www.magazine-industry-usa.com
28
'25
Written on Modified on
GreenIron adopts ABB technology to enhance circularity in metals & mining
GreenIron selects ABB's advanced control system to optimize fossil-free metal production, driving circular economy transformation, reducing CO₂ emissions, and supporting scale-up and commercialization efforts.
global.abb
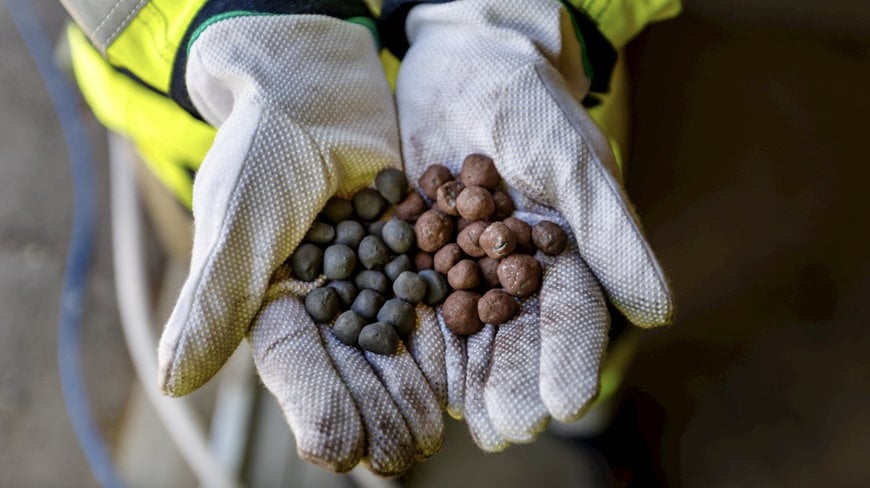
ABB's distributed control system will support the creation of fossil-free sponge iron for use in steelmaking. Image GreenIron
ABB has been selected by GreenIron, an innovative Swedish company working in the mining and metals industries with its patented materials reduction technology, to provide automation and control system solutions for a first commercial facility in Sandviken, Sweden.
GreenIron’s hydrogen-based reduction technology will be industrialized for fossil-free and energy-efficient production of metals, producing fossil-free sponge iron that can then be used in industries such as steelmaking. A single furnace is expected to reduce carbon emissions by around 56,000 tonnes per year compared to traditional coal-based methods, with the only residual product being water. Scaling up to 300 furnaces would correspond to roughly 35 percent of Sweden's annual CO₂ emissions.
The integration of the ABB Ability™ System 800xA® distributed control system (DCS) will enable the scaling up of GreenIron’s operations. The powerful automation platform will manage the entire industrial process, with the capabilities to integrate control, safety and power management into one system. It will mean overall plant visibility for optimizations, efficiencies and better decision making based on data and insights.
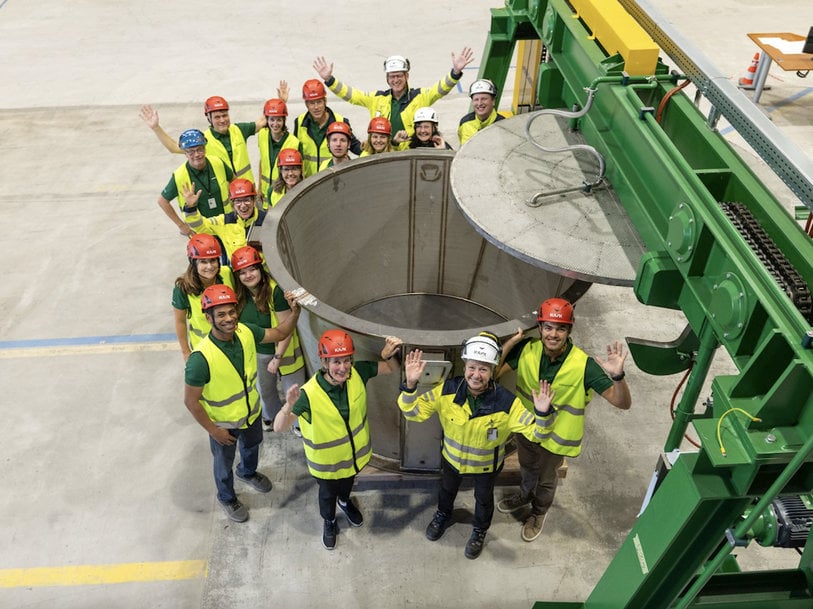
GreenIron is set to deploy its patented materials reduction technology for industrial applications. Image GreenIron
GreenIron paves the way for circular production processes by producing valuable raw materials from residual products such as landfills and residues as well as virgin ore. The sponge iron products can be used in steel or other metal fabrication processes, including electric arc furnaces, smelting plants and foundries.
