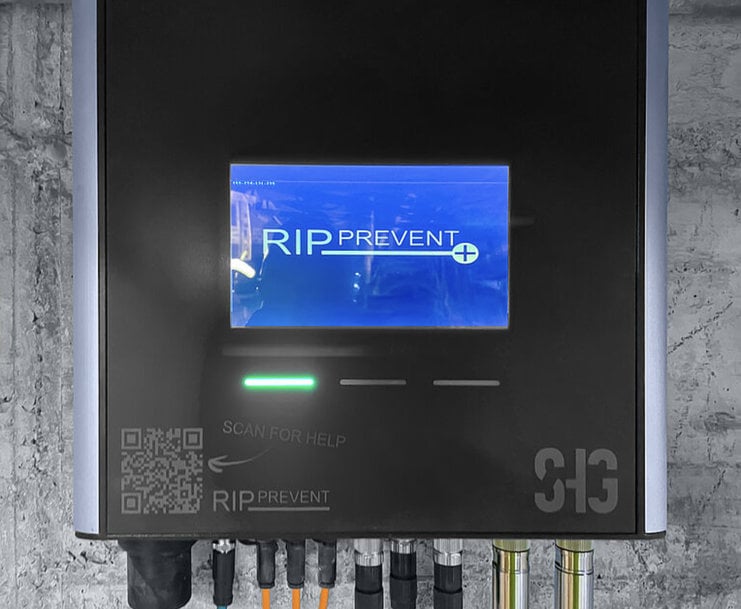
When it comes to transporting raw materials, bulk materials handling systems are the lifeline of the entire process. High availability and minimised downtimes are essential. At SOLIDS 2024 in Dortmund, the Schmersal Group and its system partner SHG - Conveyor Control GmbH will demonstrate for the first time in Hall 5, Stand 5-L06, how the efficiency of conveyor systems can be maximised with the help of predictive analytics and predictive maintenance. SHG's new 'Rip Prevent+' belt monitoring system analyses conveyor belt data using an AI-based computational model.
In the event of a rip event or anomaly, the Rip Prevent+ system generates an output signal based on conveyor-specific thresholds that the customer can implement in their PLC to automatically stop the conveyor before the critical rip event occurs. The computational model calculates the data 50 times per second and is able to send a signal to the PLC in less than a second to minimise any resulting longitudinal slot.
In addition to longitudinal crack detection and prevention, the Rip Prevent+ system offers other functions to increase conveyor system availability or to provide the user with relevant process information. These include:
- Motor monitoring
- Electrical network analysis
- Energy efficiency analysis
- Mass flow calculation
SHG - Conveyor Control GmbH is constantly expanding its functions to provide the user with a conveyor monitoring system that makes unplanned downtime almost a thing of the past.
The SHG Rip Prevent+ system can be used in mining and industrial applications to detect anomalies and cracks in all conveyor belts, including specialised belts such as corrugated sidewall belts. The Rip Prevent+ system helps customers minimise the damage caused by longitudinal rips. By stopping the conveyor when a longitudinal rip is detected, the system limits the damage associated with these events and can save customers significant costs associated with downtime, belt replacement, conveyor repair and maintenance.
HDS series belt misalignment switches for process protection
Belt misalignment switches are also used for process protection: they monitor the straightness of conveyor systems and generate a time-delayed signal if the conveyor belt is out of position. While the pre-warning signal is used to correct the belt, the stop signal is used to shut down the conveyor system.
With the modular HDS series from Schmersal, both the belt misalignment function and the EMERGENCY STOP function, designed as an emergency pull-wire switch, are integrated on one hardware platform. This makes the HDS series particularly flexible and suitable for a wide range of applications. The HDS series can optionally be connected to the Dupline installation bus, allowing the switches to be daisy-chained and diagnostic information to be easily transmitted. By transmitting status information, anomalies can be identified and faults rectified more quickly.
Visit Schmersal from 9 to 10 October 2024 at SOLIDS 2024 in Dortmund / Germany: Hall 5, Stand 5-L06
The SHG Rip Prevent+ system can be used in mining and industrial applications to detect anomalies and cracks in all conveyor belts, including specialised belts such as corrugated sidewall belts. The Rip Prevent+ system helps customers minimise the damage caused by longitudinal rips. By stopping the conveyor when a longitudinal rip is detected, the system limits the damage associated with these events and can save customers significant costs associated with downtime, belt replacement, conveyor repair and maintenance.
HDS series belt misalignment switches for process protection
Belt misalignment switches are also used for process protection: they monitor the straightness of conveyor systems and generate a time-delayed signal if the conveyor belt is out of position. While the pre-warning signal is used to correct the belt, the stop signal is used to shut down the conveyor system.
With the modular HDS series from Schmersal, both the belt misalignment function and the EMERGENCY STOP function, designed as an emergency pull-wire switch, are integrated on one hardware platform. This makes the HDS series particularly flexible and suitable for a wide range of applications. The HDS series can optionally be connected to the Dupline installation bus, allowing the switches to be daisy-chained and diagnostic information to be easily transmitted. By transmitting status information, anomalies can be identified and faults rectified more quickly.
Visit Schmersal from 9 to 10 October 2024 at SOLIDS 2024 in Dortmund / Germany: Hall 5, Stand 5-L06