“The collaboration with ABB is a crucial part of our scaling up and future growth as we commence commercial production,” said Ulrika Molander, Chief Operating Officer of GreenIron. “ABB’s system will enable us to make informed decisions, stabilize operations at every stage, and analyze data for our continued journey. It’s an exciting time for us.”
“Together with GreenIron we’re working on fulfilling sustainability objectives that are demanded by the metals industry and wider society,” said Martin Björnmalm, Local Business Line Manager for Metals, ABB Process Industries Sweden. “This is the type of project that underlines our actions in helping industries to outrun leaner and cleaner, and also aligns with an innovative process developed by our customer over many years. With this order, we will work on supporting an impactful industrial solution, bringing our technologies that are entirely scalable for future expansion. Our people are also using their expertise from mining and metals to ensure productivity and efficiency through centralized control rooms, production scheduling, and cost and resource modelling.”
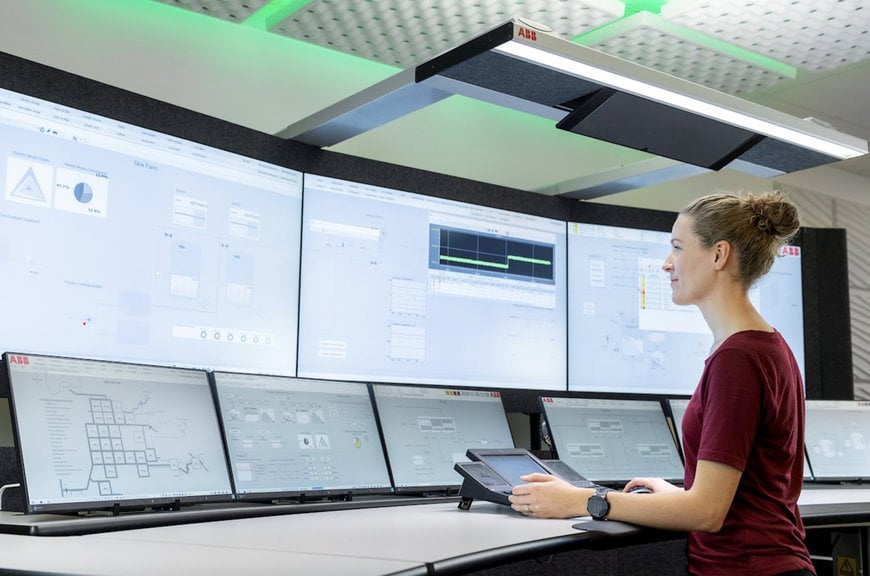
ABB Ability™ System 800xA® distributed control system (DCS) will enable the scaling up of GreenIron’s operations. Image ABB
ABB and GreenIron’s technologies are compatible with renewable, intermittent power sources like solar and wind. The goal is to contribute to the creation of a CO2-free value chain, from the extraction of ore to the production of steel and various metals. Together, these industries account for around eight per cent of global CO2 emissions, according to International Energy Agency (IEA) figures.
As industries undergo increased digital transformation, System 800xA remains key to ensuring safe, efficient and reliable operations, enabling the collection of valuable data and analytics for real-time insights. ABB’s DCS technology has been at the heart of process and energy industry operations for more than 40 years.
www.abb.com
ABB has been selected by GreenIron, an innovative Swedish company working in the mining and metals industries with its patented materials reduction technology, to provide automation and control system solutions for a first commercial facility in Sandviken, Sweden.
GreenIron’s hydrogen-based reduction technology will be industrialized for fossil-free and energy-efficient production of metals, producing fossil-free sponge iron that can then be used in industries such as steelmaking. A single furnace is expected to reduce carbon emissions by around 56,000 tonnes per year compared to traditional coal-based methods, with the only residual product being water. Scaling up to 300 furnaces would correspond to roughly 35 percent of Sweden's annual CO₂ emissions.
The integration of the ABB Ability™ System 800xA® distributed control system (DCS) will enable the scaling up of GreenIron’s operations. The powerful automation platform will manage the entire industrial process, with the capabilities to integrate control, safety and power management into one system. It will mean overall plant visibility for optimizations, efficiencies and better decision making based on data and insights.
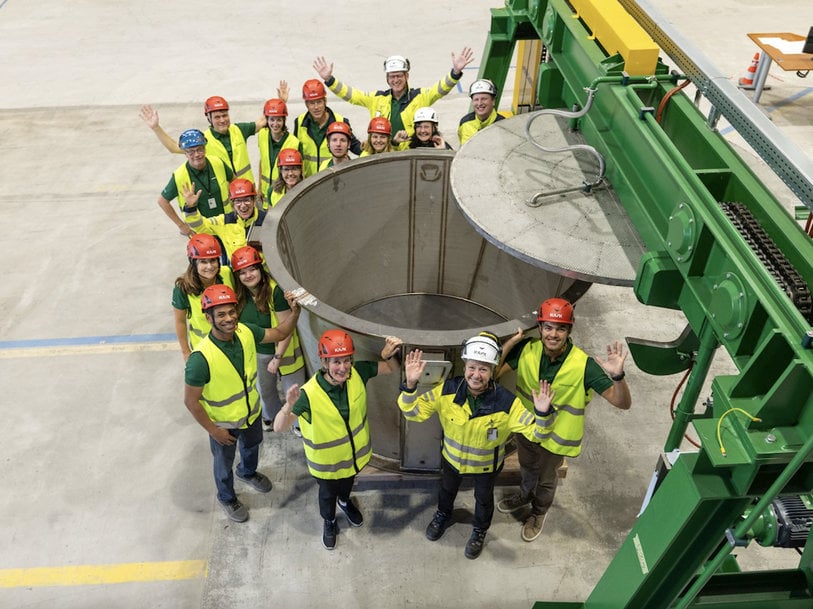
GreenIron is set to deploy its patented materials reduction technology for industrial applications. Image GreenIron
GreenIron paves the way for circular production processes by producing valuable raw materials from residual products such as landfills and residues as well as virgin ore. The sponge iron products can be used in steel or other metal fabrication processes, including electric arc furnaces, smelting plants and foundries.
“The collaboration with ABB is a crucial part of our scaling up and future growth as we commence commercial production,” said Ulrika Molander, Chief Operating Officer of GreenIron. “ABB’s system will enable us to make informed decisions, stabilize operations at every stage, and analyze data for our continued journey. It’s an exciting time for us.”
“Together with GreenIron we’re working on fulfilling sustainability objectives that are demanded by the metals industry and wider society,” said Martin Björnmalm, Local Business Line Manager for Metals, ABB Process Industries Sweden. “This is the type of project that underlines our actions in helping industries to outrun leaner and cleaner, and also aligns with an innovative process developed by our customer over many years. With this order, we will work on supporting an impactful industrial solution, bringing our technologies that are entirely scalable for future expansion. Our people are also using their expertise from mining and metals to ensure productivity and efficiency through centralized control rooms, production scheduling, and cost and resource modelling.”
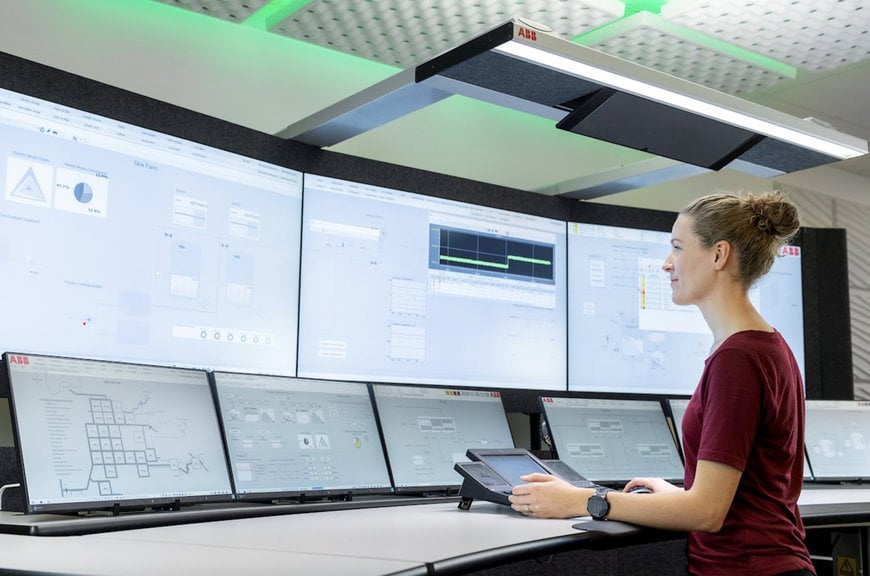
ABB Ability™ System 800xA® distributed control system (DCS) will enable the scaling up of GreenIron’s operations. Image ABB
ABB and GreenIron’s technologies are compatible with renewable, intermittent power sources like solar and wind. The goal is to contribute to the creation of a CO2-free value chain, from the extraction of ore to the production of steel and various metals. Together, these industries account for around eight per cent of global CO2 emissions, according to International Energy Agency (IEA) figures.
As industries undergo increased digital transformation, System 800xA remains key to ensuring safe, efficient and reliable operations, enabling the collection of valuable data and analytics for real-time insights. ABB’s DCS technology has been at the heart of process and energy industry operations for more than 40 years.
www.abb.com